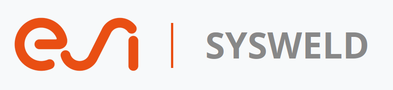
Enable Virtual Verification and Validation of Multi-Material Joining of Industrial Structures and Assemblies with Simulation
Higher efficiency & repeatability, increased quality & safety, and shorter development cycle time with a lower cost are key driving factors in modern welding & assembly body shops of manufacturing industries. Product designers, manufacturing process planners, and welding engineers must secure the above mentioned KPIs. Moreover, industries are shifting to lightweight materials such as high-strength steels and aluminium, which pose additional challenges during designing and validation phases as these advanced materials are harder to work with due to high spring back and require precise heat control. Like with every industry, competition is fierce, so industries do not have time to test different welding & assembly designs or approaches and have very little room for error – it’s very much a ‘get it right the first time’ mentality.
ESI SYSWELD, a result of 30+ years of continuous engagement with major global industrial partners, offers a unique and comprehensive virtual assessment of material characteristics, microstructure, residual stresses and distortions in welded structures and assemblies. SYSWELD addresses different welding processes (arc, electron beam, laser and spot welding) and heat treatment processes (carburizing, carbonitriding, and quenching) and considers all relevant phenomena (chemical, thermal, metallurgical and mechanical).
With all of this, SYSWELD allows engineers to be as productive as possible by building physically realistic virtual structures in the development phase to ensure improvement in the quality and performance of the manufactured products. Moreover, by coupling different manufacturing processes, our customers can simulate various process chains with upstream and downstream welding processes for design & upfront process feasibility evaluations and detailed validation to ensure cost-efficient product and production planning and drive increased profitability and margins.
Benefits of SYSWELD
- Minimizes the time and cost to market by shorting product development cycle
- Reducing the need for physical prototyping
- Controlling and optimizing material characteristics, joining process and weld quality
- Keeping distortions within specified tolerances
- Enhancing product performance and overall service life of welded structure
Did you know that Sysweld offers technology and process design solutions from welding:
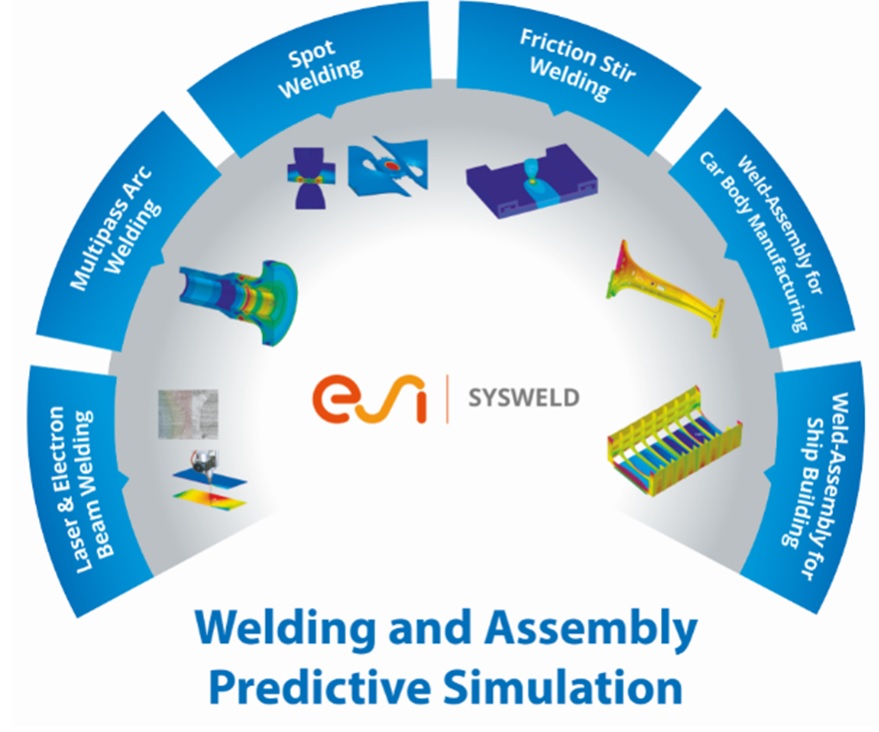
Distortion Control for Body-in-White Assemblies
