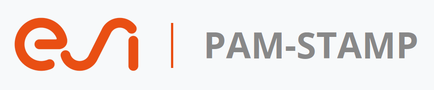
PAM-STAMP – sajtolási szimulációs megoldás
Megoldások a lemezes alkatrészek tervezése és a sajtolási szimulációk számára
A PAM-STAMP nevű szerszámtervezési és síklemezalakítási szimulációs szoftverünkkel a mérnökök számítógépükön gyorsan megtervezhetik, optimalizálhatják és ellenőrizhetik a sajtolási folyamatokat. A PAM-STAMP megoldás a hideg- és melegalakítás, hotformázás és csőalakítási folyamatokra, képes bárminemű terítékkel dolgozni, beleértve a több darabos és változó vastagságú terítékeket, és használandó minden fém alakítást felhasználó iparágban, mint például az autóipar, az aeronautika vagy a műszertechnika.
Az ajánlatkészítés szakaszában a felhasználók meghatározhatják az teríték körvonalait és annak optimális elhelyezését a lemezen az anyagköltség becsléséhez, és gyorsan kidolgozhatják a fémlemez-alakító szerszámokat. A megvalósíthatósági szakaszban a tervezők a B-Spline geometria alapján szerszámfelületeket modellezhetnek, és sikeresen megtervezhetik az alakítási folyamatot repedések és ráncok nélkül, az előírásoknak megfelelően, ideértve a peremezést, a vágási folyamat fejlesztését és a vágási él, illetve a teríték optimalizálását. A validációs szakaszban a mérnökök pontosan meg tudják becsülni a visszarúgózás mértékét, kompenzálhatják a szerszámokat mélyhúzás és többműveletes alakítás során is, valamint észlelhetik és megjeleníthetik a kozmetikai hibákat ugyanúgy, mintha a gyártósoron lennének. A megvalósít-hatósági és az érvényesítési szakaszban a szoftverbeállítások között nincs különbség, ami biztosítja a lehető legjobb elérhető eredményt.
De mi még itt nem állunk meg …
A 3D sajtolószerszámok hűtési hatékonyságának hitelesítése a hotformázási folyamatban hőátadással vagy valódi folyadékáramlási (CFD) elemzéssel lehetséges. Mivel a gyártás befolyásolja az anyag tulajdonságait, amelyek viszont hatással vannak a termék teljesítményére, az alakítási folyamat eredményei felhasználhatók a hegesztési szerelési folyamat tervezésére, azzal a céllal, hogy a szerelvény tűréshatárokon belül maradjon, és javuljon a termék teljesítménye. Végül a mérnökök megjeleníthetik és áttekinthetik az eredményeket egy virtuális valóság környezetben. A virtuális prototípuskészítés biztosítja, hogy az alkatrészek gyártási és összeszerelési folyamatai a megtervezett termékleírásokat és teljesítményt időben és költségvetésen belül teljesítsék. Az ESI teljeskörű megoldásokat kínál könnyű formatervezésű minták virtuális prototípusának kialakításához, amelyek ugyanolyan jók, mint a valódi prototípusok, így a tervezők a megfelelő döntéseket hozhatják meg.
Olvassa el kérem a “Die Face Design Solution Cuts Tooling Development Time” cikket az Engineering.com szakfolyóiratban és tudjon meg többet a PAM-STAMP lehetőségeiről (angol nyelven).
További információk: az ESI PAM-STAMP a sajtóban
Az aktív szerszámfelületek automatizált tervezése lehetővé teszi a megvalósíthatósági analízisek korai elvégzését a lemezalakítási modellek esetében
Hibaelhárítási eszközök
A szoftver támogatja a szerszámtervezést és összeállítást a hotforming technológiák számára is
Az
elsődleges
tervektől
és a koncepciótól a virtuális valóságig. Komplex megoldás a
sajtolómérnökök számára – és ami mögötte van.
Szerszámtervezés
A CATIA V5 környezetbe teljeskörűen integrált PAM-DIEMAKER és PAM-TFA for Catia V5 szimulációs megoldások a a fémek alakításához szükséges szerszámok és folyamatok tervezésének és gyártásának támogatására.
PAM-STAMP – sajtolási szimulációs megoldás
A kezdeti tervektől / koncepcióktól a kipróbálásig
Bármely adott fémmegmunkálási eljáráshoz ma mindent elhelyezhetünk egy virtuális mérnöki környezetben – a vevői igények részletezésétől a végtermék gyakorlati ellenőrzéséig, valamint a gyártóberendezések felállításáig. Ez magában foglalja az anyagköltség-becslést, a szerszámtervezést és a megvalósíthatóságot, az alkatrész-tervezés validálását és az eszközkészlet-tervezési és -formálási folyamatokat.
Az alábbiakban egy összefoglalást talál a virtuális sajtolástechnikai mérföldkövekről és elemekről, amelyek kiválóan kitűnhetnek, az ESI lemezalakítási szimulációs szoftverével és megoldásaival – a sajtolás szimulációjától a termékkialakítás, tervezés, az alkatrészek és a szerszámok gyártásáig – és egyéb más részleteket is.
A mérnökök termelékenységének növelése – Mi áll rendelkezésre és hogyan működik:
- A topológia ellenőrzése, tisztítása és javítása
- Az anyagköltségek meghatározása
- A B-Spline geometriáján alapuló következő generációs szerszámtervezés
- Gyors kapcsolat a szimulációval
- Pontos numerikus módszerek
- Geometriai ráncgátlók
- Visszarúgózás – kinematikai felkeményedés
- Vasalás
- Hármas sebességű üzemmód a lenyűgözően rövid szimulációs idők eléréséhez
- A ráncok és a gyűrődések pontos előrejelzése – numerikus ellapulás nélkül
- A teríték és a vágóél optimalizálása
- Nagy szakítószilárdságú acélok visszarugózása
- (Többlépcsős) kompenzáció
- A teljes sajtolási lánc virtuális prototípusa
- Szépséghibák
- Testreszabás
- Kiváló minőségű eredmények, költségek és idő kompromisszumok nélkül
- Hotformázás, End-to-End Virtuális Prototipuskészítés
- Kapocs a gyártástechnika és a prototípusok összeszerelése között
- Virtuális Valóság
A topológia ellenőrzése, tisztítása és javítása
A kontaktfelületek pontos leírása, mint a pontos háló alapja a pontos eredmények kulcsa – a kezdetektől. Különösen akkor, ha a mérnököknek idegen szerszámfelületekkel kell dolgozni, és a különböző rendszerek közötti adatcserére van szükség, a geometriában topológiai problémák merülhetnek fel. Szükség lehet a lyukak kitöltésére és a repedések kijavítására, vagy a geometria tökéletesítésére oly módon, hogy a szerszám felületének hálója a lehető legjobb szimulációs eredményeket adja.
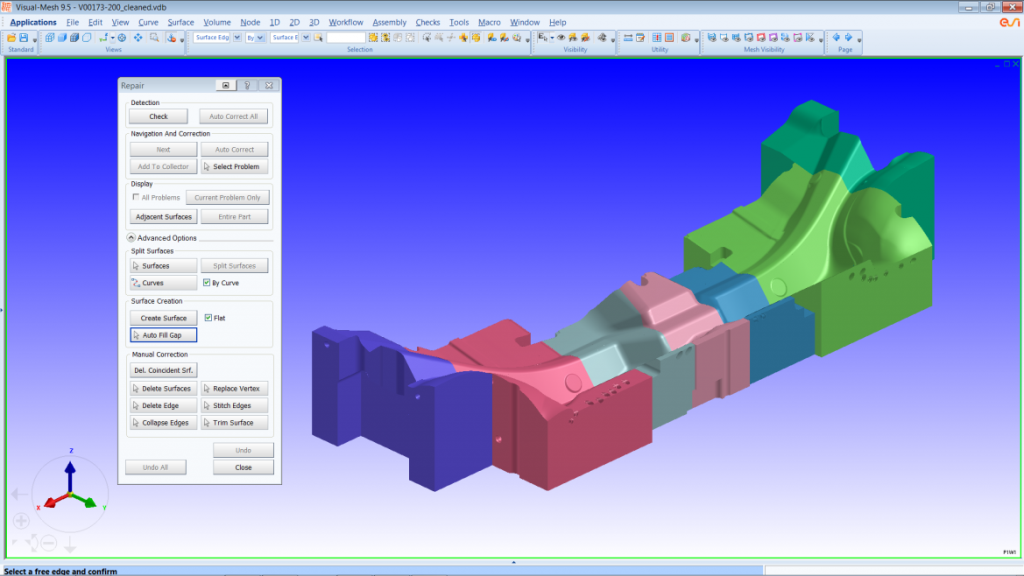
A műszerfal meleg alakító kovács szerszámának alsó része – A topológia ellenőrzése és így az érintkező felületek pontos ábrázolása garantálja a pontos eredményeket – az AP&T hozzájárulásával
Természetesen mindig választhatjuk az automatikus útvonalat – de rossz minőségű topológia esetén ez gyengébb minőségű eredményt eredményezhet, s ez nem azonosított repedések vagy ráncok kialakulásához vezethet. Hogy a lehető legjobb topológiával dolgozhasson, A VISUAL MESH lehetővé teszi bármilyen topológia ellenőrzését, tisztítását és javítását még a szimulációs munkák megkezdése előtt. Szintén lehetőség van a geometria módosítására és bármilyen már kész háló módosítására attól függetlenül, hogy az milyen rendszerben készült. Rövid időn belül lehetséges bármilyen topológiát vagy hálót olyan állapotba hozni, amely a pontos kontaktok használatával garantálja a lehető legjobb szimulációs eredményeket.
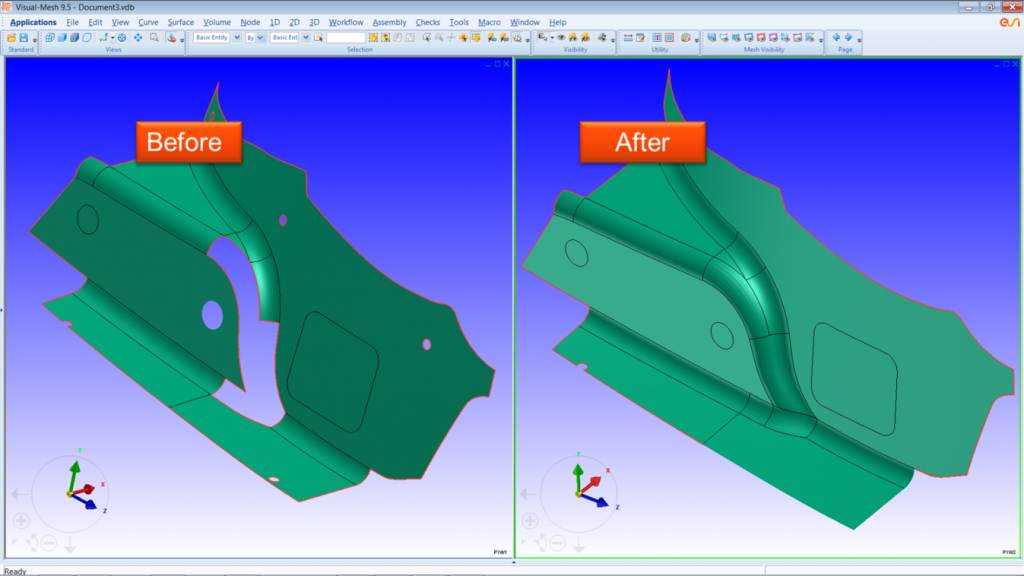
A topológia javítása a szerelési tűréshatár elérése érdekében
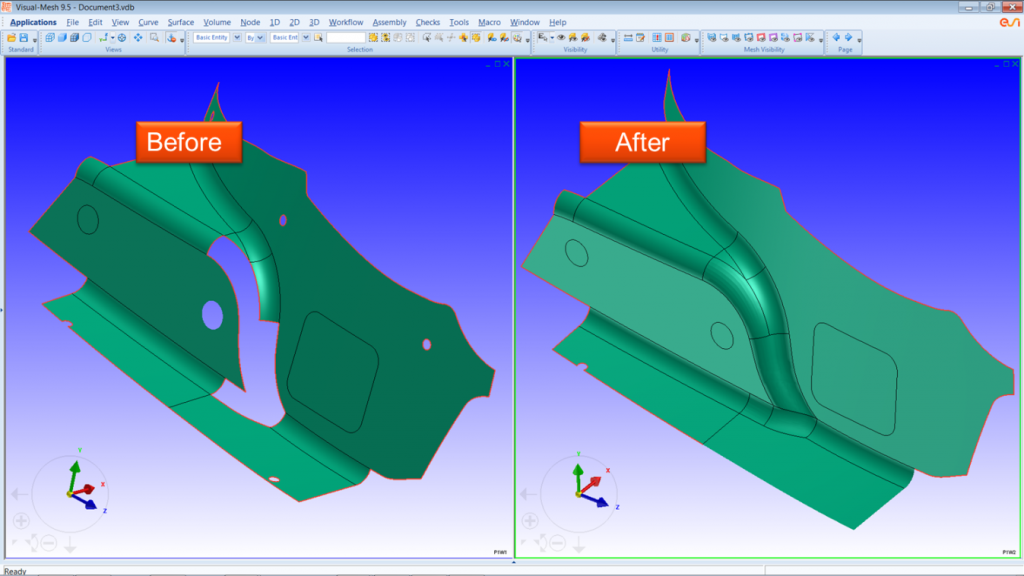
A hiányzó vagy rossz felületek javítása
A mérnökök termelékenységének növelése – Mi áll rendelkezésre és hogyan működik:
- A topológia ellenőrzése, tisztítása és javítása
- Az anyagköltségek meghatározása
- A B-Spline geometriáján alapuló következő generációs szerszámtervezés
- Gyors kapcsolat a szimulációval
- Pontos numerikus módszerek
- Geometriai ráncgátlók
- Visszarúgózás – kinematikai felkeményedés
- Vasalás
- Hármas sebességű üzemmód a lenyűgözően rövid szimulációs idők eléréséhez
- A ráncok és a gyűrődések pontos előrejelzése – numerikus ellapulás nélkül
- A teríték és a vágóél optimalizálása
- Nagy szakítószilárdságú acélok visszarugózása
- (Többlépcsős) kompenzáció
- A teljes sajtolási lánc virtuális prototípusa
- Szépséghibák
- Testreszabás
- Kiváló minőségű eredmények, költségek és idő kompromisszumok nélkül
- Hotformázás, End-to-End Virtuális Prototipuskészítés
- Kapocs a gyártástechnika és a prototípusok összeszerelése között
- Virtuális Valóság
Az anyagköltségek meghatározása
Az autó karosszériák néhány száz fém alkatrészből készülnek. A gyártási folyamat során ezeket a háromdimenziós alkatrészeket kétdimenziós lemezből vágják ki, mielőtt préselik és (pont- vagy lézer) hegesztéssel robotok által összehegesztik őket. A kétdimenziós lemez hosszú szalagok formájában áll rendelkezésre, melyek jobban “tekercsekként” ismertek, amelyek eltérő szélességűek, különböző anyagi tulajdonságokkal és árral rendelkeznek, és amelyeknek a vastagsága a tekercs mentén akár eltérő is lehet. Ha az alkatrész geometriáját tekintjük kiindulási pontnak, akkor az alkalmazás gyorsan kidolgozhatja az alkatrész síkba történő kiterítését, így hozva létre a terítéket, és meghatározhatja a terítékek optimális elhelyezkedését a tekercsen, a legkisebb anyagköltségeknek megfelelően. Az alábbiakban néhány mondatban ismertetjük az általános munkafolyamatot és a végrehajtandó feladat hatékony végrehajtásához rendelkezésre álló funkciókat.
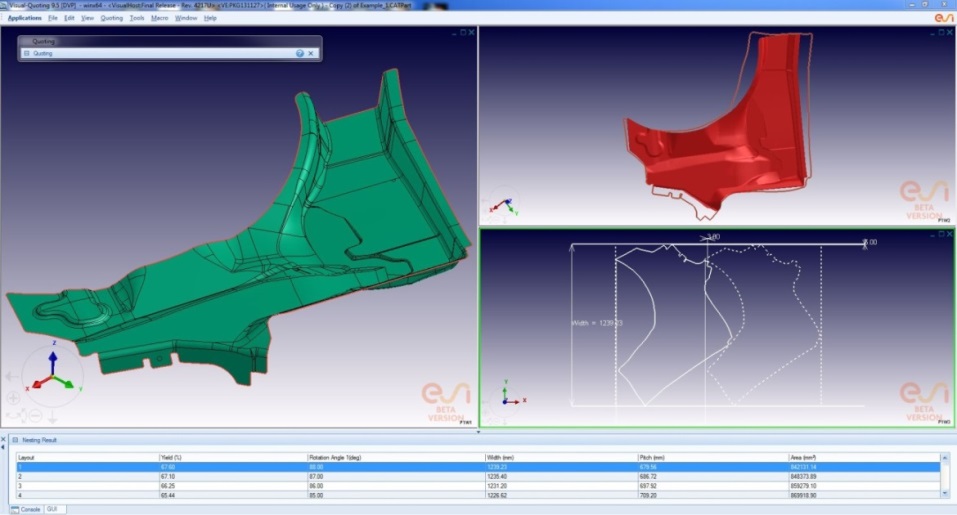
Anyagköltség becslés – a teríték körvonala és annak elhelyezése a lemezre
Az alkatrész geometriájának meghatározása
Az alkatrész felület- vagy térfogat-modellként importálható. Különleges funkció áll rendelkezésre a térfogat-modell felső és alsó felületének kinyerésére, valamint a medián felületek előállítására, hogy az alkatrész geometriájának kiterítése a semleges szálon helyesen kiszámítható legyen. A szükséges anyag- és vastagsági információk hozzárendelhetőek a kiválasztott alkatrészhez.
A teríték körvonala
Az ajánlattételi megoldás az ESI GROUP egylépcsős, a maga osztályában legjobb megoldóján alapul. A lehető legrövidebb idő alatt, az alkatrész teljes 3D modellje és számos folyamatparaméter, mint például a leszorítóerő, a lemez anyagának és vastagságának figyelembe vételével pontosan meghatározza az alkatrész terítékét (bár alávágott részek is keletkezhetnek). A kidolgozott teríté-ken kívül az alkatrész megvalósíthatósága közvetlenül és alaposan elemezhető különböző kontúrok, például elvékonyodás, vastagság eloszlás és az alakíthatósági határvonal-diagram (FLD) felhasználásával. Támogatva van a teríték kontúrjának egyenes beolvasása is.
A teríték elhelyezése a lemezen
A kifejlesztett teríték felhasználható annak a lemezre való elhelyezés folyamatában. A körvonal finomítható, és lehetőség van kiegészítő rész alkalmazására vagy az anélkül is elhelyezhető a körvonal konstans megnövelésével. Az anyag optimális kihasználásának számításakor a teríték több elrendezése támogatott, mint például az „Egy felül“, „Kettő felül“, „Tükör“ vagy a „Transzfer szerszám“.
A jelentések automatikus létrehozása
A megoldás gyors és automatizált jelentésgenerátort tartalmaz az alkatrész anyagának árajánlatára. Ez a funkció magában foglalja az anyagfelhasználást, a hulladékot, a terítékek egymástól való távolságát, a tekercs szélességét, a terítéket és a terítékek sorrendjének képeit a szalagon, valamint a kifejlesztett teríték körvonalát.
A mérnökök termelékenységének növelése – Mi áll rendelkezésre és hogyan működik:
- A topológia ellenőrzése, tisztítása és javítása
- Az anyagköltségek meghatározása
- A B-Spline geometriáján alapuló következő generációs szerszámtervezés
- Gyors kapcsolat a szimulációval
- Pontos numerikus módszerek
- Geometriai ráncgátlók
- Visszarúgózás – kinematikai felkeményedés
- Vasalás
- Hármas sebességű üzemmód a lenyűgözően rövid szimulációs idők eléréséhez
- A ráncok és a gyűrődések pontos előrejelzése – numerikus ellapulás nélkül
- A teríték és a vágóél optimalizálása
- Nagy szakítószilárdságú acélok visszarugózása
- (Többlépcsős) kompenzáció
- A teljes sajtolási lánc virtuális prototípusa
- Szépséghibák
- Testreszabás
- Kiváló minőségű eredmények, költségek és idő kompromisszumok nélkül
- Hotformázás, End-to-End Virtuális Prototipuskészítés
- Kapocs a gyártástechnika és a prototípusok összeszerelése között
- Virtuális Valóság
A B-Spline geometriáján alapuló következő generációs szerszámtervezés
Manapság a szerszámok aktív felületeinek tervezése egyre inkább a CAD környezetekben történik. Az iterációk közvetlenül a CADen belül natív CAD adatokon történnek. A szerszámtervezéshez használt eszköznek támogatnia kell a felhasználót a folyamat tervezési ciklusának minden szakaszában: a nagyon korai konceptuális fázistól a megvalósíthatósági tanulmányokon keresztül a végső validálásig. Ezen egymástól független lépések mindegyikéhez meg kell határozni a teljesítmény és a pontosság szempontjából optimális értéket. A szerszámfelület kialakításának a B-Spline geometriáján kell alapulnia annak érdekében, hogy a megoldás gyors, hatékony, rugalmas és megfeleljen az autóipar szabványainak. A szükséges geometriai változások miatti esetleges késéseket ki kell küszöbölni. A felületeknek pontosaknak kell lenniük, hogy garantálják az kontakt felületek pontos leírását és a pontos szimulációs eredményeket – a lehető leghamarabb
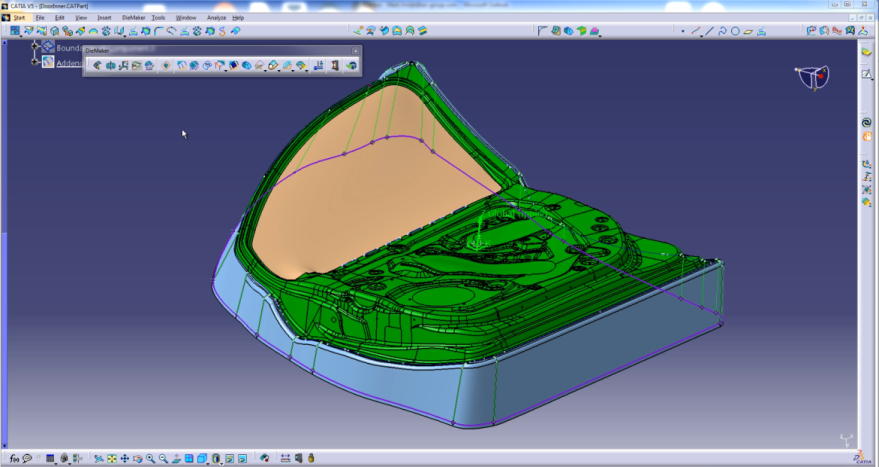
Az ajtó belső részének aktív szerszámfelülete – B-spline geometria alapján
Kihívás az ügyfél számára
Az autóipari préselt alkatrészek a tervezési osztálytól származnak, és gyakran csak az esztétikát (külső panelek) vagy a funkcionalitást (megerősítések, tartók stb.) veszik figyelembe. Általában nem vagy csak nagyon kevés figyelmet fordítanak a gyárthatóságra. Ez a folyamattervezési osztály vagy a szerszámkészítő feladata: megtalálni a módját, hogyan lehet robusztus és költség-optimalizált módon alkatrészeket létrehozni. Az esetek többségében az idő alatti nyomás óriási (és egyre növekszik), de a szerszámfelület kialakításának és folyamatának számtalan változatát meg kell vizsgálni, mielőtt az optimális alak (gyárthatóság és költség!) megtaláltatik.
Jellemző munkamenet
Az alkatrész geometriájából kiindulva, az első húzószerszám szerszámfelületének kialakítása gyorsan elkészíthető, és az általános megvalósíthatóság szempontjából, mint például a repedések és ráncok kialakulása, kiértékelhető. Mivel az első javaslat általában nem felel meg az összes kritériumnak, iterációs hurkokat futtatnak a szerszámfelület kialakításának és a préselési folyamat paramétereinek optimalizálására. Ezek az iterációk általában a következő tevékenységekből állnak:
Teljes vagy részleges alkatrész-módosítás a tervezési osztálytól
Geometriai kiegészítésmódok a ráncok, repedések kiküszöbölésére vagy a vágási feltételek optimalizálására
Folyamatmódosítások a repedések és ráncok kiküszöbölése, és a folyamat általános robusztusságának javítása érdekében
A teríték méretének csökkentése az anyagköltség-optimalizálás érdekében
Javasoljon alkatrész-módosításokat arra az esetre, ha a megvalósítható vagy robusztus folyamat nem garantálható
Az első javaslat tervezete általános megvalósíthatóságának igazolása után további műveletek kerülnek bevonásra a folyamattervezésbe (vágás, szegélyezés, hajlítás, kalibrálás.), úgy a geometriai kialakítás, mint a szimuláció validálásának esetében. A repedések és ráncok elemzése, valamint a nyomóerő becslése mellett ebben a szakaszban más kritériumok is relevánssá vállnak, mint pl. a külső panelek kozmetikai hibáinak elemzése, és a mélyhúzó szerszámok visszarugózásának kompenzációja. Végül, az utolsó lépésként, a folyamat tervezésének teljes validációja után, a gyártószerszámok marására kerül sor.
Kulcsképességek
A speciális szerszámtervezési megoldás integrálása a CAD környezetbe hatalmas előnyöket kínál a szokásos CAD alkalmazásokhoz és a hálón alapuló eszköztervezési megoldásokhoz képest:
A CAD szokásos használatához képest minimalizálja a szerszámkészítők munkaterhelését az eszköztervezés és a folyamatismeret megvalósításával, és figyeli az aktív szerszámfelületek tervezésének természetes folyamatát.
Az integráció nagy teljesítményű interaktív eszközöket és funkciókat kínál, amelyek útmutatást és támogatást nyújtanak az alkatrészek előkészítésében, a leszorítók és a szerszámtestek fejlesztésében, valamint gyors hozzáférést biztosítanak a fontos folyamatadatokhoz, például a vágási szögviszonyokhoz és a vágási él geometriájához.
Egyesíti a szerszámfelület gyors kialakításának kényelmét és sebességét a natív CAD felület minőségével. Ezért a legmagasabb minőségi szimulációs eredmények várhatók – már a kezdetektől.
A teljes CAD alapú kialakítás kiküszöböli a hálón alapuló modellnek a CAD környezetben való újragenerálásának szükségességét, vagyis ugyanannak a munkának kétszeri elvégzését. Ugyanaz a modell használható a fejlesztési folyamat minden szakaszában, a korai (megvalósíthatósági) státustól egészen a modell marásáig.
A CAD-integrációnak köszönhetően az összes natív CAD funkció használható az optimális kialakítás eléréséhez anélkül, hogy szükségesek lennének kompromisszumok a háló-alapú szerszámgép tervező szoftver korlátozásai miatt.
Könnyű és gyors iterációk az adott alkatrész cseréje során: néhány perc alatt az eredeti alkatrész geometriája kicserélhető az elem legújabb verziójára. A teljes szerszámot már nem kell manuálisan újratervezni.
A szimulációs környezettel való szoros kapcsolatnak köszönhetően a gyors és egyszerű szimulációs iterációk elvégezhetőek sok felhasználói beavatkozás és a geometriai pontosság elvesztése nélkül.
Fő előnyök
Költségek csökkentése a legmodernebb megoldások alkalmazásával a szerszámok aktív fejlesztése során, amelyek mindjárt az első alkalommal kivitelezhetőek.
A prototípus és a gyártás sikerének biztosítása először a virtuális prototípus tesztelésével: a termelési problémák elkerülésének stratégiája
Idő nyerése: nincs szükség a szerszám aktív felületeinek a háló referencia alapján történő újjáépítésre CAD környezetben
A fejlesztési folyamat utolsó szakaszában az új alkatrészváltozatok is könnyen és gyorsan megvizsgálhatók a CAD adatok integrált intuitív cserefunkciójának köszönhetően.
Gyors tanulási görbe az új felhasználók számára: már nagyon kevés képzés mellett a CAD rendszerekben kevésbé járatos szakemberek is rendkívül hatékonnyá válhatnak a gyártásra kész szerszámtervek kialakításában
A formatervezési termék könnyen integrálható a meglévő fogadó PLM struktúrába
A mérnökök termelékenységének növelése – Mi áll rendelkezésre és hogyan működik:
- A topológia ellenőrzése, tisztítása és javítása
- Az anyagköltségek meghatározása
- A B-Spline geometriáján alapuló következő generációs szerszámtervezés
- Gyors kapcsolat a szimulációval
- Pontos numerikus módszerek
- Geometriai ráncgátlók
- Visszarúgózás – kinematikai felkeményedés
- Vasalás
- Hármas sebességű üzemmód a lenyűgözően rövid szimulációs idők eléréséhez
- A ráncok és a gyűrődések pontos előrejelzése – numerikus ellapulás nélkül
- A teríték és a vágóél optimalizálása
- Nagy szakítószilárdságú acélok visszarugózása
- (Többlépcsős) kompenzáció
- A teljes sajtolási lánc virtuális prototípusa
- Szépséghibák
- Testreszabás
- Kiváló minőségű eredmények, költségek és idő kompromisszumok nélkül
- Hotformázás, End-to-End Virtuális Prototipuskészítés
- Kapocs a gyártástechnika és a prototípusok összeszerelése között
- Virtuális Valóság
Gyors kapcsolat a szimulációval
A gyors kapcsolat a szimulációval minimalizálja a szimuláció beállítására és az iterációk megvalósítására fordított időt
A sok iteráció támogatását, amely az autótervezés korai szakaszára jellemző, egy külön összeköttetéssel biztosított úgy a szerszámfelület kialakítása, mind a szimulációs környezet között. A virtuális prototípus készítésének végső célja az, hogy a présből kijövő alkatrész rögtön az „első alkalommal” jó legyen.
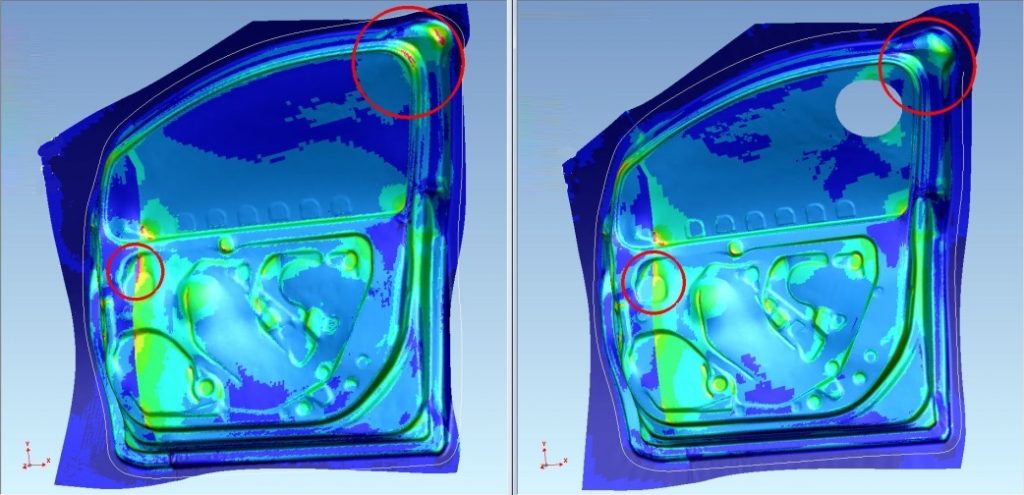
A szerszámtervezési folyamat közepén – gyors iterációk az eredmény minőségét befolyásoló kompromisszumok nélkül
Ehhez azonban előzetesen gyors iterációkra van szükség a szimulációs környezetben, hogy robusztus és megvalósítható megoldást találjon az alkatrész előállításához. Az első szimuláció általában messze van a végső megvalósítható tervtől. Ezen túlmenően ebben a szakaszban maga az alkatrész geometria is gyakran megváltozik: apróbb jellemzők hozzáadhatók vagy eltávolíthatók, vagy az alkatrészek teljesen áttervezhetőek. Korábban az eszköz CAD modelljét további kiegészítő információk nélkül importálták. Meg kellett határozni a teríték határvonalát és a ráncgátlókat, azok adataival és tulajdonságaikkal együtt, ami végső szerszám időigényes előállítását eredményezte. Ez nehézkes és időigényes iterációt eredményezett sok manuális mérnöki munkával, s oka volt a projekt késedelmének és a túlköltekezésnek is. Ráadásul hibák is előfordultak az egyes iterációk között. Jelenleg az ESI Group összes a szerszámtervezést elősegítő megoldása CAD környezetbe került beépítésre (CATIA V5 és VISUAL). Ezek magukban foglalják az aktív szerszámfelületek tervezése és a szimuláción alapuló elemző eszköz közötti hatékony átmenetet, abszolút minimumra csökkentve a szükséges felhasználói interakciót.
A szimulációval való gyors kapcsolat a húzószerszám-szimuláció beállításához szükséges idő akár 80% -át megtakarítja. Nemcsak a geometriai adatokat (például a húzószerszám és a ráncgátló geometriáját) továbbítják, hanem a folyamat adatait is, mint a leszorítóerők, a ráncgátlók közötti távolság, az alkatrész anyagának meghatározása, az anyag vastagságának, valamint az anyag eltolódásának iránya, és végül megőrzésre kerülnek az autó koordinátái és a többi koordináta rendszer, ezzel támogatva a fejlett interdiszciplináris tervezést.
A mérnökök termelékenységének növelése – Mi áll rendelkezésre és hogyan működik:
- A topológia ellenőrzése, tisztítása és javítása
- Az anyagköltségek meghatározása
- A B-Spline geometriáján alapuló következő generációs szerszámtervezés
- Gyors kapcsolat a szimulációval
- Pontos numerikus módszerek
- Geometriai ráncgátlók
- Visszarúgózás – kinematikai felkeményedés
- Vasalás
- Hármas sebességű üzemmód a lenyűgözően rövid szimulációs idők eléréséhez
- A ráncok és a gyűrődések pontos előrejelzése – numerikus ellapulás nélkül
- A teríték és a vágóél optimalizálása
- Nagy szakítószilárdságú acélok visszarugózása
- (Többlépcsős) kompenzáció
- A teljes sajtolási lánc virtuális prototípusa
- Szépséghibák
- Testreszabás
- Kiváló minőségű eredmények, költségek és idő kompromisszumok nélkül
- Hotformázás, End-to-End Virtuális Prototipuskészítés
- Kapocs a gyártástechnika és a prototípusok összeszerelése között
- Virtuális Valóság
Pontos numerikus módszerek
Pontos numerikus módszerek – kulcs a pontos virtuális prototípuskészítéshez
A pontos kontakt definíció meggátolja a teríték csomópontjainak a szerszám elemeinek térfogatába történő bárminemű behatolását a számítás során. A csomópontok pontosan az elem felületén maradnak a pontosan kiszámított kontakt erőknek köszönhetően.
Napjainkban a PAM-STAMP minden explicit szimulációját pontos kontaktokkal és magas minőségű numerikus beállításokkal hajtják végre, függetlenül attól, hogy megvalósíthatósági vagy validációs szakaszban vannak-e. Pontos kontaktokkal alkalmaznak a hatalmas szimulációs modellekben is, amelyek egymillió vagy több elemből állnak. Ugyanakkor az explicit módszer, sok kicsi időléptékkel lehetővé teszi az anyagtörténet pontos integrálását a húzás fázisába. Az implicit oldók esetében nem lehetséges a pontos kontaktmodellt használni sokszámú kicsi időléptékkel nagy modellek esetében, ugyanis az túl időigényes lenne.
A pontos kontaktokkal történő munkavégzés, az anyagmodellek gyors és pontos beállítása és a kezdetektől pontos numerikus beállítások számos előnnyel jár:
Az validációs szakaszban nincs kockázata a későn felismert és így költséges problémáknak, mint például a megvalósíthatósági szakaszban használt különböző (kontakt vagy numerikus) beállítások okoznak repedések vagy ráncok. A pontos kontakt használata az összes szimulációs szakaszban, valamint a szerszám topológiájának és hálójának pontos ábrázolása a kezdetektől segít elkerülni ezt a problémát, amelyek egyébként nagyon időigényesek lehetnek a felmerült problémák kompenzálása esetében.
Az alakítás utáni képlékenység és a maradék feszültségek pontos kiszámítása garantált, ami a pontos visszarúgózás számítás előfeltétele.
Ez a pontos visszarugózás a legjobb alap a prediktív deformáció kompenzációra az alakítási oldalon vagy a végső összeszerelési folyamat során (hideg és meleg összeszerelés)
A pontos visszarúgózás pontos maradandó feszültségeket és képlékeny előélet-ismeretet igényel – ezek a prediktív teljesítményszimulációk alapvető alapjai.
A vasalási hatás figyelembe vehető
A sajtóerő pontosan előjelezhető
A pontos kontakt és a vasalás képezik a pontos préselés alapját – ami sok időt takaríthat meg, különösen a meleg alakító kovács szerszám kifejlesztésekor.
A pontos kontakt viszonylag számításigényes. Ugyanakkor a PAM-STAMP új háromszoros sebességű módjával (amelyre később hivatkozunk ebben a dokumentumban) a pontos numerikus beállításokkal történő szimulációk már a projekt legkorábbi szakaszában is lehetségesek. Következésképpen a megvalósíthatósági szakaszban lévő összes numerikus kompromisszum kizárható.
A mérnökök termelékenységének növelése – Mi áll rendelkezésre és hogyan működik:
- A topológia ellenőrzése, tisztítása és javítása
- Az anyagköltségek meghatározása
- A B-Spline geometriáján alapuló következő generációs szerszámtervezés
- Gyors kapcsolat a szimulációval
- Pontos numerikus módszerek
- Geometriai ráncgátlók
- Visszarúgózás – kinematikai felkeményedés
- Vasalás
- Hármas sebességű üzemmód a lenyűgözően rövid szimulációs idők eléréséhez
- A ráncok és a gyűrődések pontos előrejelzése – numerikus ellapulás nélkül
- A teríték és a vágóél optimalizálása
- Nagy szakítószilárdságú acélok visszarugózása
- (Többlépcsős) kompenzáció
- A teljes sajtolási lánc virtuális prototípusa
- Szépséghibák
- Testreszabás
- Kiváló minőségű eredmények, költségek és idő kompromisszumok nélkül
- Hotformázás, End-to-End Virtuális Prototipuskészítés
- Kapocs a gyártástechnika és a prototípusok összeszerelése között
- Virtuális Valóság
Geometriai ráncgátlók
A geometriai ráncgátlók jól kezelhetők a pontos kontakttal. Ez egy újabb hozzájárulás a számított eredmények magas színvonalához. Az új hármas sebességű üzemmód rövid válaszidőt biztosít az eredményminőség csökkentése nélkül. Az egyszerűsítésekre már nincs szükség.
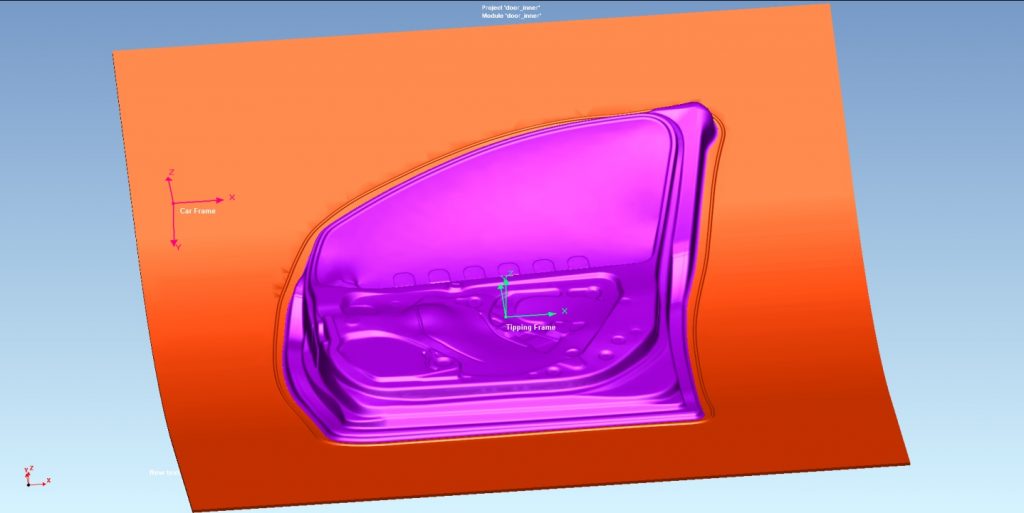
Geometriai ráncgátlók a szimulációban
A mérnökök termelékenységének növelése – Mi áll rendelkezésre és hogyan működik:
- A topológia ellenőrzése, tisztítása és javítása
- Az anyagköltségek meghatározása
- A B-Spline geometriáján alapuló következő generációs szerszámtervezés
- Gyors kapcsolat a szimulációval
- Pontos numerikus módszerek
- Geometriai ráncgátlók
- Visszarúgózás – kinematikai felkeményedés
- Vasalás
- Hármas sebességű üzemmód a lenyűgözően rövid szimulációs idők eléréséhez
- A ráncok és a gyűrődések pontos előrejelzése – numerikus ellapulás nélkül
- A teríték és a vágóél optimalizálása
- Nagy szakítószilárdságú acélok visszarugózása
- (Többlépcsős) kompenzáció
- A teljes sajtolási lánc virtuális prototípusa
- Szépséghibák
- Testreszabás
- Kiváló minőségű eredmények, költségek és idő kompromisszumok nélkül
- Hotformázás, End-to-End Virtuális Prototipuskészítés
- Kapocs a gyártástechnika és a prototípusok összeszerelése között
- Virtuális Valóság
Visszarúgózás – kinematikai felkeményedés
A fémlemez belsejében fennmaradó feszültségek a sajtolás után, közvetlenül az alkatrész szerszámból való eltávolítása előtt „visszarugózást” okoznak. Következésképpen a pontos visszarugózás előrejelzése pontos feszültség-előrejelzést igényel a sajtolás során. Azonban a szokásos anyagmodellek, például az izotróp felkeményedés nem tudják pontosan előrejelezni a feszültség állapotot. A következő kép prof. Yoshida előadásából (Hirosimai Egyetem) elmagyarázza, hogy a ciklikus feszültség-nyúlás sajtolás alatti lefolyása miért fontos a visszarúgózás elemzéséhez.