ESI SYSWELD enables the designers and process planners to virtually manufacture, assemble, and test physically realistic virtual assemblies, long before their hardware prototypes are manufactured. You can now ensure the dimensional accuracies (geometrical quality) of hot and cold joined assemblies by accounting for the mechanical load effects during successive assembly processes, and heat effects induced by welding. You can:
- Manage tolerances at various levels from planning to fabrication validation
- Avoid distortions due to gap closing and effects of hot and cold joining processes
- Decide the type, location, sequence, forces of the clamps
- Identify the influence of gaps and joining process on the assembly distortion
- Control distortions by weld sequence optimization
As part of the simulation of the assembly of stamped parts, the work procedure takes into account several technological steps and operations:
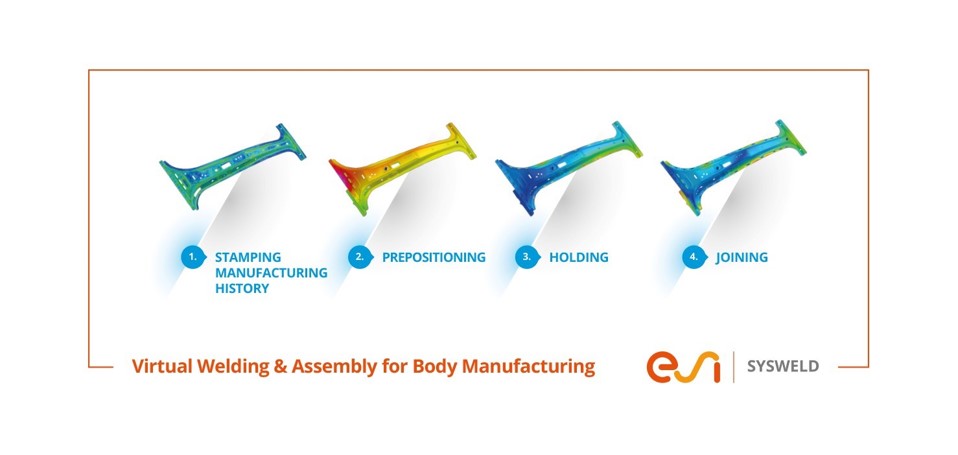
Weld Quality and Performance
Welding & Assembly simulation minimizes the cost throughout different phases of product development, such as designing, manufacturing planning, try-out, and fabrication validation. ESI SYSWELD is the most accurate Finite Element Analysis (FEA) multi-physics software on the market to simulate thermal joining (arc, electron beam, laser, friction stir, spot welding). By accounting for all relevant manufacturing effects and enabling the transport of simulation results from one manufacturing step to the next, SYSWELD delivers a truly predictive end-to-end solution for the manufacturing of welded and assembled industrial parts.
Your Benefits:
- Develop and optimize a welding plan in a short time frame
- Work with all industrial structural steel, aluminium, complex materials, or dissimilar metals
- Secure process feasibility, security with lower cost, and cycle time
- Keep welding distortions within allowable tolerances
- Control high residual stresses in the welding structures for quality assessment
- Improve crash and fatigue performance of the product
Sysweld as a unique solution has implemented the following welding and assembly procedures for car body production:
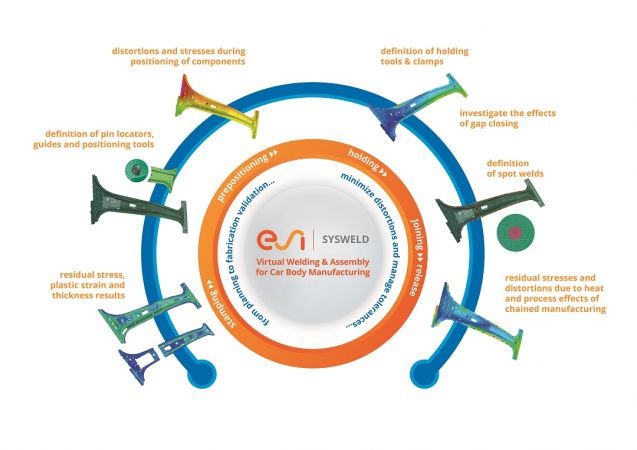
Distortion Control in Automotive Industry using Virtual Welding & Assembly
Benefiting from years of developments aimed at the automotive industry, SYSWELD enables the modeling of the full stamp-welding-assembly simulation chain for fast distortion engineering in the context of car body manufacturing.
Design engineers can now control the dimensional inaccuracies of hot and cold joined assemblies by accounting for the mechanical load effects during successive assembly processes, and heat effects induced by welding.