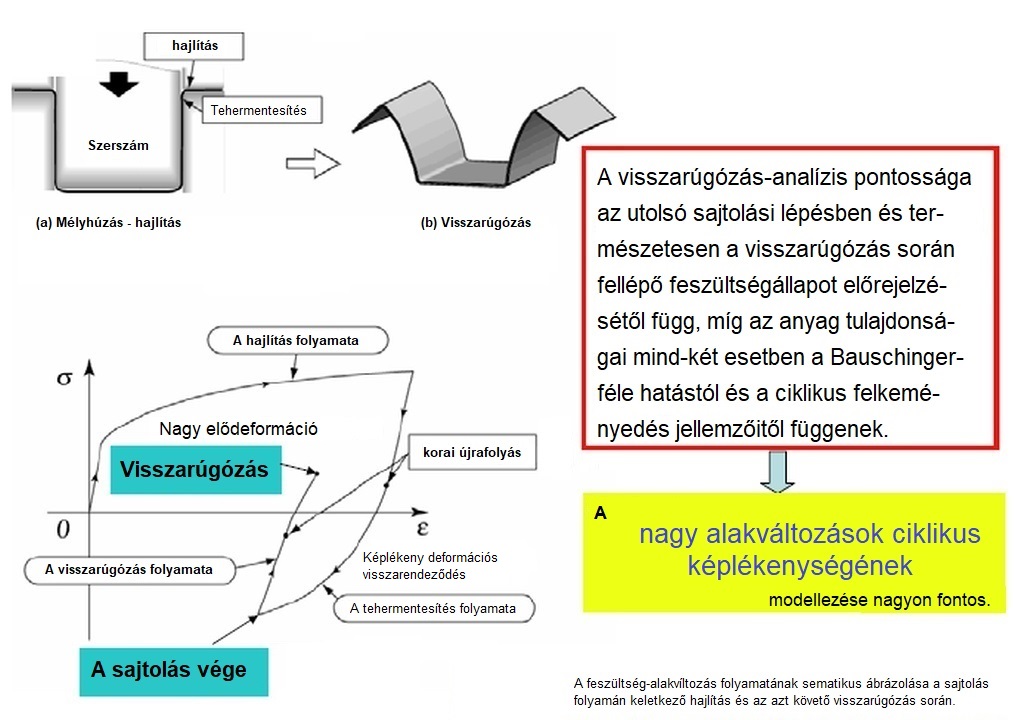
A modellezés fontossága a nagy nyúlású ciklikus plaszticitás esetében
A kinematikai felkeményedés Yoshida-Uemori (Y-U) modellje
Az anyagmodellezés ciklikus deformációja pontos leírása érdekében az anyagmodellben figyelembe kell venni a Bauschinger-hatást. Erre a célra egy kinematikus felkeményedési (KH) modellt alkalmaznak az izotropikus felkeményedési modell helyett. A meglévő KH modellek közül a Yoshida-Uemori modell a legjobb a fémlemez alakításához. Ennek oka az, hogy az Y-U modell csak a ciklikus plaszticitás hét paraméterét tartalmazza, és mindegyik paraméter fizikai meghatározással rendelkezik. Nincsenek mesterséges matematikai paraméterek. Ezenkívül a modellbe bevezették a Young modulusát a képlékeny feszültség függvényében, hogy pontosabban leírják a feszültség-nyúlás visszahatását a feszültség relaxáció után.
A következő képek szemléltetik az Y-U modell hatékonyságát a visszarúgás előrejelzésében, amelyről a TOA Industries Co., Ltd. számolt be. Az Y-U modellnek köszönhetően a visszarugózás előrejelzési pontossága drasztikusan javult a 980 MPa szakítószilárdságú, nagy szilárdságú acélból készült B-oszlop belső panelen. Következésképpen a TOA Industriesnek sikerült csökkentenie a fizikai próbák számát.
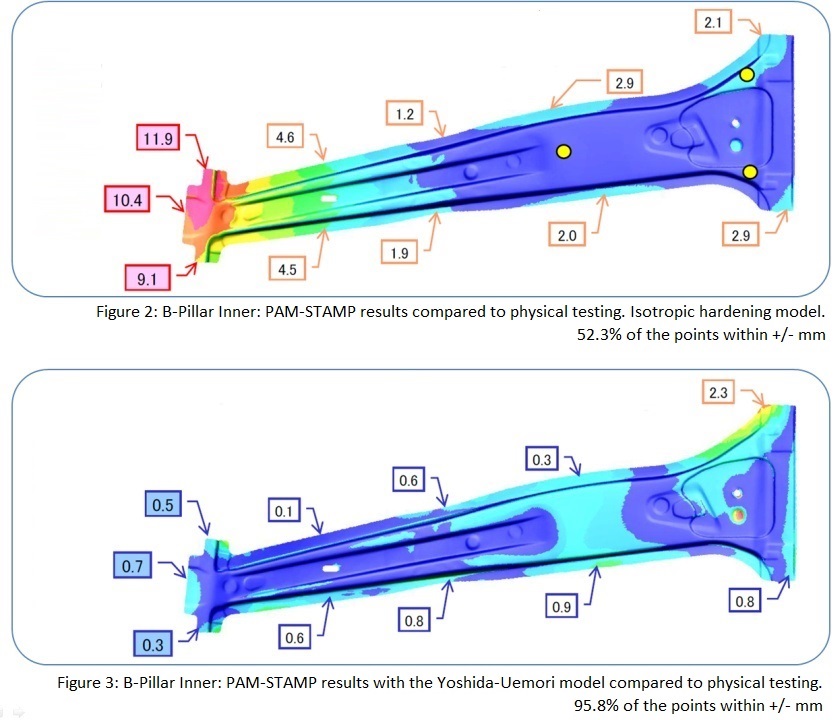
A visszarúgózás pontosságának növelése a Y-U modell segítségévelA
TOA Industries hozzájárulásával
Az anyagparaméterek azonosítása a ‘MatPara’ segítségével
Ha az anyagvizsgálat és a paraméterek azonosítása nehéz, akkor nehéz az anyagmodellt felhasználni a gyártásban, jóllehet maga az anyagmodell pontosabb eredményeket adhat. Hála a MatPara-nak, amelyet prof. Yoshida fejlesztett ki és az ESI, Group terjeszt, a Y-U modell anyagi paraméterei könnyen azonosíthatóak. Az alábbi ábra a „MatPara” -t mutatja, ahol a Y-U paramétereket az anyagpróbákból számítják ki, amelyek magukban foglalják a ciklikus húzó-nyomó vizsgálatokat és a törésig végzett szakítópróbát. A MatPara-ba integrált anyagadatbázisnak és a szoftver mögött meghúzódó erős optimalizálási technológiának köszönhetően az Y-U paramétereket akkor is meg lehet becsülni, ha csak a szakítópróba eredményei ismertek.
Y-U modell
A mérnökök termelékenységének növelése – Mi áll rendelkezésre és hogyan működik:
- A topológia ellenőrzése, tisztítása és javítása
- Az anyagköltségek meghatározása
- A B-Spline geometriáján alapuló következő generációs szerszámtervezés
- Gyors kapcsolat a szimulációval
- Pontos numerikus módszerek
- Geometriai ráncgátlók
- Visszarúgózás – kinematikai felkeményedés
- Vasalás
- Hármas sebességű üzemmód a lenyűgözően rövid szimulációs idők eléréséhez
- A ráncok és a gyűrődések pontos előrejelzése – numerikus ellapulás nélkül
- A teríték és a vágóél optimalizálása
- Nagy szakítószilárdságú acélok visszarugózása
- (Többlépcsős) kompenzáció
- A teljes sajtolási lánc virtuális prototípusa
- Szépséghibák
- Testreszabás
- Kiváló minőségű eredmények, költségek és idő kompromisszumok nélkül
- Hotformázás, End-to-End Virtuális Prototipuskészítés
- Kapocs a gyártástechnika és a prototípusok összeszerelése között
- Virtuális Valóság
Vasalás
A vasalás a visszarúgózás esetében – különösen a nagy szilárdságú acéloknál – és a folyamatokban végbemenő természetes jelenségeknél, mint például a kivágás-lyukasztás, használatos.
Azoknak a folyamatoknak a precíz kialakítása, amelyek során vasalás vagy kivágás (lyukasztás) történik, különleges véges elem (FE) formulációt igényel, amely figyelembe veszi a teljes keresztmetszetben létrejövő feszültségállapotot.

Kivágás – lyukasztás

Vasalás
A héjelemek általános formulációja nem elégséges ennek a jelenségnek a leírásához, ugyanis a feszültségek és a fajlagos nyúlások nem elég pontosan vannak meghatározva az elem normál irányában. Ezért a PAM-STAMP egy új típusú elemet vezet be a vasalás szimulációjára: a feszültséget annak teljes vastagságában figyelembe vevő elemet.
Ez az elem figyelembe veszi az elvékonyodást, a normál feszültséget és a 3D képlékeny elváltozást, melynek kiváltó oka a kétoldalú kontaktus. Amennyiben a vasalás jelensége létrejön, az elem automatikusan aktiválásra kerül, miközben kompatibilis a Yoshida-féle kinematikus felkeményedéssel, ami azt jelenti, hogy használható a fejlett visszarugózási szimulációk esetében.
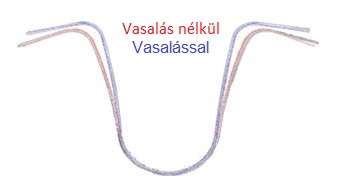
Grey: real test with/without ironingRed: PAM-STAMP results without ironingBlue: PAM-STAMP results with ironing
Szürke: valós teszt a vasalás figyelembe vételével/mellőzésével
Piros: PAM-STAMP eredmények a vasalás mellőzésével
Kék: PAM-STAMP eredmények a vasalás figyelembe vételével
A mérnökök termelékenységének növelése – Mi áll rendelkezésre és hogyan működik:
- A topológia ellenőrzése, tisztítása és javítása
- Az anyagköltségek meghatározása
- A B-Spline geometriáján alapuló következő generációs szerszámtervezés
- Gyors kapcsolat a szimulációval
- Pontos numerikus módszerek
- Geometriai ráncgátlók
- Visszarúgózás – kinematikai felkeményedés
- Vasalás
- Hármas sebességű üzemmód a lenyűgözően rövid szimulációs idők eléréséhez
- A ráncok és a gyűrődések pontos előrejelzése – numerikus ellapulás nélkül
- A teríték és a vágóél optimalizálása
- Nagy szakítószilárdságú acélok visszarugózása
- (Többlépcsős) kompenzáció
- A teljes sajtolási lánc virtuális prototípusa
- Szépséghibák
- Testreszabás
- Kiváló minőségű eredmények, költségek és idő kompromisszumok nélkül
- Hotformázás, End-to-End Virtuális Prototipuskészítés
- Kapocs a gyártástechnika és a prototípusok összeszerelése között
- Virtuális Valóság
Hármas sebességű üzemmód a lenyűgözően rövid szimulációs idők eléréséhez
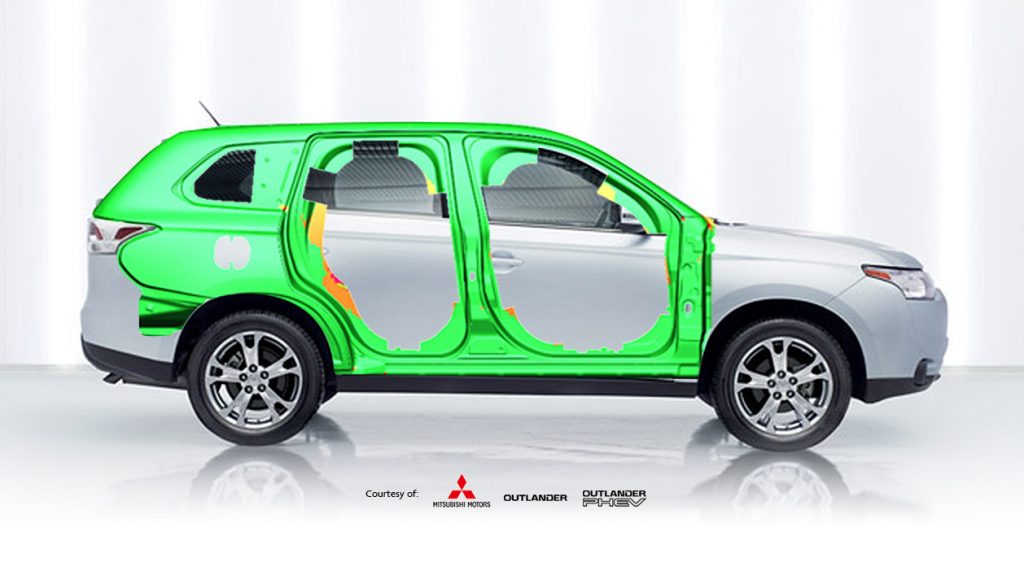
Hármas sebességű mód az explicit szimulációkhoz
A PAM-STAMP új megoldója lehetővé teszi az elemzés felgyorsítását ugyanúgy, mint a hagyományos numerikus hangolással, éspedig a minőség romlása nélkül. Pontosabban, a 3-4X elemzés felgyorsítás a mélyhúzási fázisban anélkül, hogy a minőség csökkenésével járna, lehetővé teszi a magas minőségű megvalósíthatósági tanulmányok elvégzését ugyanannyi idő alatt, mint amennyit a hagyományos megvalósíthatósági tanulmányok igényelnek.
A többmagos processzorokkal kombinálva nagyon rövid szimulációs idő érhető el. Az új megoldóval és egy négymagos processzorral akár 12-15 X-es sebességnövekedés lehetséges, összehasonlítva az az új megoldó nélküli egymagos szimulációval. A szimulációs idők már elég rövidek ahhoz, hogy az alakíthatósági szakasz pontosságát felhasználhassák a korai megvalósíthatósági szakaszban – mindezt a PAM-STAMP által biztosított precíziós formázási minőséggel. Következésképpen a továbbiakban nem szükséges kifejezetten a szimulációkat numerikus eszközökkel hangolni, azaz tömeg skálázással, numerikus beállításokkal, a hálónagyság növelésével stb. – a megvalósíthatósági futási idő elérése érdekében a gyengébb minőség árán. A megvalósíthatóság szakaszában a középszintű alapértelmezett beállítások használhatók. Mivel az új megoldó fejlesztése nem a minőség rovására történik, az a validációs / alakítási szakaszban is használható. Következésképpen a konzervatív mérnöki alapvető alapbeállításokkal ugyanazt a szimulációs időt vagy akár még rövidebbet is el lehet elérni, mint a hangolt alapértéknél. Az új megoldóval többé nem szükséges durvább hálókat vagy bármilyen más modell-egyszerűsítést használni a rövidebb szimulációs idő elérése érdekében. Ez lehetővé teszi a kiváló minőségű eredmények elérését, ésszerű szimulációs idővel a lehető legkorábbi szakaszban. Az alábbi ábra a hármas sebességű üzemmód hatékonyságát mutatja. Az ellenőrzéshez használt modellt a Mitsubishi Motors biztosította. A minőség elvesztése nélkül a hármas sebességű módban végzett számítások 3,7-szeresen gyorsabbak a normál üzemmódhoz képest.
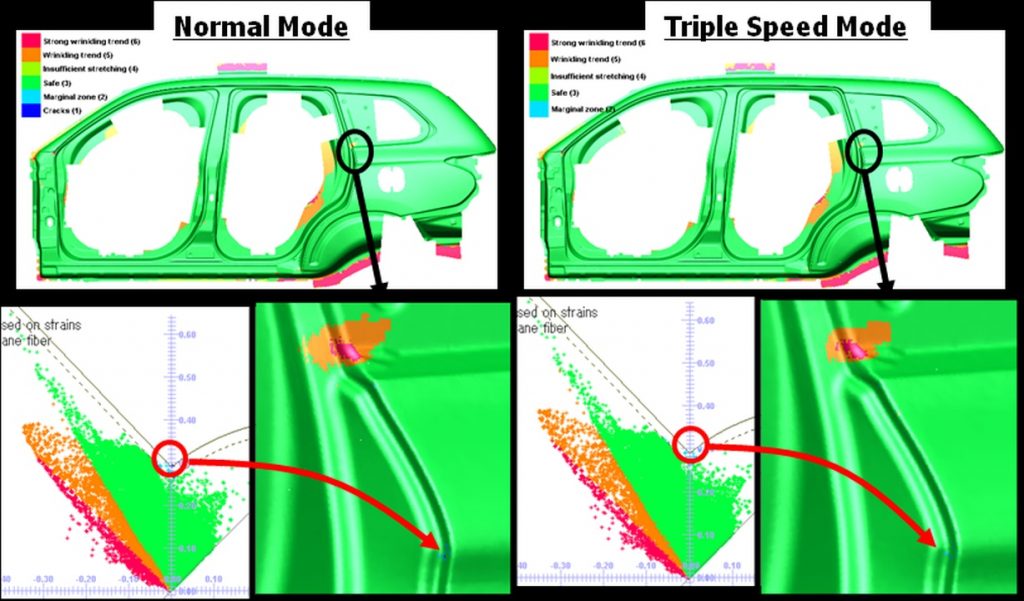
Stage | Calcultion time (h) | Calcultion time (h) | Ratio | Calculation type |
Normal | Triple | |||
Restrike | 4.11 | 1.1 | 3.74 | DMP 4 cores |
Szimulációk hármas sebességgel, A Mitsubishi Motors hozzájárulásával
A mérnökök termelékenységének növelése – Mi áll rendelkezésre és hogyan működik:
- A topológia ellenőrzése, tisztítása és javítása
- Az anyagköltségek meghatározása
- A B-Spline geometriáján alapuló következő generációs szerszámtervezés
- Gyors kapcsolat a szimulációval
- Pontos numerikus módszerek
- Geometriai ráncgátlók
- Visszarúgózás – kinematikai felkeményedés
- Vasalás
- Hármas sebességű üzemmód a lenyűgözően rövid szimulációs idők eléréséhez
- A ráncok és a gyűrődések pontos előrejelzése – numerikus ellapulás nélkül
- A teríték és a vágóél optimalizálása
- Nagy szakítószilárdságú acélok visszarugózása
- (Többlépcsős) kompenzáció
- A teljes sajtolási lánc virtuális prototípusa
- Szépséghibák
- Testreszabás
- Kiváló minőségű eredmények, költségek és idő kompromisszumok nélkül
- Hotformázás, End-to-End Virtuális Prototipuskészítés
- Kapocs a gyártástechnika és a prototípusok összeszerelése között
- Virtuális Valóság
A ráncok és a gyűrődések pontos előrejelzése – numerikus ellapulás nélkül
Ráncosodás
Különösen a hotformázás során a ráncok kialakulhatnak és eltűnhetnek. Abban az esetben, ha a folyamat végén nem simulnak ki, akár a szerszámot is tönkretehetik. A PAM-STAMP kompromisszumok nélkül szimulálja a ráncokat – ahogy a valóságban előfordulnának, beleértve a hajtogatást is. Csak az explicit szimulációs séma képes erre – a sok kis időléptéknek és a jelentős geometriai nemlinearitás kezelésének köszönhetően, anélkül, hogy lelassítaná vagy akár meg is állítaná a szimulációt.
A ráncok kialakulása az alakítás során – Az AP&T hozzájárulásával
A mérnökök termelékenységének növelése – Mi áll rendelkezésre és hogyan működik:
- A topológia ellenőrzése, tisztítása és javítása
- Az anyagköltségek meghatározása
- A B-Spline geometriáján alapuló következő generációs szerszámtervezés
- Gyors kapcsolat a szimulációval
- Pontos numerikus módszerek
- Geometriai ráncgátlók
- Visszarúgózás – kinematikai felkeményedés
- Vasalás
- Hármas sebességű üzemmód a lenyűgözően rövid szimulációs idők eléréséhez
- A ráncok és a gyűrődések pontos előrejelzése – numerikus ellapulás nélkül
- A teríték és a vágóél optimalizálása
- Nagy szakítószilárdságú acélok visszarugózása
- (Többlépcsős) kompenzáció
- A teljes sajtolási lánc virtuális prototípusa
- Szépséghibák
- Testreszabás
- Kiváló minőségű eredmények, költségek és idő kompromisszumok nélkül
- Hotformázás, End-to-End Virtuális Prototipuskészítés
- Kapocs a gyártástechnika és a prototípusok összeszerelése között
- Virtuális Valóság
A teríték és a vágóél optimalizálása
A sajtolási folyamat paramétereinek, például az erőknek és a ráncgátlóknak az optimalizálása, az azt követő folyamat robusztusságának ellenőrzése az anyagtulajdonságok és a folyamatváltozók természetes változásaihoz lassan alkalmazkodnak, mivel a számítógépes hardver és a szoftver technológia szinergikusan fejlődik, hogy csökkentse a számítási időt, és az optimalizálási és a robusztussági értékelések az alakítási szimuláció logikus kiterjesztésévé váljanak.
Az automatikus optimalizáló modul addig futtatja az iterációkat, amíg nem kapunk jó eredményt. A teríték optimalizált alakja és a vágóél segít az anyagspórolásban és csökkenti a vágási műveletek számát.
A teríték és a vágóél optimalizálása
A mérnökök termelékenységének növelése – Mi áll rendelkezésre és hogyan működik:
- A topológia ellenőrzése, tisztítása és javítása
- Az anyagköltségek meghatározása
- A B-Spline geometriáján alapuló következő generációs szerszámtervezés
- Gyors kapcsolat a szimulációval
- Pontos numerikus módszerek
- Geometriai ráncgátlók
- Visszarúgózás – kinematikai felkeményedés
- Vasalás
- Hármas sebességű üzemmód a lenyűgözően rövid szimulációs idők eléréséhez
- A ráncok és a gyűrődések pontos előrejelzése – numerikus ellapulás nélkül
- A teríték és a vágóél optimalizálása
- Nagy szakítószilárdságú acélok visszarugózása
- (Többlépcsős) kompenzáció
- A teljes sajtolási lánc virtuális prototípusa
- Szépséghibák
- Testreszabás
- Kiváló minőségű eredmények, költségek és idő kompromisszumok nélkül
- Hotformázás, End-to-End Virtuális Prototipuskészítés
- Kapocs a gyártástechnika és a prototípusok összeszerelése között
- Virtuális Valóság
Nagy szakítószilárdságú acélok visszarugózása
Nagy szakítószilárdságú acélok visszarugózása PAM-STAMP ben
A gépjárműipar és a repülőgépipar modern követelményei nagyobb szilárdságot és csökkentett súlyt jelentenek. Ez azt jelenti, hogy a korszerű járműszerkezetekben fokozottan használják a nagy szilárdságú acél- és alumínium alkatrészeket. A visszarugózás problémája a szerszámgyártási folyamat előterébe került. A legújabb generációs anyagoknál tapasztalt visszarugózás mértéke olyan magas, és az anyagok olyan erősek, hogy a prototípus kialakításánál nem lehetséges a visszarugózás korrekciója, a visszarugózást már a szerszámtervezés során kell kompenzálni.
Ultra magas szakítószilárdságú acél tulajdonságai
Magas folyáshatár
Rossz alakíthatóság
Jelentős mértékű visszarúgózás
A PAM-STAMPbe az utóbbi években számos fejlesztést került beépítésre, hogy segítse a mérnököket megbirkózni a rugózás kihívásaival:
A szerszám automatikus kompenzációjának modulja
Yoshida-Uemori anyagtani modell, amely sikeresen használható a nagy szakítószilárdságú acélok visszarugózásának szimulációjánál
A kontaktok pontos formulációja
Stabilitásvesztés érzékelése
Összenyomódás érzékelése
Teljes keresztmetszetben feszültséggel dolgozó elemmodell az anyag összenyomódásának és a vasalási folyamatnak a modellezésére
A mérnökök termelékenységének növelése – Mi áll rendelkezésre és hogyan működik:
- A topológia ellenőrzése, tisztítása és javítása
- Az anyagköltségek meghatározása
- A B-Spline geometriáján alapuló következő generációs szerszámtervezés
- Gyors kapcsolat a szimulációval
- Pontos numerikus módszerek
- Geometriai ráncgátlók
- Visszarúgózás – kinematikai felkeményedés
- Vasalás
- Hármas sebességű üzemmód a lenyűgözően rövid szimulációs idők eléréséhez
- A ráncok és a gyűrődések pontos előrejelzése – numerikus ellapulás nélkül
- A teríték és a vágóél optimalizálása
- Nagy szakítószilárdságú acélok visszarugózása
- (Többlépcsős) kompenzáció
- A teljes sajtolási lánc virtuális prototípusa
- Szépséghibák
- Testreszabás
- Kiváló minőségű eredmények, költségek és idő kompromisszumok nélkül
- Hotformázás, End-to-End Virtuális Prototipuskészítés
- Kapocs a gyártástechnika és a prototípusok összeszerelése között
- Virtuális Valóság
(Többlépcsős) kompenzáció
A (többlépcsős) szerszám kompenzációja PAM-STAMP-ben
A kozmetikai hibák értékelésén túl a pontos modellezés és a húzószerszám megfelelő folyamata is a sikeres kompenzáció feltétele.
Kompenzáció előtt
Kompenzáció után
Az alkatrészt 20 mm-es visszarugózással – például – nem szabadna kompenzálni. A kompenzáció alkalmazható a mélyhúzó műveleten, vagy akár a többlépcsős műveletsorra különböző stratégiák segítségével.
Kompenzációs rendszerek, melyek megtalálhatóak a PAM-STAMP-ben
Az Arcelor és a Renault a visszarúgózás kompenzációjának módszerét több alkatrészen is ellenőrizték:
Roof cross member, HE450M (FB600), thickness 1.8 mm, Courtesy of Renault
B-oszlop merevítése, acél minőségi osztálya: TRIP 800, lemezvastagság 1.2 mm
Az Atlas Tool, Inc. a PAM-STAMP szoftvercsomag segítségével fejleszti az visszarúgózási folyamat alapos kompenzációja folyamatának szimulációját
Olvassa el a teljes sikertörténetet (angol nyelven)
„A fejlett magas szakítószilárdságú acélok és részben a kétfázisú acélok egyre inkább elterjednek az autóipar beszállítói körében, ugyanis ezek használatával növelhető a biztonság a tömeg és a költségek párhuzamos csökkentése mellett. A fejlett szimulációs szoftver használata lehetővé tette számunkra áthidalni az ezen anyagok által okozott alakítási problémákat, és eleget tenni ügyfeleink elvárásainak a lehető legrövidebb idő alatt. Tapasztalatunk a PAM-STAMP szoftverrel karöltve jelentős versenyelőnyt jelent számunkra.“
Mark R. Schmidt, az Atlas Tool elnöke
A mérnökök termelékenységének növelése – Mi áll rendelkezésre és hogyan működik:
- A topológia ellenőrzése, tisztítása és javítása
- Az anyagköltségek meghatározása
- A B-Spline geometriáján alapuló következő generációs szerszámtervezés
- Gyors kapcsolat a szimulációval
- Pontos numerikus módszerek
- Geometriai ráncgátlók
- Visszarúgózás – kinematikai felkeményedés
- Vasalás
- Hármas sebességű üzemmód a lenyűgözően rövid szimulációs idők eléréséhez
- A ráncok és a gyűrődések pontos előrejelzése – numerikus ellapulás nélkül
- A teríték és a vágóél optimalizálása
- Nagy szakítószilárdságú acélok visszarugózása
- (Többlépcsős) kompenzáció
- A teljes sajtolási lánc virtuális prototípusa
- Szépséghibák
- Testreszabás
- Kiváló minőségű eredmények, költségek és idő kompromisszumok nélkül
- Hotformázás, End-to-End Virtuális Prototipuskészítés
- Kapocs a gyártástechnika és a prototípusok összeszerelése között
- Virtuális Valóság
A teljes sajtolási lánc virtuális prototípusa
A teljes sajtolási lánc virtuális prototípusa a PAM-STAMP környezetben
Kezdetekben a számítógépes modellezés a sajtolás folyamatának szimulációjára fókuszált, s az volt a célja, hogy eliminálja az anyag megrepedését vagy hullámosodását. A szimulációs technikák a visszarugózásra és annak kompenzációjára összpontosítanak. A PAM-STAMP szoftvercsomaggal lehetőség van a teljeskörű virtuális prototípusépítésre, amely magában foglalja a sajtolás folyamatának egészét, beleértve a következő folyamatokat:
Mélyhúzás és visszarúgózás
Kalibrálás és visszarúgózás
Hajlítás és visszarúgózás
Görgős szegélyezés és visszarúgózás
Ez segít a mérnököknek megőrizni az egész sajtolás feletti ellenőrzést, amely magasabb minőséget eredményez és kizárja a „meglepetéseket“ a valós prototípus építése közben.
A Hyundai hozzájárulásával
A precíz mérnöki munka a PAM-STAMP síklemezalakítási szoftvercsomag segítségével 80%-al csökkenti a többlépcsős szerszám bevezetési költségeit.
Olvassa el a teljes sikertörténetet
„A
számítógépes szimulációk csökkentették a megfelelő
raktári készletektől függő alakítási folyamat kifejlesztéséhez
szükséges időt és kiadásokat, éspedig az eredeti $18.000
a jelenlegi $3.600“, mondja
Rick Barnard, Precise Engineering vezérigazgatója.
„A
költségcsökkentés kulcsa az általunk tervezett sokrétű
szerszámok gyors és olcsó szimulációjához a PAM-STAMP
használata volt. A virtuális többlépcsős szerszám
elkészítésével annak befejezését áthelyeztük
a sajtolóműhelyből a tervezőirodába, ahol az
gyorsabban végrehajtható, és függetlenek vagyunk
a sajtológépektől is. Sikerült meghatároznunk a folyamatot,
kifejlesztettük a szükséges terítéket, pontosan meghatároztuk
az anyag folyásának menetét az első sajtolási művelet közben,
kiértékeltük a visszarúgózás hatását a végső
tűréshatárokra és figyelemmel kísértük a falelvékonydás
mértékét anélkül, hogy elkezdtük volna szerszámunk gyártását.“
A mérnökök termelékenységének növelése – Mi áll rendelkezésre és hogyan működik:
- A topológia ellenőrzése, tisztítása és javítása
- Az anyagköltségek meghatározása
- A B-Spline geometriáján alapuló következő generációs szerszámtervezés
- Gyors kapcsolat a szimulációval
- Pontos numerikus módszerek
- Geometriai ráncgátlók
- Visszarúgózás – kinematikai felkeményedés
- Vasalás
- Hármas sebességű üzemmód a lenyűgözően rövid szimulációs idők eléréséhez
- A ráncok és a gyűrődések pontos előrejelzése – numerikus ellapulás nélkül
- A teríték és a vágóél optimalizálása
- Nagy szakítószilárdságú acélok visszarugózása
- (Többlépcsős) kompenzáció
- A teljes sajtolási lánc virtuális prototípusa
- Szépséghibák
- Testreszabás
- Kiváló minőségű eredmények, költségek és idő kompromisszumok nélkül
- Hotformázás, End-to-End Virtuális Prototipuskészítés
- Kapocs a gyártástechnika és a prototípusok összeszerelése között
- Virtuális Valóság
Szépséghibák
Szépséghibák előrejelzése PAM-STAMP segítségével
A szépséghibák jelensége szorosan összefügg a visszarúgózás jelenségével. Ezeknek a kis hibáknak a felfedezése csupán nagyon pontos szimulációk segítségével lehetséges, amelyekre a PAM-STAMP lehetőséget biztosít. A szoftver a problémás terület határvonala érzékelésének új funkcióval is rendelkezik, amely a kőmintával való összehasonlítás vagy az érzékelők elvén érzékeli és osztályozza a problémás részeket. A felhasználó ezeknek a határvonalaknak a segítségével nagyon gyorsan meghatározhatja a problémás helyeket éppúgy, mint a műhelyben, és lemérheti annak mélységét és nagyságát.
Szépséghibák előjelzése
Az AETHRA Automotive Systems a PAM-STAMP segítségével vizsgálja az autókarosszériák méretes elemeit érő kritikus hatásokat
Olvassa el a teljes sikertörténetet
„Az
AETHRA Automotive Systems, az ESI SOUTH AMERICA brazíliai irodájának
segítségével, a PAM-STAMP használatának köszönhetően
kiemelkedően javították a külső panelek alakításánál
keletkező szépséghibák előrejelzését és az elért eredmények
minőségét.
Napjainkban,
ahhoz, hogy kielégíthessük partnereink igényeit, egyszerre több
változtat is tesztelhetünk a fejlesztés stádiumában, ugyanis
bizonyosak vagyunk abban, hogy a szimulációk eredményei
megegyeznek a gyakorlati mérések eredményeivel.”
A. Micheletti Viana, gépészmérnök – alakíthatósági szakember
Wellington Caetano Soares, gépészmérnök – alakíthatósági szakember
Arlem Picinin Campos, szimulációs menedzser
A külső panelokban keletkező típushiba a szimuláció segítségével nagyon gyorsan felismerhető
A mérnökök termelékenységének növelése – Mi áll rendelkezésre és hogyan működik:
- A topológia ellenőrzése, tisztítása és javítása
- Az anyagköltségek meghatározása
- A B-Spline geometriáján alapuló következő generációs szerszámtervezés
- Gyors kapcsolat a szimulációval
- Pontos numerikus módszerek
- Geometriai ráncgátlók
- Visszarúgózás – kinematikai felkeményedés
- Vasalás
- Hármas sebességű üzemmód a lenyűgözően rövid szimulációs idők eléréséhez
- A ráncok és a gyűrődések pontos előrejelzése – numerikus ellapulás nélkül
- A teríték és a vágóél optimalizálása
- Nagy szakítószilárdságú acélok visszarugózása
- (Többlépcsős) kompenzáció
- A teljes sajtolási lánc virtuális prototípusa
- Szépséghibák
- Testreszabás
- Kiváló minőségű eredmények, költségek és idő kompromisszumok nélkül
- Hotformázás, End-to-End Virtuális Prototipuskészítés
- Kapocs a gyártástechnika és a prototípusok összeszerelése között
- Virtuális Valóság
Testreszabás
A PAM-STAMP testre szabható a specializált eszköztárakkal és folyamatmakrókkal. Ez lehetővé teszi a sajtolás folyamatának egyszerűsítését és automatizálását.
Az eszköztár testreszabása az egy- és kettős műveleti folyamatok beállításához
A folyamatmakrók lehetővé teszik a sajtolási műveletek vagy a teljes folyamatok testreszabását oly módon, hogy a felhasználóknak csak a tényleges folyamatadatokat kell kitölteniük a folyamat-szimuláció beállításának befejezéséhez. Következésképpen nincs szükség a véges elemek módszerének vagy a numerikus módszerek ismereteire a folyamat-szimuláció beállításához és futtatásához.
Az eszköztár testreszabása az egy- és kettős műveleti folyamatok beállításához
A testreszabható billentyűparancsok lehetővé teszik az 1-kattintásos adatellenőrzést vagy kiértékelést.
Az eszköztár testreszabása az egy- és kettős műveleti folyamatok beállításához
Külső programokat is hozzáadhat például a megoldó feladatainak vagy a feladatok ütemezésének kezeléséhez.
Az eszköztár testreszabása az egy- és kettős műveleti folyamatok beállításához
Feladatok ütemezése
Lehetőség van arra is, hogy a PAM-STAMP-ot a VISUAL ENVIRONMENT környezetben teljesen testreszabott folyamatok hátterébe helyezzük.
A PAM-STAMP integrálása a légiközlekedési folyamatoknak szentelt folyamatkörnyezetbe
A mérnökök termelékenységének növelése – Mi áll rendelkezésre és hogyan működik:
- A topológia ellenőrzése, tisztítása és javítása
- Az anyagköltségek meghatározása
- A B-Spline geometriáján alapuló következő generációs szerszámtervezés
- Gyors kapcsolat a szimulációval
- Pontos numerikus módszerek
- Geometriai ráncgátlók
- Visszarúgózás – kinematikai felkeményedés
- Vasalás
- Hármas sebességű üzemmód a lenyűgözően rövid szimulációs idők eléréséhez
- A ráncok és a gyűrődések pontos előrejelzése – numerikus ellapulás nélkül
- A teríték és a vágóél optimalizálása
- Nagy szakítószilárdságú acélok visszarugózása
- (Többlépcsős) kompenzáció
- A teljes sajtolási lánc virtuális prototípusa
- Szépséghibák
- Testreszabás
- Kiváló minőségű eredmények, költségek és idő kompromisszumok nélkül
- Hotformázás, End-to-End Virtuális Prototipuskészítés
- Kapocs a gyártástechnika és a prototípusok összeszerelése között
- Virtuális Valóság
Kiváló minőségű eredmények, költségek és idő kompromisszumok nélkül
Kiváló minőségű eredmények, költségek és idő kompromisszumok nélkül
Az
összes új fejlesztés eredményeként a szimulációs idő és az
eredményminőség közötti kompromisszumok elhagyhatók, miközben
lehetséges a realisztikus virtuális prototípuskészítés.
A Mitsubishi Outlander oldalsó karosszériaeleme
Az ESI szerszámfelület megtervezéséhez kínált, a B-Spline geometrián alapuló eszközei kiváló minőségű aktív szerszámfelületeket hoznak létre, amelyek pontos leírást adnak az érintkező felületekről. Az adatok automatikus továbbítása a PAM-STAMP-be, és a mélyhúzás-szimuláció beállítása minimálisra csökkenti a munkaidőt. Az alkatrészek geometriájának, a szerszám felületének, a ráncgátlóknak, a fékező hornyoknak és a folyamathoz kapcsolódó egyéb paramétereknek a módosítása rövid időt vesz igénybe. Manapság a PAM-STAMP megoldó mindig pontos érintkezéssel működik a mélyhúzás során, nincs kompromisszum a numerikus beállításokban, és ha szükséges, geometriai fékezőhornyokkal és bármilyen fejlett, határfelülettel és felkeményedéssel rendelkező anyagmodellel. Az új hármassebességű mód négy vagy nyolc párhuzamos processzor maggal összekapcsolva nagyon alacsony válaszidővel biztosítja a szimulációs eredményeket, még olcsó számítógépeknél is. A szimulációs idők hihetetlenül rövidek a nyolc processzormaggal, SSD-merevlemezzel és újabb processzorokkal rendelkező számítógépeknél. A nyolcmagos konfiguráció és a hármassebességű üzemmód esetén a sebesség akár hússzoros is lehet, szemben az egymagos konfigurációval, hármassebességű opció nélkül. Ez lehetővé teszi a folyamatosan magas színvonalú eredményeket a korai megvalósíthatóságtól a csúcsminőségű alakíthatóságig, következésképpen minimalizálva az általános tervezési költségeket.
A mérnökök termelékenységének növelése – Mi áll rendelkezésre és hogyan működik:
- A topológia ellenőrzése, tisztítása és javítása
- Az anyagköltségek meghatározása
- A B-Spline geometriáján alapuló következő generációs szerszámtervezés
- Gyors kapcsolat a szimulációval
- Pontos numerikus módszerek
- Geometriai ráncgátlók
- Visszarúgózás – kinematikai felkeményedés
- Vasalás
- Hármas sebességű üzemmód a lenyűgözően rövid szimulációs idők eléréséhez
- A ráncok és a gyűrődések pontos előrejelzése – numerikus ellapulás nélkül
- A teríték és a vágóél optimalizálása
- Nagy szakítószilárdságú acélok visszarugózása
- (Többlépcsős) kompenzáció
- A teljes sajtolási lánc virtuális prototípusa
- Szépséghibák
- Testreszabás
- Kiváló minőségű eredmények, költségek és idő kompromisszumok nélkül
- Hotformázás, End-to-End Virtuális Prototipuskészítés
- Kapocs a gyártástechnika és a prototípusok összeszerelése között
- Virtuális Valóság
Hotformázás, End-to-End Virtuális Prototipuskészítés
Hotformázás – az ügyféligényektől a virtuális valóságig
A hotformázás gyorsan növekszik, ez egy lenyűgöző gyártási technika, ahol a meleg teríték jó formázhatóságát a szerszámban véghezvitt edzés miatt a végtermék kivételes szilárdságával kombinálják. Nincs olyan tradicionális alakítható anyag, amely közel állna a melegen formált acél szilárdságához. Ez természetes választássá teszi az autó ütközéses alkatrészei esetében. Manapság az összes nagyobb OEM gyártó dolgozik a gépjárművek hotformázással alakított alkatrészeivel az ütközési energia elnyelése érdekében. Ennek köszönhetően a kiemelkedő ütközőképességgel rendelkező kis autók gyártása is lehetséges – ugyanis lehetséges a hagyományosan gyengébb A osztályú autók számára az 5 csillag megszerzése az EURO-NCAP ütközési tesztekben (pl. FIAT 500).
Ez azt jelenti, hogy a sajtolás során nincs értelme csak az alkatrész alakíthatóságára figyelni. Az egész láncot szem előtt kell tartani – a tervezés kezdeti szakaszától kezdve. A végső alkatrész megfelelő működésének eléréséhez elengedhetetlen a szükséges ütésállóság elérése. Ez azt jelenti, hogy a biztonsági mérnöknek a sajtolási osztályra kell támaszkodnia a megfelelő tulajdonságokkal rendelkező alkatrészek előállításakor.
Maga a hotformázás olyan gyártási technika, ahol a különböző mezők együtt játszanak, hogy működésbe lépjenek vagy sem. A sajtoló osztálynak most kell kiépíteni a tudásbázist a kohászat-, a hőátadás-, a hűtés- és a folyadékok dinamikájának területén is – olyan területeken, amelyek esetében általában több szakember van bekapcsolva.
Összegezve: ezzel az új eljárással a sajtoló szakember hirtelen számos új területtel szembesül, amelyekben magas szintű ismeretekkel kell rendelkeznie, hogy ezt a folyamatot korrigálhassa.