Engineers can virtually manufacture, assemble and test physically realistic virtual components, long before their hardware prototypes are manufactured.
Automotive manufacturers and their suppliers can consequently reduce the cost and delays caused by manufacturing planning, try-out and process validation.
The output of the weld quality simulation are the following main physical quantities:
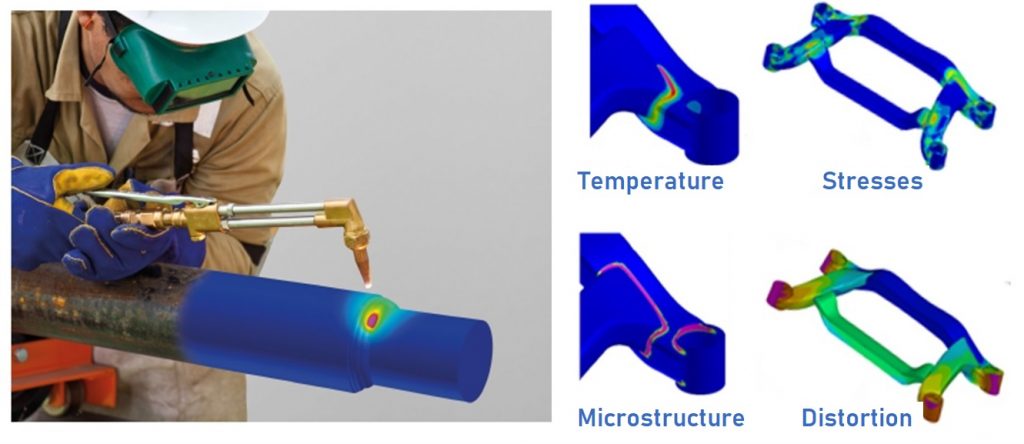
Heat Treatment Simulation
SYSWELD addresses heat treatment processes (Carburizing, Carbonitriding, and Quenching, etc.) and considers all thermal, metallurgical, and mechanical phenomena.
Your Benefits :
- Avoid component distortion and high material hardness during or after heat treatment
- Obtain correct material strength, toughness, and hardness
- Ensure high wear resistance of the contacting surfaces
- Achieve the required distribution of residual stresses
Did you know that Sysweld offers technology and process design solutions forn heat treatment:
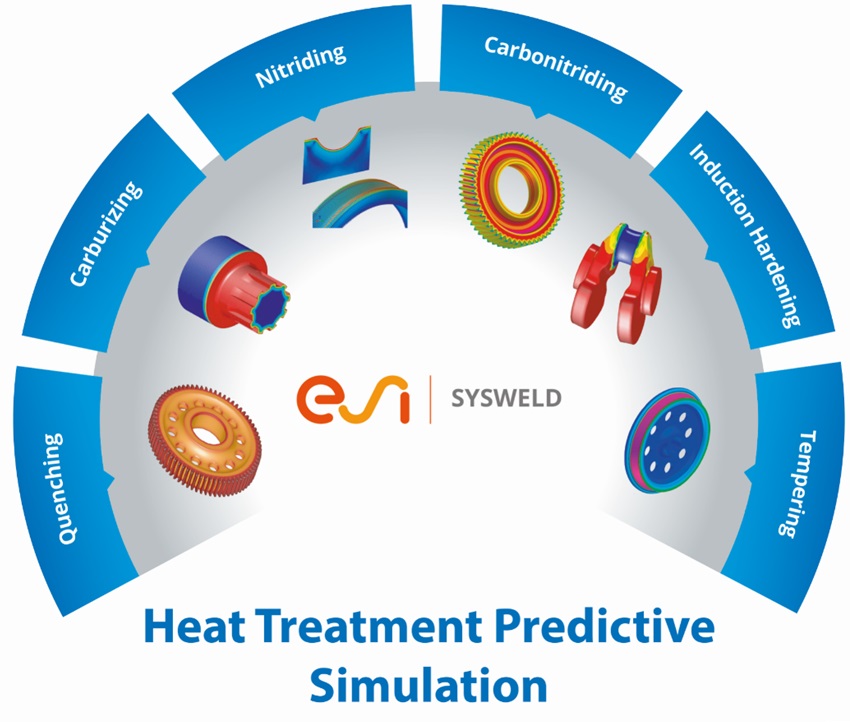
About ESI Group
Ready for a license?
Looking for more information?