Még a legtehetségesebb mérnökökkel szemben is túl nagy elvárás lenne, hogy mindezen területeken szakértővé válljanak. Ez egy tipikus terület, ahol a virtuális gyártás fontos szerepet játszhat az új folyamatok indításában. Az alkatrészgyártás minden különféle aspektusával virtuálisan tesztelhető, mielőtt a drága melegformázási folyamat megkezdődne. A részleges teljesítmény a végső ütközés során szintén virtuálisan tesztelhető. Ez ismét egy lépés az end-to-end virtuális gyártás felé – még akkor is, ha a különféle szempontok szimulálása továbbra is kihívásnak számít.
Manapság a teljes értéklánc elérhető, lehetővé téve a teljes sajtolási folyamat elemzését a kezdeti alkatrészköltségektől az edzés utáni deformációkig, a hűtési csatorna elemzésén át a virtuális valóságban való ellenőrzésig.
Anyagköltségek meghatározása
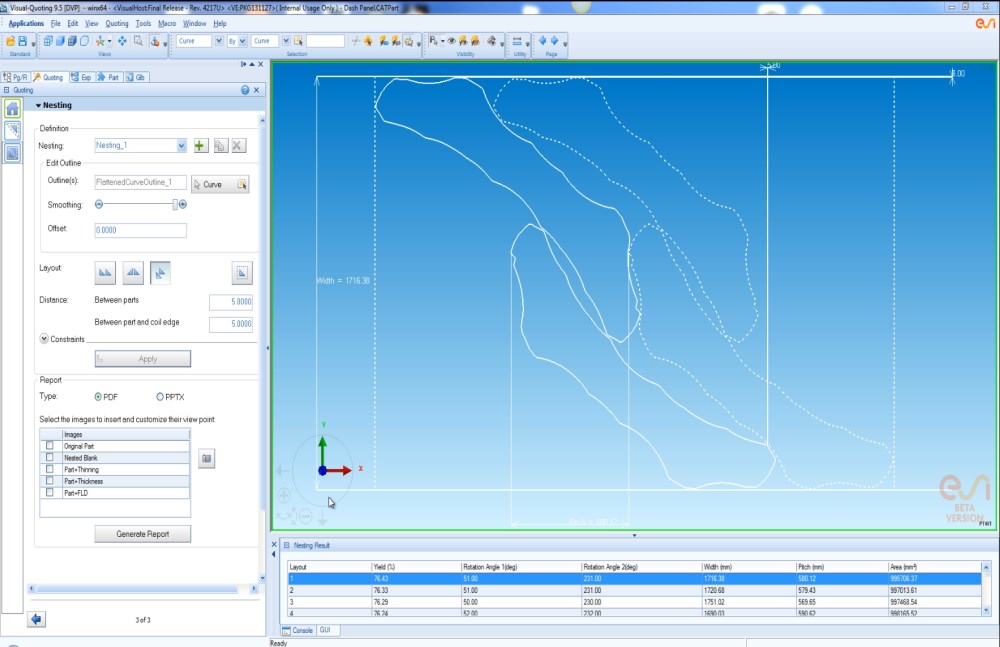
Műszerfal terítéke és annak elhelyezése a pléhlemezre – Az AP&T hozzájárulásával
A topológia ellenőrzése, tisztítása és javítása
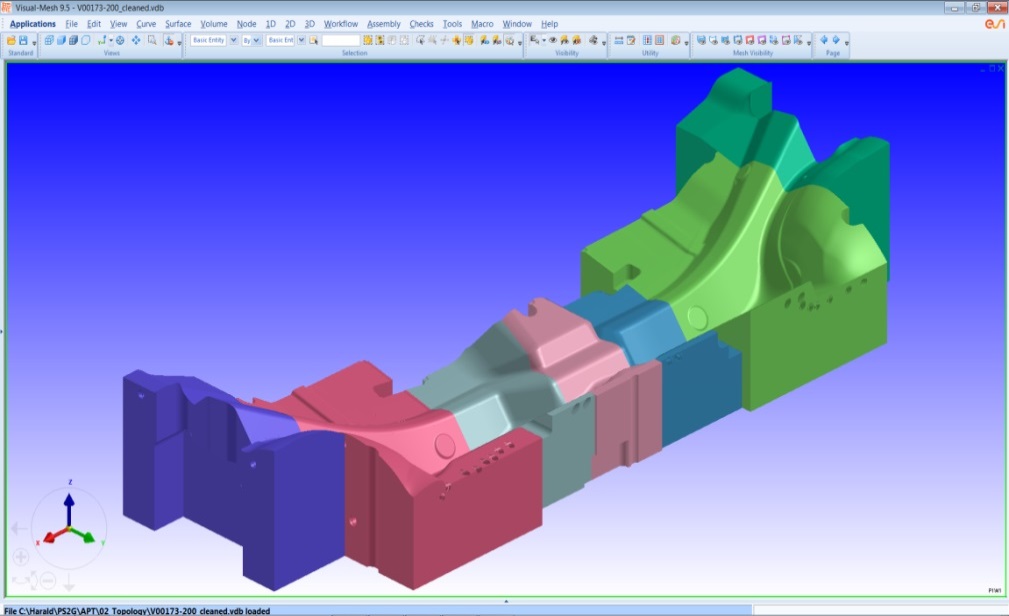
Műszerfal szerszám alsó része – Az AP&T hozzájárulásával
Szerszám aktív felületeinek tervezése
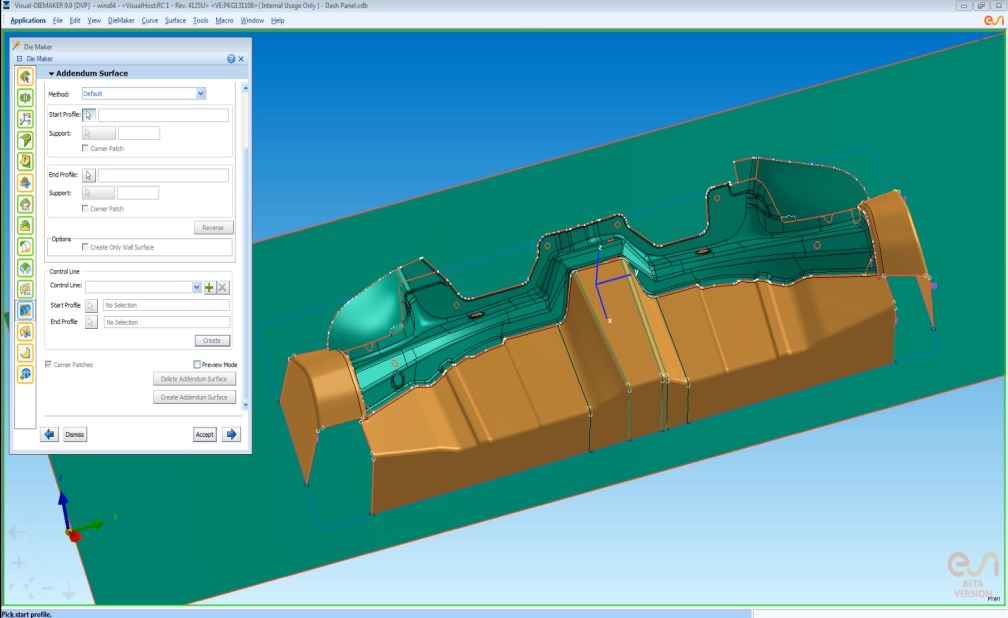
Műszerfal
szerszám aktív felületeinek tervezése –
Az
AP&T hozzájárulásával
Az alakíthatóság megvalósíthatósági szimulációja
Mozgatás – sajtolás
A repedések és ráncok eliminációja
A szerszám aktív felületeinek iterációja a tervezés során mindaddig, amíg az nem megfelelő
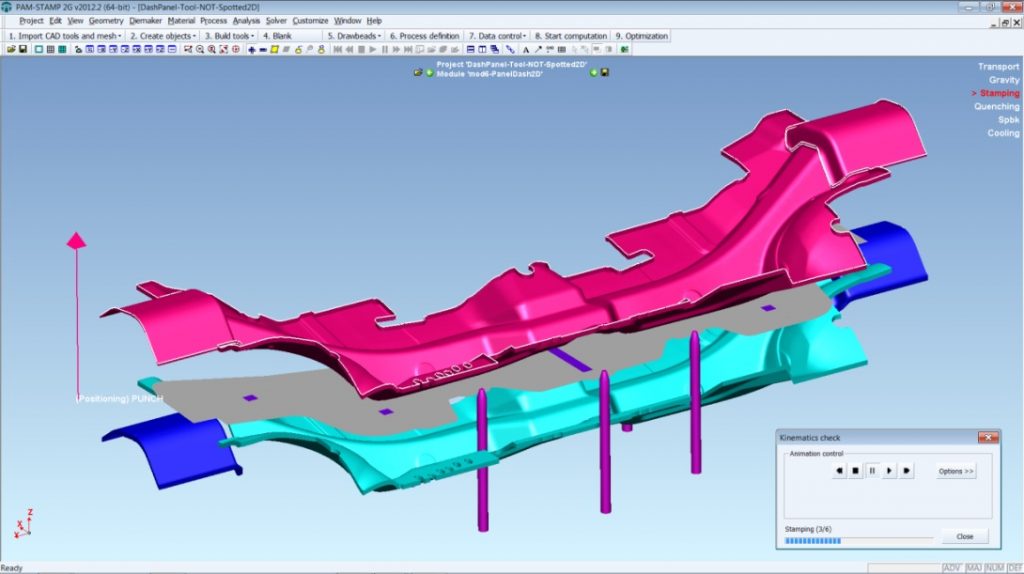
Műszerfal hotformázási folyamata 6 lépésben – Az AP&T hozzájárulásával
Bővített alakítási szimuláció
Mozgatás – sajtolás – edzés
A szerszám aktív felületének pozicionálása
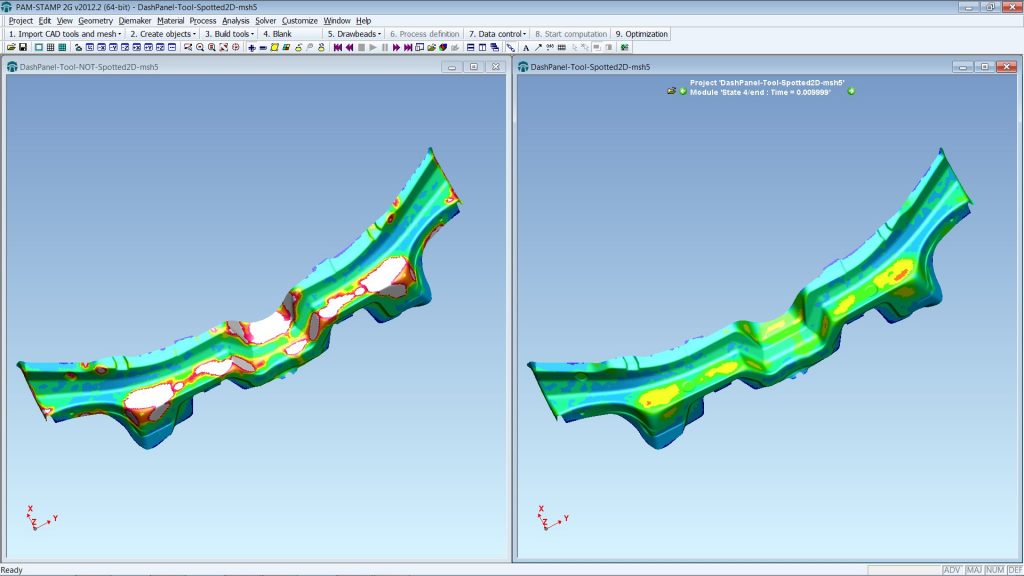
A hőmérséklet az edzés végén meghaladja a megengedett értéket a nem pozicionált szerszámban (bal oldalt), miközben az összes hőmérsékleti szint a megengedett maximális érték alatt a pozicionált szerszám (jobb oldalt) esetében – Az AP&T hozzájárulásával
Bővített alakítási szimuláció
Mozgatás – sajtolás – edzés – visszarúgózás – levegőn történő hűtés
Pozicionált szerszám homlokfelület – valós hőátadás a szerszámban éppúgy, mint a valós gyártás során
Az alkatrész hőmérsékletének és fázisarányának pontos meghatározása, a szerszámból való kivétel után
Az alkatrész deformációja – Az alkatrész névleges alakjától való eltérése erősen függ az edzés utáni maximális hőmérséklettől
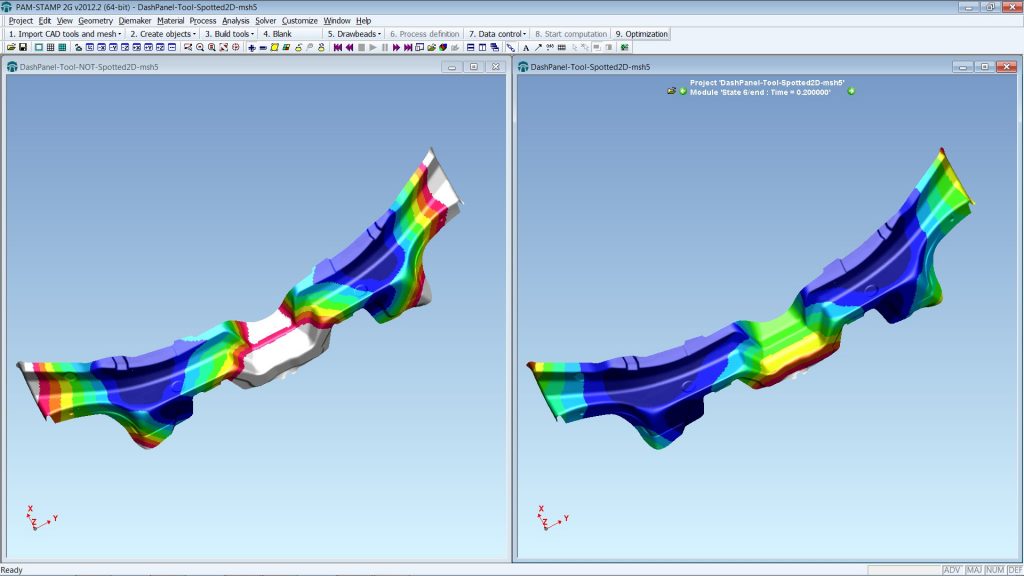
Léghűtés okozta deformáció az edzés után a nem pozicionált szerszám esetében (balra) és pozicionált szerszámban (jobbra) – Az AP&T hozzájárulásával
Részlegesen beedzett és több darabból álló teríték
Részben beedzett és több darabból álló terítékek kezelése is lehetséges. Így néz ki a tipikus hűtési sebesség a részlegesen edzett alkatrészen, a dilatométer teszt eredményében. Az x tengelyen a hőmérséklet van ábrázolva, az y tengelyen pedig a kiindulóponthoz viszonyított valós térfogat, mely függvénye a hőmérsékletnek és a fázisátalakulásoknak.
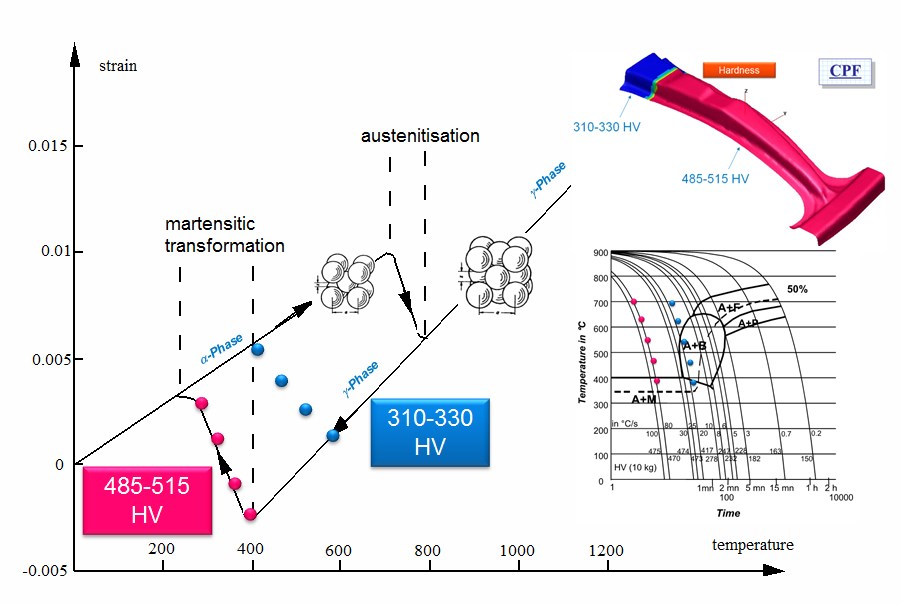
A részlegesen edzett alkatrészek tipikus hűtési sebessége a dilatométer diagramján
Ez a levegőhűtés okozta deformáció. Azután alakul ki, hogy az alkatrészt kiveszik a szerszámból, a bimetálokhoz hasonló hatás miatt.
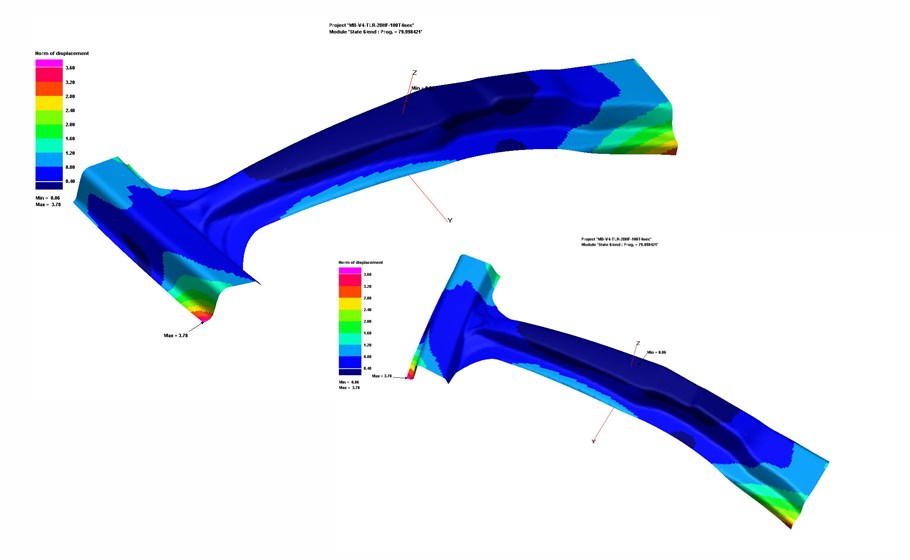
A szabad levegőn való hűtés okozta deformáció a részlegesen beedzett részeken
Mindezeket a modellezési technikákat kombinálhatjuk a több darabból álló teríték esetében is.
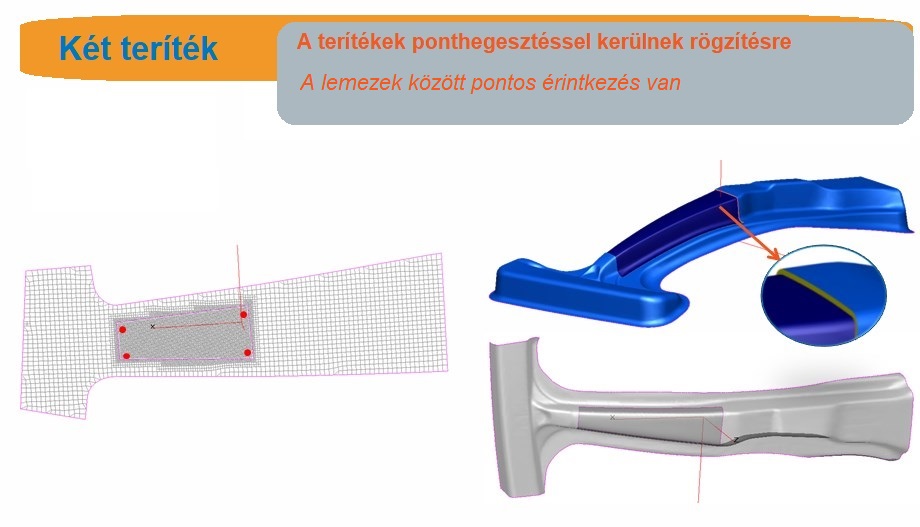
Több darabból álló teríték modelljének beállítása
Hotformázás – a szerszám hűtési képessége
A hűtőcsatorna elemzését hőátadási modell alkalmazásával végezzük – figyelembe véve a teríték alakítási szimulációból származó tényleges hőmérsékleteit. A hőátadási térképek CFD elemzésen alapulnak, lásd a következő fejezetet. Van egy speciális eszköz a CAD modell felépítéséhez és egy összetett 3D szerszám rövid időn belüli hálózásának elkészítéséhez.
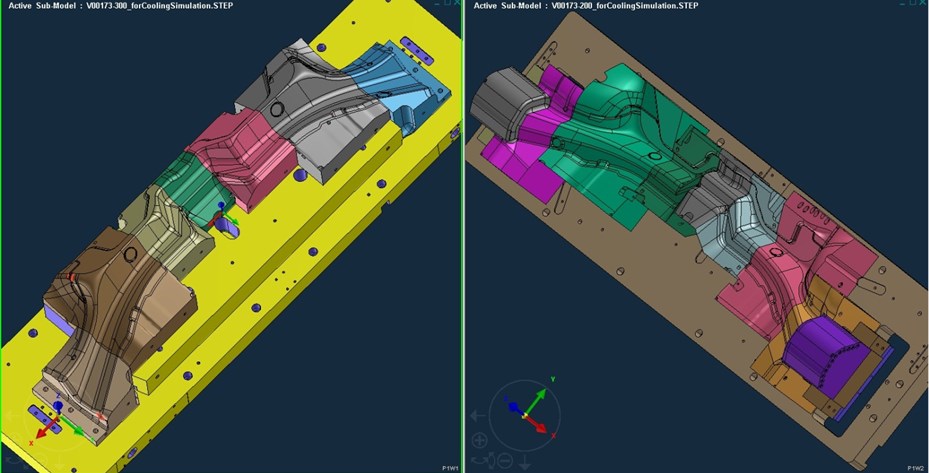
A szerszám egy része CAD környezetben – az AP&T hozzájárulásával
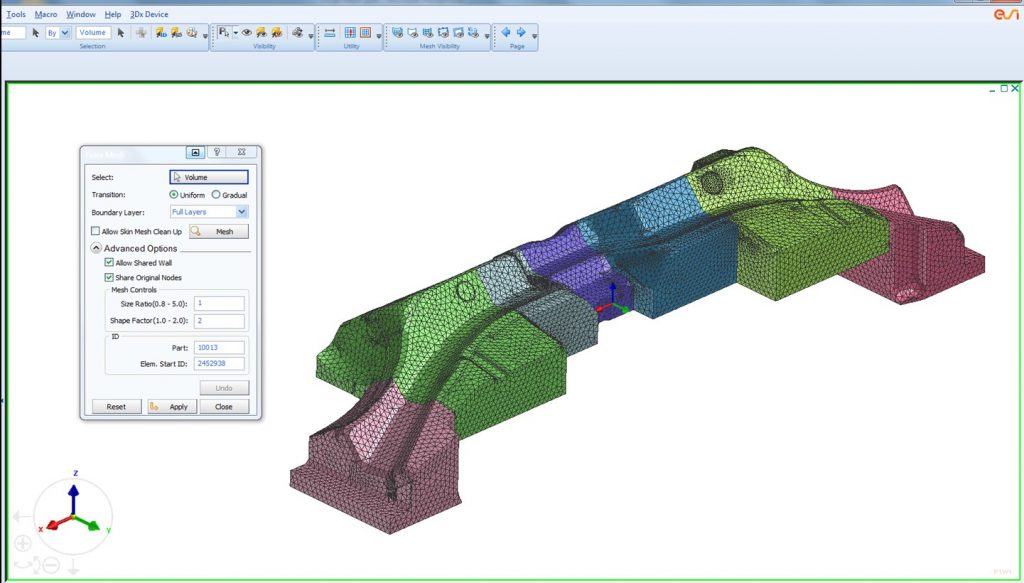
A szerszám hőátadási elemzéshez igazított térhálója – Az AP&T hozzájárulásával
A hűtőcsatornák hőátadási együtthatója ebben a szakaszban állandónak van becsülve.
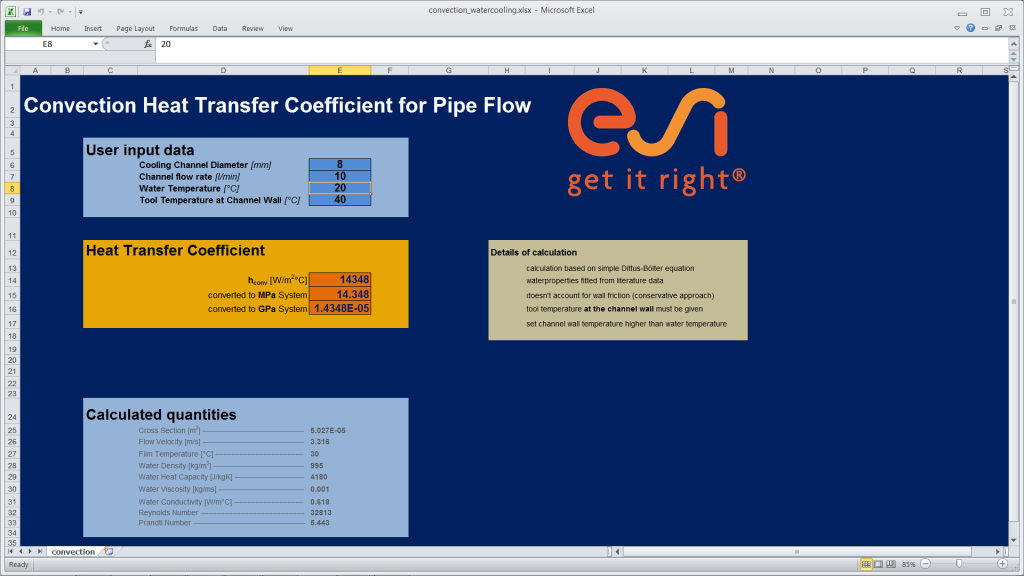
A hőátadási együttható becslése a hűtőcsatornákban
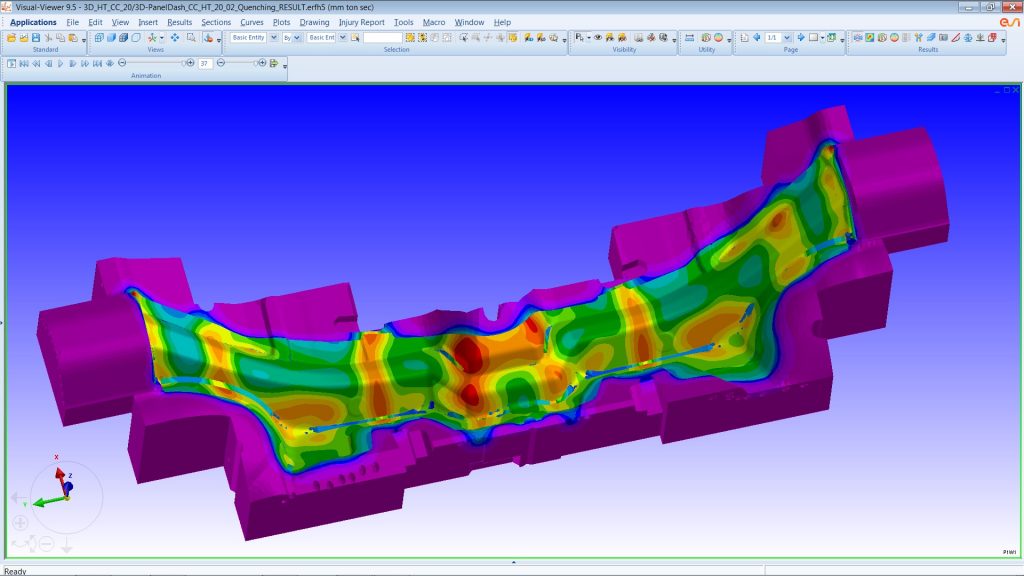
A teríték és a szerszám hőmérséklete néhány sajtolási ciklus után – Az AP&T hozzájárulásával
Hűtőcsatornák tervezése – CFD
Az ötvözött lemezből készült teríték hotforming technológiával végzett sajtolásának hőanalízise és a valós kísérletek is azt sugallják, hogy az ausztenit fázisának martenzitté történő átalakítása a lemez melegítési és hűtési hőmérsékletének szabályozásával a hőformázás alapja. Amennyiben a hűtési sebesség eléri vagy meghaladja a kritikus hűtési sebességet, az ausztenit közvetlenül átalakítható martenzitté. A lemez kritikus hűtési sebessége függ a kritikus vízáramlás elemeitől, a szerszámhűtő rendszer felépítésétől, a hűtőközegtől, a szerszámon átfolyó folyadék mennyiségétől stb. Amennyiben adottak a szerszám felépítésének elemei, a hűtőrendszer, a hűtőközeg stb. meg vannak határozva, a kritikus hűtési sebesség állandó. Ennek eredményeként a kritikus vízáram szabályozásával garantálható egy átmeneti forró alakítási folyamat, valamint a forró alakítási követelmények, miközben a hotformázás során meggátoljuk a túlzott visszaverődést, a repedezést, a megnövekedett formáló erőt, a szerszám könnyű kopását stb.
Az ACE + CFD megoldót a hűtőfolyadék áramlási sebességének kiszámításához használja a felső és az alsó szerszám hűtőcsöveiben. A 21. ábra a felső sajtolószerszám hűtőcsövében a nyomáseloszlást mutatja 2, 5 és 8 bar nyomáson. A CFD elemzés meghatározza a hőátadási együtthatót a hűtőcsövekben. Az ACE + által kiszámított hőátadási tényezőket a PAM -STAMP-be beolvasva a szerszám felülete hőmérsékletének kiszámításához használják.
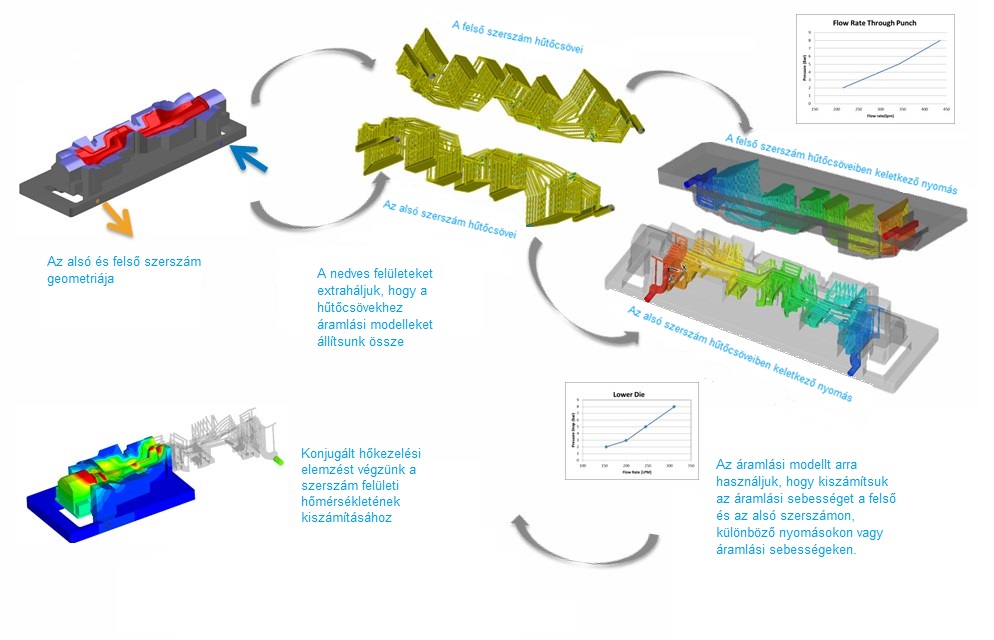
A hőátadási térképek elkészítése
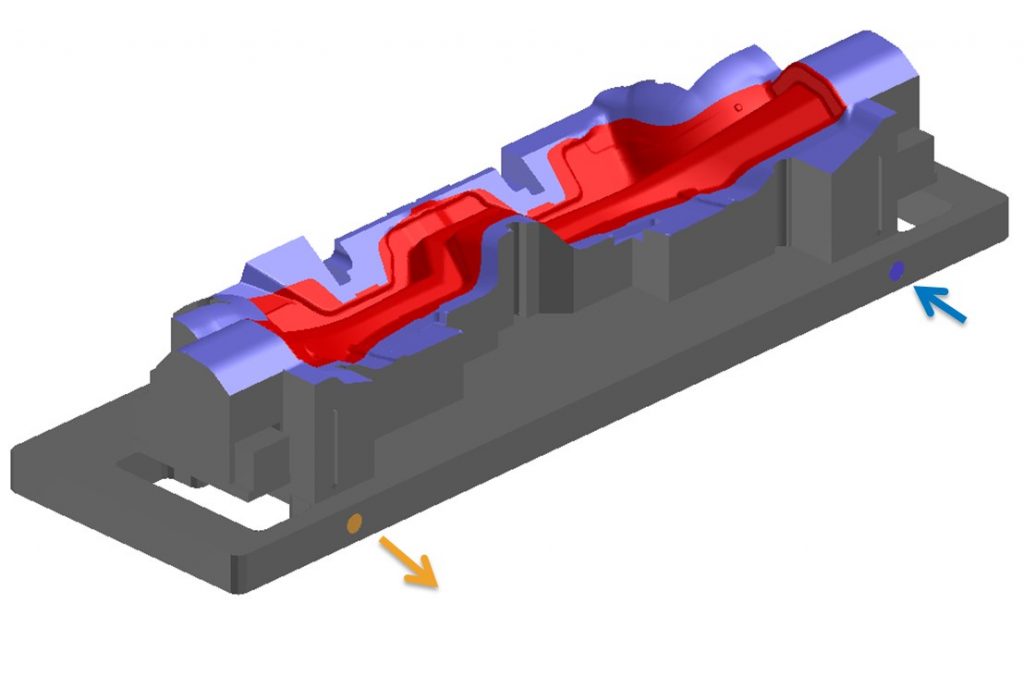
Bemeneti és kimeneti nyílások
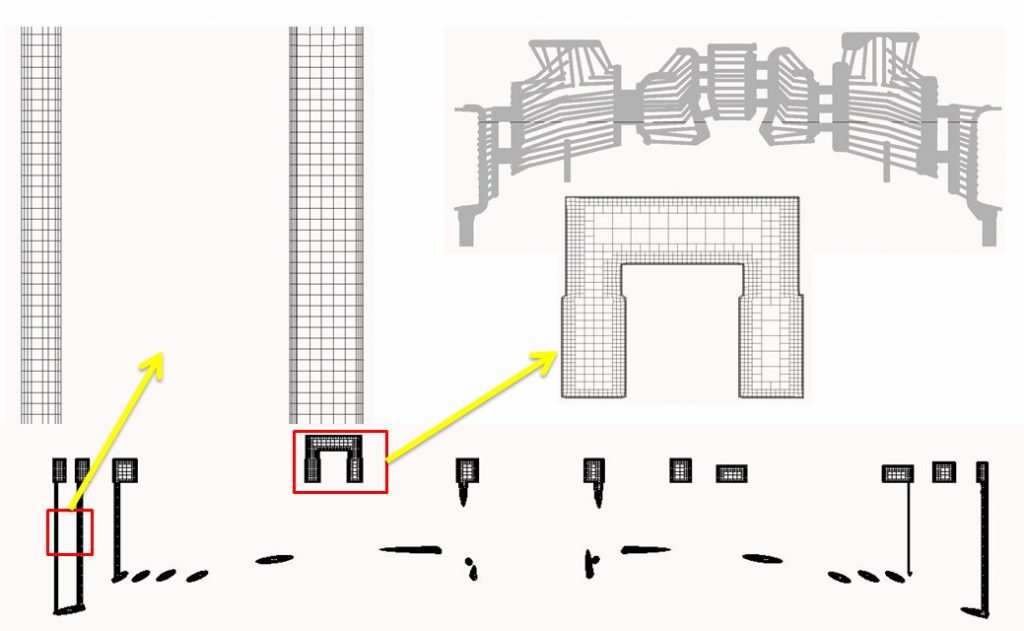
CFD háló VisCard környezetben
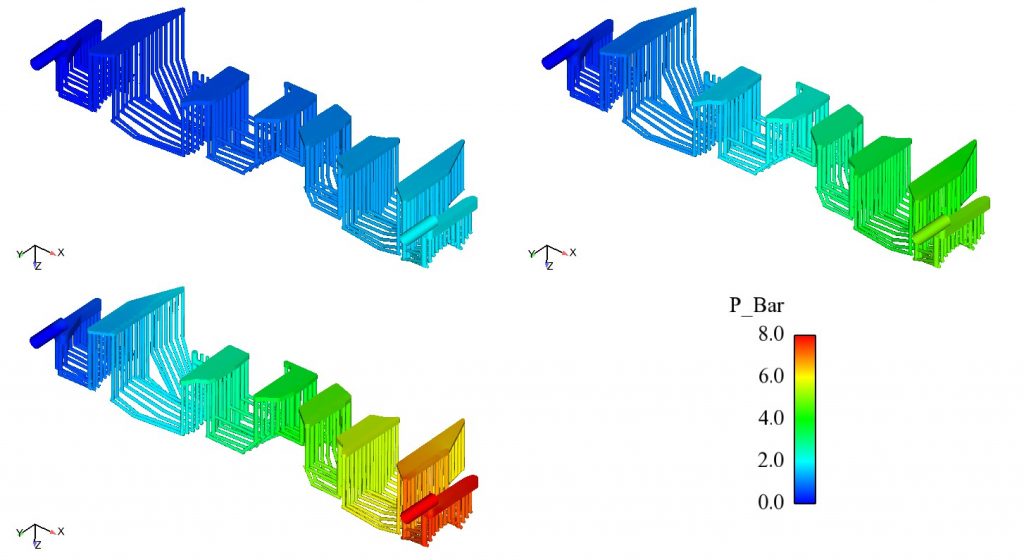
Nyomáscsökkenés a bemenetről a kimenetre – Az AP&T hozzájárulásával
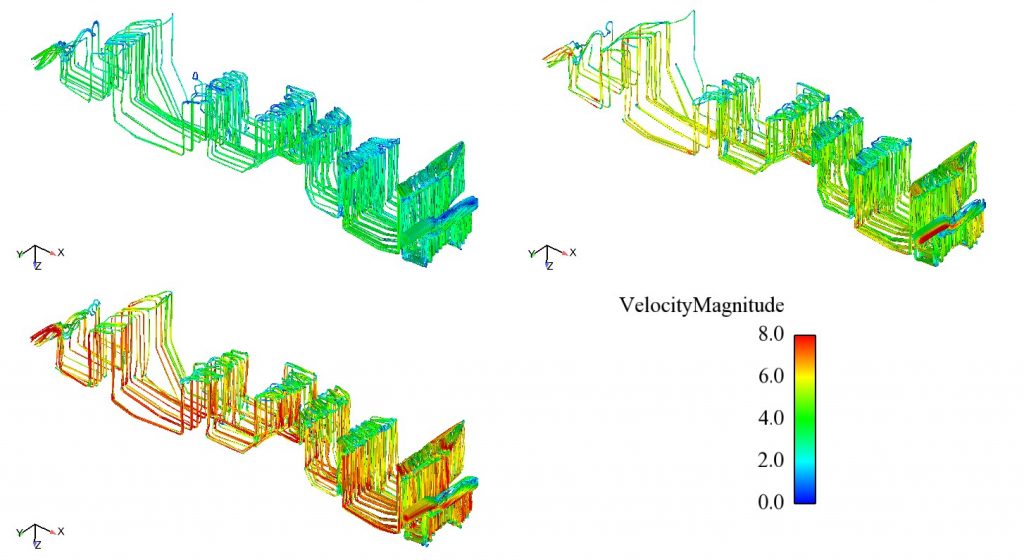
Sebességi térképek a bemenettől a kimenetig – a zárványok azonosítása stb. – Az AP&T hozzájárulásával
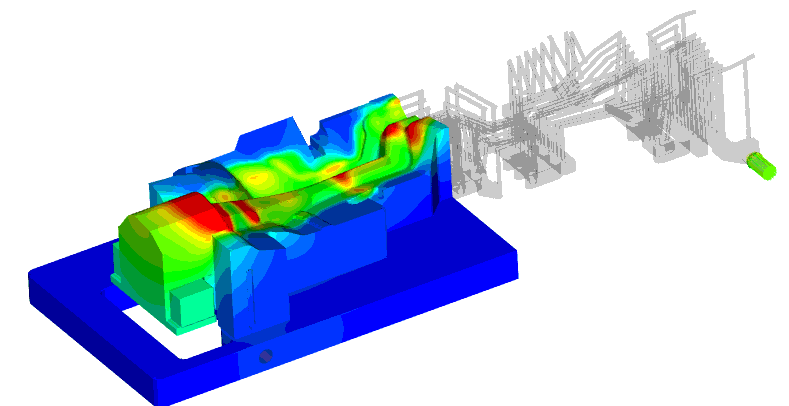
A szerszám felülete és hőmérséklete, sebessége, a nyomás és a teljes hőátadás egy modellben
Virtuális valóság
A virtuális valóság a hotformázási gyártósor teljes tervének áttekintésére szolgál. Még arra is lehetőség van, hogy integráljuk a síklemezalakító szimulációk eredményeit is.
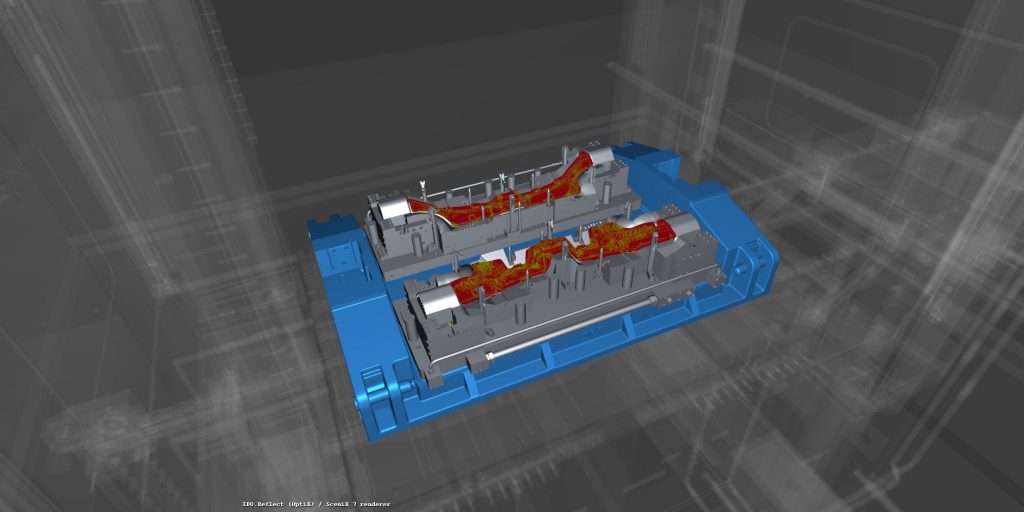
Virtuális valóság – a forró alkatrész a szerszámban – Az AP&T hozzájárulásával
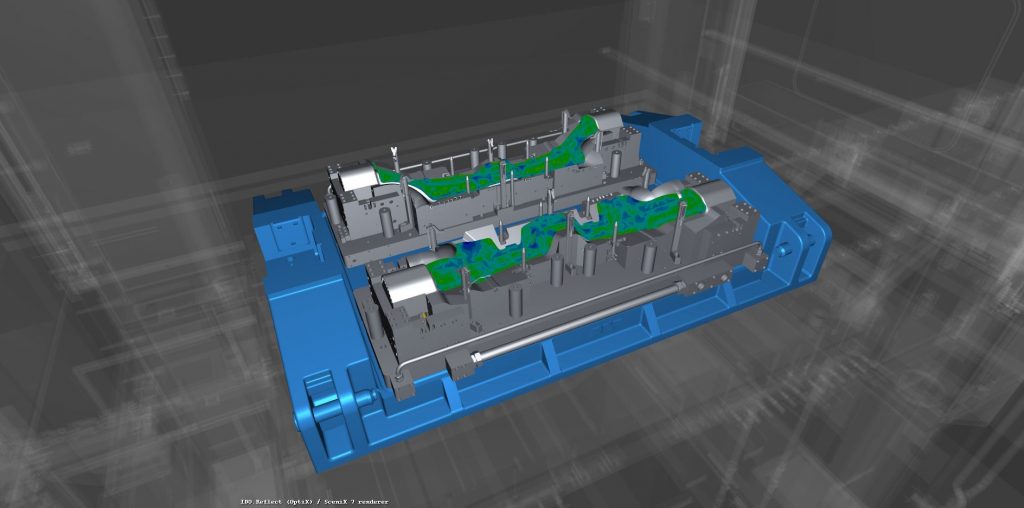
Virtuális valóság – az alkatrész edzés után – Az AP&T hozzájárulásával
A mérnökök termelékenységének növelése – Mi áll rendelkezésre és hogyan működik:
- A topológia ellenőrzése, tisztítása és javítása
- Az anyagköltségek meghatározása
- A B-Spline geometriáján alapuló következő generációs szerszámtervezés
- Gyors kapcsolat a szimulációval
- Pontos numerikus módszerek
- Geometriai ráncgátlók
- Visszarúgózás – kinematikai felkeményedés
- Vasalás
- Hármas sebességű üzemmód a lenyűgözően rövid szimulációs idők eléréséhez
- A ráncok és a gyűrődések pontos előrejelzése – numerikus ellapulás nélkül
- A teríték és a vágóél optimalizálása
- Nagy szakítószilárdságú acélok visszarugózása
- (Többlépcsős) kompenzáció
- A teljes sajtolási lánc virtuális prototípusa
- Szépséghibák
- Testreszabás
- Kiváló minőségű eredmények, költségek és idő kompromisszumok nélkül
- Hotformázás, End-to-End Virtuális Prototipuskészítés
- Kapocs a gyártástechnika és a prototípusok összeszerelése között
- Virtuális Valóság
Kapocs a gyártástechnika és a prototípusok összeszerelése között
Az előző szakaszban foglalkoztunk az alkatrészek gyártásával, beleértve az anyagok fizikáját. Az autóipari gyártási folyamat során az alkatrészeket ezután összeszerelik a karosszériaüzemben. Ebben a folyamatban az alak, az anyagtulajdonságok és a merevség ismét módosításra kerül. A termék- és a folyamattervezők számára csak akkor hasznosak ezek az információk, ha a megfelelő időben állnak rendelkezésre. Ezen információk megfelelő időben történő megadása a Virtuális Karosszériaüzem célja. Műszaki szempontból az összeszerelési folyamat okozta deformációt és a kapcsolódó szerelési problémákat, például a tényleges feszültség-nyúlás helyzetét a térben, a merevségi jellemzőket, a maradandó feszültséget és a felkeményedés mértékét a termék- és a folyamattervezőknek a megfelelő időben kell átadni.
A kezdeti behatolási területek
A kiszámított deformáció a készülékből történő kivétel után
Szerelést (ponthegesztést) követő maradandó feszültségek: az alakíthatósági folyamat időlefolyásának ismerete nélkül
Szerelést (ponthegesztést) követő maradandó feszültségek: az alakíthatósági folyamat időlefolyásának ismeretével
A virtuális összeszerelési folyamatot az alábbiakban ismertetjük, és néhány mérföldkővel szemléltetjük.
A strukturális elemeket acéllemezből állítják elő préseléssel,
Az alkatrészek a készülékekben kerülnek elhelyezésre,
Az érintkezési interferenciák az egyes préselt geometriák között észlelésre kerülnek,
A szorítószerszámok zárva vannak,
A kontaktok és a deformációk aktualizálásra kerülnek,
A vezető csapok effektusai figyelembe vannak véve,
Az egyes alkatrészek ponthegesztéssel vannak összefogva,
A hézagok záródása és a hő okozta zsugorodás is figyelembe van véve,
A kontaktok és a deformációk aktualizálásra kerülnek,
Az összeállítási egység elengedésre kerül, és kiszámítják a végső deformációkat / maradandó feszültségeket / a valós pontot a nyúlás-feszültség térben, amelyek utána bármilyen virtuális analízis vizsgálatnak alávethetők.
A termék- és folyamattervezők előnyei a következők:
Pozicionálási problémák felismerése,
a vezető csapok, készülékek, bilincsek, hegesztések, alkatrészek közötti rések hatásainak tanulmányozása,
Az összeszerelési problémák felismerése és ellenintézkedések alkalmazása
Prototípus-költségek megtakarítása, a költségigényes munkák csak szükség esetén kerülnek elvégzésre
A virtuális teljesítmény kiértékelésének javítása a tartósság és az ütközési viselkedések területén
Koncepció validációja
Az értékelt prototípus – a Chrysler hozzájárulásával
Kiváló korreláció a számított és a mért eredmények között – a Chrysler hozzájárulásával
A mérnökök termelékenységének növelése – Mi áll rendelkezésre és hogyan működik:
- A topológia ellenőrzése, tisztítása és javítása
- Az anyagköltségek meghatározása
- A B-Spline geometriáján alapuló következő generációs szerszámtervezés
- Gyors kapcsolat a szimulációval
- Pontos numerikus módszerek
- Geometriai ráncgátlók
- Visszarúgózás – kinematikai felkeményedés
- Vasalás
- Hármas sebességű üzemmód a lenyűgözően rövid szimulációs idők eléréséhez
- A ráncok és a gyűrődések pontos előrejelzése – numerikus ellapulás nélkül
- A teríték és a vágóél optimalizálása
- Nagy szakítószilárdságú acélok visszarugózása
- (Többlépcsős) kompenzáció
- A teljes sajtolási lánc virtuális prototípusa
- Szépséghibák
- Testreszabás
- Kiváló minőségű eredmények, költségek és idő kompromisszumok nélkül
- Hotformázás, End-to-End Virtuális Prototipuskészítés
- Kapocs a gyártástechnika és a prototípusok összeszerelése között
- Virtuális Valóság
Virtuális Valóság
Az egyidejű tervezésnél a munkafolyamat továbbra is létezik, de az iterációkat figyelembe veszik. A fő különbség a terméktervezés szokásos megközelítésétől az, hogy minden tudományág részt vesz a terméktervezés legkorábbi szakaszaiban; egyidejűleg haladnak úgy, hogy az iterációk kevesebb felesleges erőfeszítést és időveszteséget eredményeznek. Ennek a megközelítésnek a kulcsa a tudományágak közötti és az azokon belüli kommunikáció elismert fontossága. A termék gyártásának és teljesítményének megtervezésében alkalmazott erőteljes és hatékony eszköz a számítógépes szimuláció. A gyártási folyamat következő lépése egy prototípus, azaz a termék eredeti működőképes modelljének elkészítése és tesztelése.
Most ezt a következő lépést hajtjuk végre a virtuális termékgyártás tervezésének folyamatában, az anyag fizikájának szimulálásával az egyes gyártási lépéseknél, ezt a komplex technológiát elérhetővé téve a technikusok és a tervezők számára a folyamat automatizálásával. Az ESI, GROUP virtuális valósága a virtuális prototípus-készítés folyamatát egy magasabb szintre emeli.
Virtuális valóság – az alkatrész edzés után – Az AP&T hozzájárulásával
A mérnökök termelékenységének növelése – Mi áll rendelkezésre és hogyan működik:
- A topológia ellenőrzése, tisztítása és javítása
- Az anyagköltségek meghatározása
- A B-Spline geometriáján alapuló következő generációs szerszámtervezés
- Gyors kapcsolat a szimulációval
- Pontos numerikus módszerek
- Geometriai ráncgátlók
- Visszarúgózás – kinematikai felkeményedés
- Vasalás
- Hármas sebességű üzemmód a lenyűgözően rövid szimulációs idők eléréséhez
- A ráncok és a gyűrődések pontos előrejelzése – numerikus ellapulás nélkül
- A teríték és a vágóél optimalizálása
- Nagy szakítószilárdságú acélok visszarugózása
- (Többlépcsős) kompenzáció
- A teljes sajtolási lánc virtuális prototípusa
- Szépséghibák
- Testreszabás
- Kiváló minőségű eredmények, költségek és idő kompromisszumok nélkül
- Hotformázás, End-to-End Virtuális Prototipuskészítés
- Kapocs a gyártástechnika és a prototípusok összeszerelése között
- Virtuális Valóság
Die Face Design and feasibility/formability simulation fully integrated into CATIA V5
Az ESI Group fém alakítási CATIA V5 PLM környezetre épülő termékportfóliója segíti éppúgy a sajtolással előállított termékek szerkesztését, mint a szerszámkészítők munkáját, éspedig a beépített jelentős mérnöki eszközökkel, amelyek támogatják a gyors generatív modellkészítést a PLM környezetben a tervezés és a gyártás fázisában egyaránt:
A PAM-TFA (Transparent Formability Analysis) a CATIA V5 környezetbe integrált gyors alakíthatósági analízist biztosító modul. Ez egy erős teljesítményű „inverz“ oldó, mely segít előre meghatározni az alkatrész alakíthatóságát és annak árkalkulációját.
A PAM-DIEMAKER for CATIA V5 egy speciális eszköz CATIA V5 környezetben (beleértve a szimulációhoz való zökkenőmentes kapcsolódást); az aktív szerszámfelületek tervezését teszi lehetővé. Vezeti a felhasználót a szerszámfelület-tervezési folyamat során (nyitás, leszorítók tervezése, szerszámtest-, vágóél fejlesztés.), hatékony és üzlet-orientált funkciókkal, az előzetes megvalósíthatósági tanulmányoktól a teljes végső validálásig.
Kulcstulajdonságok:
A B-spline geometrián alapuló szupergyors szerszámtest tervezés
A szerszámtervező szoftver két működési módot kínál: termék- (megvalósíthatóság) vagy szerszámfejlesztés
CATIA környezetben és CATIA adatbázisokkal dolgozhat
Használhatja a PAM-DIEMAKER vagy a natív CATIA funkciókat
Már nem kell többé várakozni, amikor módosítania kell az alkatrész geometriáját
Az alkatrészek gyors és robusztus cseréje
Közvetlen kapcsolat a PAM-STAMP-lel és nagymértékben automatizált adatátvitel
A piacon a leggyorsabb megoldó a megvalósíthatóság és az alakíthatóság esetében is (próbálja ki!)
A legjobb szimulációs minőség a piacon
Ügyfeleink sikerei
„A SEAT fejlesztési prototípus központja (CPD) számára a Catia V5 környezetbe integrált eszközök, mint például a PAM-DIEMAKER for CATIA V5 lehetőséget biztosítanak a szerszám gyors és pontos kifejlesztésére. Nagyon értékes, hogy lehetőségünk van a szükséges geometria módosítások elvégzésére, miközben ezek az evolúciós adatok állandóan rendelkezésünkre állnak a CATIA környezetben végrehajtott megmunkáláshoz.
Ez óriási előnyt jelent úgy a produktivitás szempontjából, mint a konstrukciónk végső minősége szempontjából, és a folyamat minden fázisában változatlan környezetben teremt lehetőséget a munkánk végzésére.“
Javier
Diaz Martinez,A
fejlesztési prototípus központ (CPD) igazgatója, SEAT S.A.
A PAM-DIEMAKER for CATIA V5 szimulációs csomag lehetővé tette, hogy munkánk minden egyes lépését ugyan abba a környezetben végezzük a fejlesztési folyamat teljes egészében. Ez számunkra azt jelentette, hogy gyorsabban vagyunk képesek elvégezni a várható költséganalízist, miközben pontos szimulációval határozzuk meg a teríték szükséges nagyságát és alakíthatóságát. Végül konkurenciaképesebbek vagyunk, ugyanis ajánlatunk partnerünknél való bemutatásánál erős érvekkel rendelkezünk és garantálni tudjuk a minőséget.“
Vladimir B.
Ferreira Jr.Tech
Center, Tower Automotive, Brazília
Találjon meg bennünket a Dassault Systèmes PLM MarketPlacealkalmazásán
PAM-STAMP – nagyon rugalmas termék
A PAM-STAMP lehetővé teszi szinte bármilyen szerszám művelet szimulálását, amely szóba jöhet: a teríték előkészítése, levágása, kilyukasztása, lyuggatása és kivágása, körbevágása, ékekkel végrehajtott műveletek, hajlítás, alakítás, mélyhúzás, dombornyomás, lyukasztás-kivágás, többlépcsős műveletek és szintén összeszerelési műveletek, mint pl. a házasság.
Az alábbiakban felsoroljuk a legfontosabb alkalmazásokat, amelyeket a szoftver kínál. A szokásos grafikus felhasználói felület segítségével beállíthatja őket és szimulálhat velük. Továbbá lehetőség van a folyamatok és a szerszámműveletek testreszabására az Ön igényei szerint.
Alkalmazások
Csövek alakítása és hidroformázás
A bonyolult alkatrészek kis hajlító sugárral történő gyártásának piaci igényeire válaszul a PAM-TUBE a csövek hajlításának pontos szimulációját kínálja a szerszám valósághű modelljének alkalmazásával és pontosabb alakítási eredményekkel, azzal a céllal, hogy kizárjuk a járulékos problémákat.
A hidroformálás az alakítás egyik fejlett technológiája, amely lehetővé teszi bonyolult alkatrészek legyártását és azok felületi minőségének egyidejű javítását. A folyadék általi bővítés és a magasnyomású technikák a PAM-TUBE környezetben különállóan és kombinálva is modellezhetőek, melynek köszönhetően a szoftver lehetővé teszi a csövek alakításának összes folyamata számítógépes szimulációját.
A kezelőbarát szoftverkörnyezet lehetővé teszi a folyamat gyors definícióját és a szerszám tervezését, miközben segít ellenőrzés alatt tartani a bonyolult hidroformálási folyamatokat.
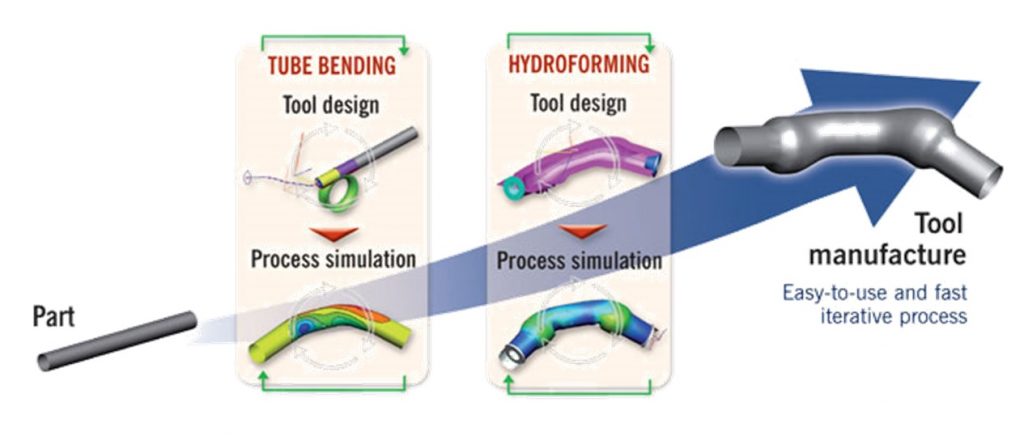
Csőalakítási folyamatok
A PAM-STAMP csőhajlítását az egyetemi és ipari intézményekkel együttműködve fejlesztették ki. A Siegeni Egyetem, illetve a DaimlerChrysler, az Audi, a Schuler Hydro Forming, a bu Engineering GmbH, a hde Solutions, az Eberspâcher és a ThyssenKrupp Budd közötti szoros együttműködés robusztus ipari szoftvert eredményezett, amely lehetővé teszi a csövek hajlításának és hidroformázásának megbízható szimulációját. Ez magában foglalja a következő funkciókat:
- Alakváltozások előrejelzése,
- Az ovalizáció előrejelzése,
- A hajlítóél gyors érzékelése,
- A hegesztési varratok figyelembe vétele,
- A szerszám testének egyszerű elhelyezése,
- A szerszám homlok felületének automatikus létrehozása,
- Többlépcsős folyamatmakrók létrehozása a hatékony munkavégzés érdekében.
- A teljesen paralellizált számítások segítenek gyorsítani a fejlesztési folyamatokat és csökkenteni a költségeket
Motorbölcső, A Thyssenkrupp Budd hozzájárulásával
Csövek hajlítása
A csövek CNC-hajlítását általában nem szimulálják, hanem tesztelik és optimalizálják a hajlítógépen a műhelyben. A csövek hajlításakor, mint közbenső gyártási lépés egy hidroformázott terméknél, a hajlítás döntő szerepet játszik. Tehát gyakran kell szimulálni, hogy pontos eredményeket érjünk el a megvalósíthatóság meghatározásában a hidroformázás során. Ha a cél egy virtuálisan gyártott alkatrész, amelyet egy szerelvény felépítésére kérnek, akkor semmi értelme elhanyagolni a gyártási műveleteket, mivel ezek meghatározzák a végső rész teljesítményjellemzőit.
A PAM-STAMP a felhasználó számára virtuális hajlítógépet kínál, amely lehetővé teszi az összes tengely vezérlését pl. a készülékre alkalmazott erők, vagy a nyomásos szerszám útja és sebessége szabályozásának vonatkozásában. A rásegítővel végrehajtott hajlítást is szimulálhatjuk. A folyamat beállítása egyszerű hajlítási görbével kezdődik, és lehetővé teszi a hajlítás alapvető ismereteivel a felhasználó számára, hogy gyorsan megkaphassa a hajlított csövet.
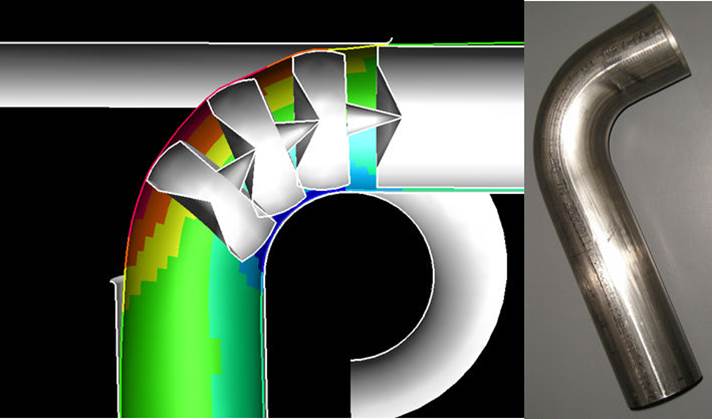
Pontos hajlítási szimuláció a tüskegömbök hatásának figyelembe vételével. A Mewag Maschinenfabrig AG hozzájárulásával
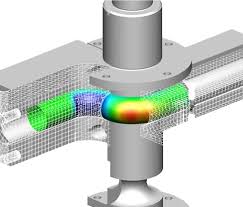
Összetett hajlítás szimulációja. A Tenneco Automotive hozzájárulásával
Hidroformázás
A hidroformázás az alkatrészek formázását jelenti folyadékok erőátvitelként történő felhasználásával, összehasonlítva a hagyományos prések által kifejtett mechanikai erőkkel. A szakosodott ipari ágazatokban a tápközeg lehet gáz- vagy műanyag pellet is, amely nem gátolja a PAM-STAMP segítségével végzett szimulációt. Vagy csövek, vagy zárt keresztmetszetű profilok alakíthatók ki belső nyomással vagy sík terítékekre ható egyoldalú nyomószerszámmal, amelyet Fluidcell-eljárásnak nevezünk, vagy a mechanikai alakítást gátló passzív ellenállással, ez az úgynevezett Aquadraw-folyamat.
A zárt keresztmetszetű alkatrészek hidroformázása során általában tengelyirányú tüskéket használnak az alkatrészek végeinek tömítésére és az anyagnak a formázó szerszámba történő benyomására, hogy az alkatrészvégek közelében lévő területeken nagyobb tágulást érjenek el. Az elágazó alkatrészekhez, például a t-darabokhoz is szükség van egy ellenszerszámra, hogy ellenőrizzék az anyag áramlását az elágazásba. Mindezeket a műszaki szempontokat a PAM-STAMP kínálta lehetőségek teljesen lefedik.
Összefoglalva: a PAM-STAMP a teljes virtuális gyártási láncot lefedi a csövek hajlításától a biztonsági elemek gyártásáig vagy a túlnyomással történő alakításig, a rozsdamentes anyagok edzésének opcionális figyelembe vételétől az aktuális hidroformázásig, az esetleges levágással és a szabadon választható befejezési móddal, vagy az azt követő mechanikus megmunkálással.
A hidroformázás tipikus vevői kihívásai hasonlóak a hagyományos fémlemez-alakításhoz, néhány kiegészítéssel. A végső alkatrésztől kezdve a PAM-TUBEMAKER hidroformázási alkatrész-tervező modul támogatja az ügyfelet a fordított tervezés munkafolyamatában a szükséges kezdeti csőig az összes kapcsolódó gyártási lépéssel, amely a végső alkatrész alakjának eléréséhez szükséges. A fordított evolúció azt jelenti, hogy a következő kihívásoknak kell megfelelniük az ügyfél előtt:
- A cső vagy szelvényrész keresztmetszetének meghatározása
- Hajlító vonal tervezése a hajlítások számának és a hajlítási sugár (általában egy sugár) kiválasztásával, amelyeket a rendelkezésre álló berendezésekhez lehet igazítani a termelési költségek optimalizálása érdekében
- Döntés egy lehetséges előalakító műveletről
- A leszállási zóna, azaz a csővég hengeres részének meghatározása
- Hidroformázó szerszám előkészítése
- A cső kezdeti méretei
A csőtől a hidroformázott részig tartó kezdeti szimuláció vagy részleges futtatás után problémák esetén az ügyfél dönthet úgy, hogy egy második vagy további lépésben optimalizálja és implementálja azt a PAM-TUBEMAKER -be, eszközöket és folyamatokat adaptálva az eredmények javítására érdekében. A szimulációs eredmények megválaszolnak minden kérdést a megvalósíthatósággal és a műhely felszerelésével kapcsolatban:
- Helyi elvékonyodás, repedések vagy ráncok megjelenése
- Speciális kenés, vagy esetleg ék használata szükséges
- A kapott alak eltérése a CAD-től és szintén az alkatrész visszarugózása
- A szükséges maximális nyomás és a kapcsolódó mennyiségek, például záró erő, vagyis a présgép nagysága
- Maximális nyomás és a vizsgált tengelyirányú elmozdulás / erő határozza meg az axiális hidraulikus hengerek méretét
A PAM-STAMP lehetővé teszi az ügyfél számára, hogy egyetlen környezetben tesztelje és optimalizálja a teljes hidroformázási folyamatot, miközben a PAM-TUBEMAKER-et választja kiindulási pontként, vagy az összes szerszámhoz és alkatrészhez rendelkezésre álló CAD adatokat felhasználhatja az ügyfél számára. A nap végén rendelkezésre áll minden szükséges adat és információ a megbízható ajánlat és a megvalósíthatósági nyilatkozat benyújtásához.
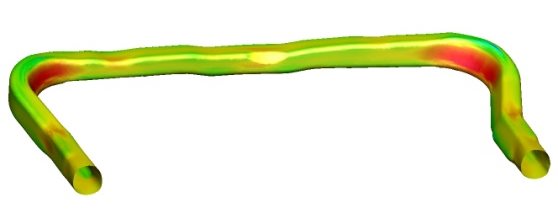
Mintadarab (valós). A Fischer Hydroforming GmbH hozzájárulásával
A kép bal oldalán látható alkatrész maximális alakíthatósága ~ 50%, s a nyomás lefolyásának manuális kipróbálása általában egyértelmű kudarchoz vezet:
Repedések a jelzett területen
Az automatikus megoldóval történő indítás után a repedés eltűnt:
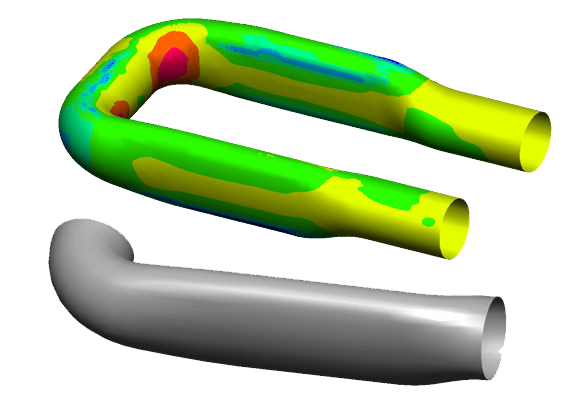
Repedések nélkül – biztonságos a gyártás szempontjából
Applications AlkalmazásokApplications
Görgős és asztali peremezés
A járműváltozatok számának növekvő tendenciája a legyártott autók számának egyidejű csökkenésével olyan költséghatékony gyártási módszereket és karosszéria-koncepciókat igényel, mint például a szegélyezés. Ez az eljárás nagyon rugalmas, és csak mérsékelt beruházásokat igényel. Ennek a szimulációnak a célja a készülékek, a programozás és tesztek mellőzése a prototípus fázisban és a kísérleti sorozatban.
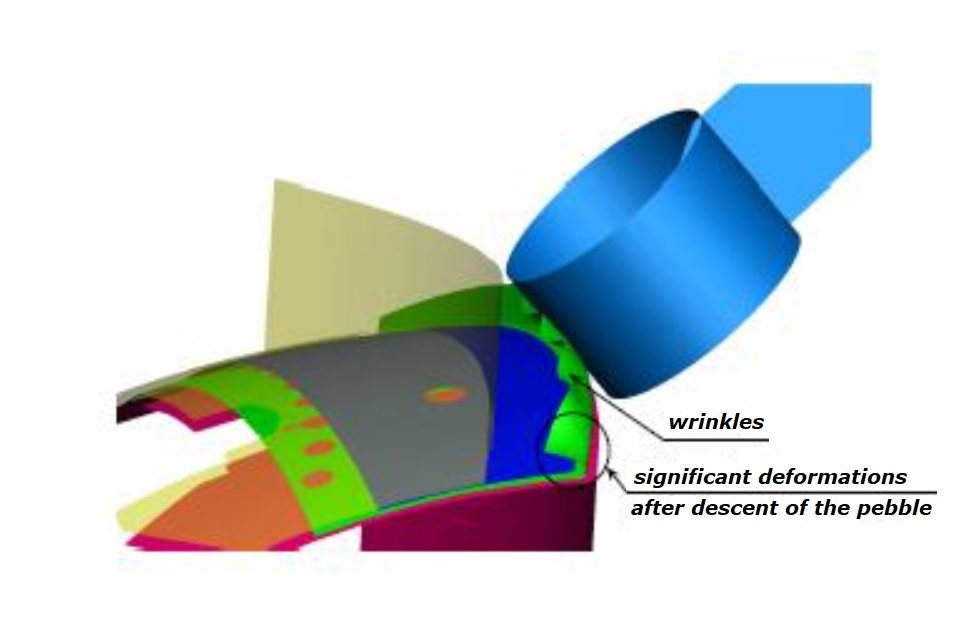
Az UBS hozzájárulásával
Az optimális és hibamentes peremezési eljárás mellett a szimuláció középpontjában a szerelvénynek az alkatrészek visszarugózása és a szegélyezés okozta alakváltozása áll. A végső külső él “beillesztése” szintén kiértékelhető.
A PAM-STAMP belsejében egy felhasználóbarát felület határozza meg a fizikai folyamatot, hasonlóan a robotkar által vezetett szegélygörgő programozásához. Ez lehetővé teszi a meglévő tapasztalatok és stratégiák szisztematikus optimalizálását az esetleges ebből adódó alakváltozások ellenőrzése érdekében. Az alkatrész vágási vonalainak helyzete, amelyek nélkülözhetetlenek a peremezéshez, optimalizálható az egyes alkatrészek eljárási sorrendjéhez.
A PSA PEUGEOT CITROËN a gépjárművek gyártósorán sikeresen használja a PAM-STAMP csomagot a görgős szegélyezés szimulációjához
Olvassa el a teljes sikertörténetet
Ajtó görgős szegélyezése
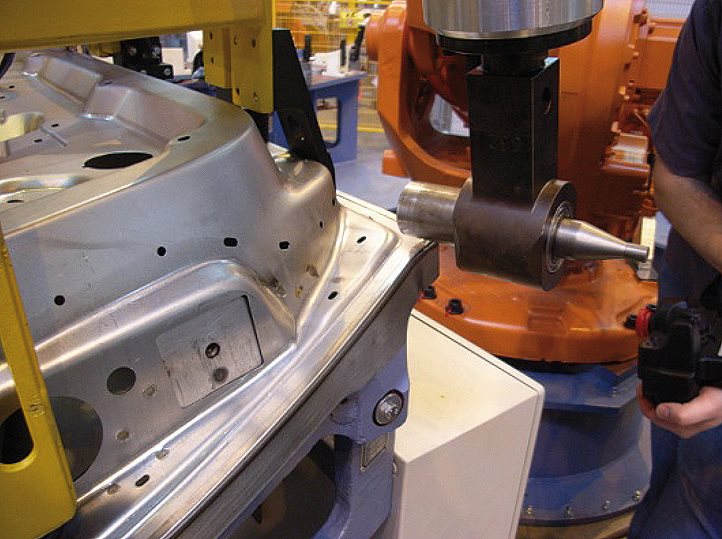
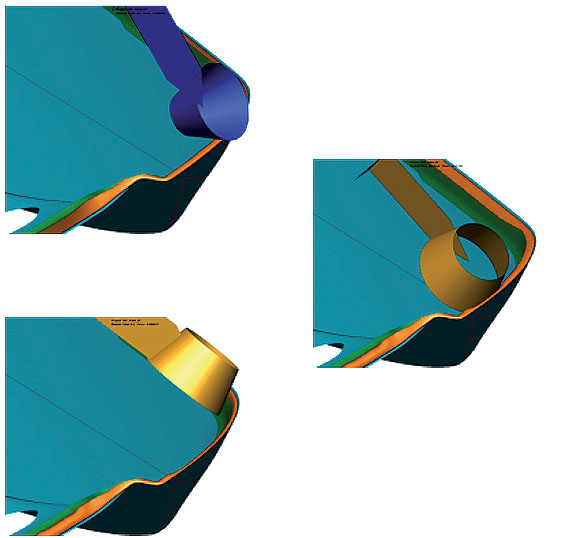
„A PSA szegélyezési szakemberei a PAM-STAMP szoftverkörnyezetbe integrálták a szegélyezés legfontosabb és legmodernebb fizikai paramétereit. Ez az új eszköz nagyon gyorsan kulcsfontosságúvá vált a termék pontos definíciója és a vele járó folyamatok sikeres megvalósíthatósága terén, ugyanis valós ipari eseteken lett tesztelve és validálva.”
Patrice Auger, A gyártási folyamatok kutatás-fejlesztési igazgatója, PSA-Peugeot-Citroën
Alkalmazások
Hotformázás
Fentebb már feldolgozva!
Alkalmazások
Szuperképlékeny alakítás
Szuperképlékeny alakítás PAM-STAMP használatával
A Szuperképlékeny alakítás egyes alumínium és titán ötvözetek mechanikai viselkedésére jellemző, amellyel nagyon magas szívósságot érhetünk el, mely lehetővé teszi bonyolult alakok elkészítését is, amelyeket más módon lehetetlen megvalósítani. Ezt a technológiát a légi ipar már régóta kihasználja, de az autóiparban is egyre nagyobb teret kap a kis darabszámú autógyártás területén.
Ennek ellenére – megtervezni a folyamatot úgy, hogy bizonyosak legyünk az ezekben a drága anyagokban rejlő potenciál kiaknázásában, nagyon összetett és nehéz feladat. A PAM-STAMP beépített moduljai segítenek meghatározni a folyamat javasolt menetét és optimális paramétereit, melynek célja a folyamat idejének és a felhasznált anyag mennyiségének optimalizációja.
A Superform USA a PAM-STAMP szoftvercsomagra hagyatkozik a bonyolult szerszámok tervezésekor és ezek virtuális megvalósíthatósági tesztjeikor.
Olvassa el a teljes sikertörténetet
„A PAM-STAMP megváltoztatta sebességünket, amellyel képesek vagyunk meghatározni az elvékonyodás mértékét vagy az alakítási ciklusidőket. Tekintettel arra, hogy szerszámaink tervezésénél igénybe vesszük megérzéseinket, tapasztalatunkat és kreativitásunkat, a PAM-STAMP segít tesztelni ötleteink megvalósíthatóságát anélkül, hogy fémhez kelljen nyúlnunk.”
A. J.
Barnes,
A Superform USA műszaki elnökhelyettese.
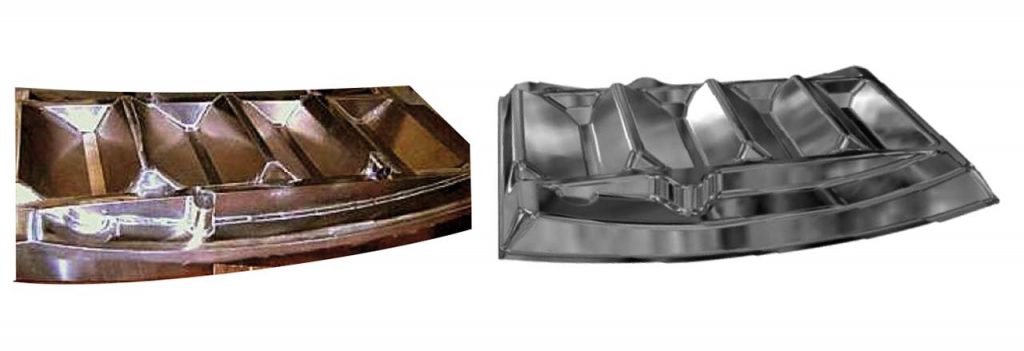
Az eredeti 23 elemből álló hegesztett konstrukció (balra) és az egy darabos szuperképlékeny alakításra optimalizált szerkezet (jobbra)
Alkalmazások
Nyújtási formázási eljárások
Nyújtási formázási eljárások PAM-STAMP szoftverkörnyezetben
A nyújtási formázási eljárásoknak számos változata létezik, kezdve a profilok nyújtásos hajlításától a panelek nyújtással történő alakításáig, a repülőgép-törzspanelektől a szárnyak belépő élének kialakításáig.
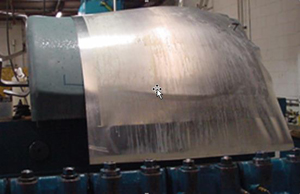
A motor tolóerő-váltójának belső burkolataA A folyamat meglehetősen kényes, és fontos megtalálni a folyamatparaméterek megfelelő egyensúlyát a jó minőségű alkatrészek előállítása és a hibák elkerülése érdekében – különösen akkor, ha az aeronautikában használt alumínium és titán alapanyagának költségei ilyen magasak. A PAM-STAMP-et széles körben használják az aeronautikában az ilyen típusú eljárásokkal előállított alkatrészek formázási minőségének előrejelzésére. Ezen túlmenően az ezekre a folyamatokra jellemző komplex kinematika elemezhető és optimalizálható a PAM-STAMP segítségével. Természetesen a visszarúgózás és annak kompenzációja is kiszámítható és optimalizálható. Triform Press hozzájárulásával
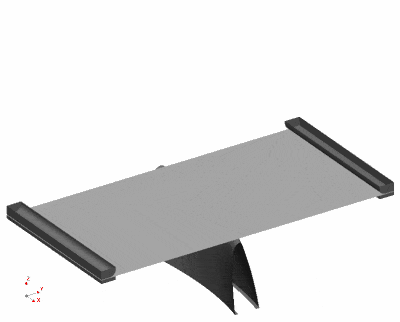
Szárny belépő éle A Triform Press hozzájárulásával
A fentebb leírt animált nyújtási formázási folyamat során három formázási típust értékeltek – a mélyhúzást, hidroformázást és a nyújtási formázást. Végső soron a nyújtás formázása adta a legjobb általános alakítási eredményeket. A legkonzisztensebb végvastagság, csökkent visszarugózás és a szerszámnyomok kiküszöbölése a külső felületen.
Alkalmazások
Gumiba történő alakítás
Gumiba történő alakítás a PAM-STAMP segítségével
A kis volumenű
gyártóipar számára, mint például a légi ipar, a gumiba történő
alakítás nagyon érdekes gyártástechnológiát kínál – lehetővé
teszi ugyanis nagyon bonyolult felületek kialakítását is. A luxus
kategóriájú autók optikai elemek gyártásánál is lehetőség
van a rendkívüli minőségű felületek előállítására anélkül,
hogy a szerszám érintkezzen az alkatrésszel. A PAM-STAMP
segítségével lehetséges virtuálisan definiálni a gumiba történő
alakítási folyamat paramétereit, mint például a nyomás időbeli
lefolyása stb.
Szintén
lehetőség van a visszarúgózás és az ebből adódó
kompenzáció numerikus analízisére is.
A Harbin Aircraft Industry a PAM-STAMP szoftvernek köszönhetően sikeresen implementálta a gumiágyba történő alakítás szimulációját
Olvassa el a teljes sikertörténetet
A PAM-STAMP segítségével képesek vagyunk ellenőrizni termékeink minőségét. Ezen felül, a kiadásokat és a szükséges időt is csökkentettük harminc, esetenként akár 50 százalékkal is. A szoftver munkánk alapeszközzé vált.“
Liu Junji úr, Harbin Aircraft Industry Group Co. Ltd. Műszaki igazgató helyettese
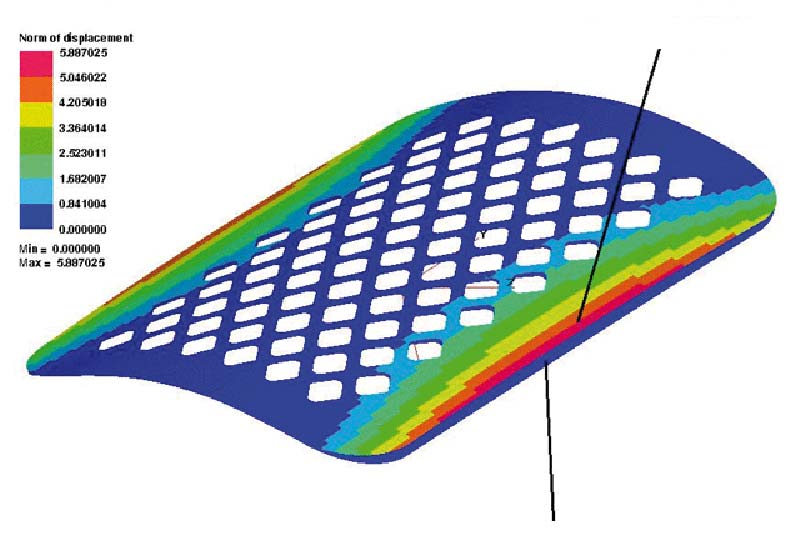
A visszarúgózás kompenzációjának eredménye a végső alkatrészen
Készen áll a licenc megszerzésére?
Több információt szeretne?
Az ESI Group-ról
A cég 1973-as alapítása óta, az ESI Group a Virtuális Prototípuskészítés világméretű újítója és az ipari transzformáció globális vezetője. A cég egyedülálló anyagfizikai ismereteinek köszönhetően az elmúlt 45 évben fejlett szimulációs módszereket fejlesztett ki és folyamatosan tökéletesíti azokat. Miután felismerte a hiányosságokat a termék életciklus-menedzsmentjének (PLM) hagyományos megközelítésében, az ESI holisztikus módszertant mutatott be, amelynek középpontjában az ipari termelékenység és a termék mindent átfogó életciklusának teljes teljesítménye állt, azaz a termék életciklusától a gyártásig és az azt követő üzemeltetésig. Az ESI a világ 20 országában az összes jelentős ipari szektorban jelen van, és mintegy 1200 nagyon magasan képze