FFS a procedure - which also includes several engineering disciplines - which is designed to decide whether a given piece of equipment is suitable for continued operation with given operating parameters.
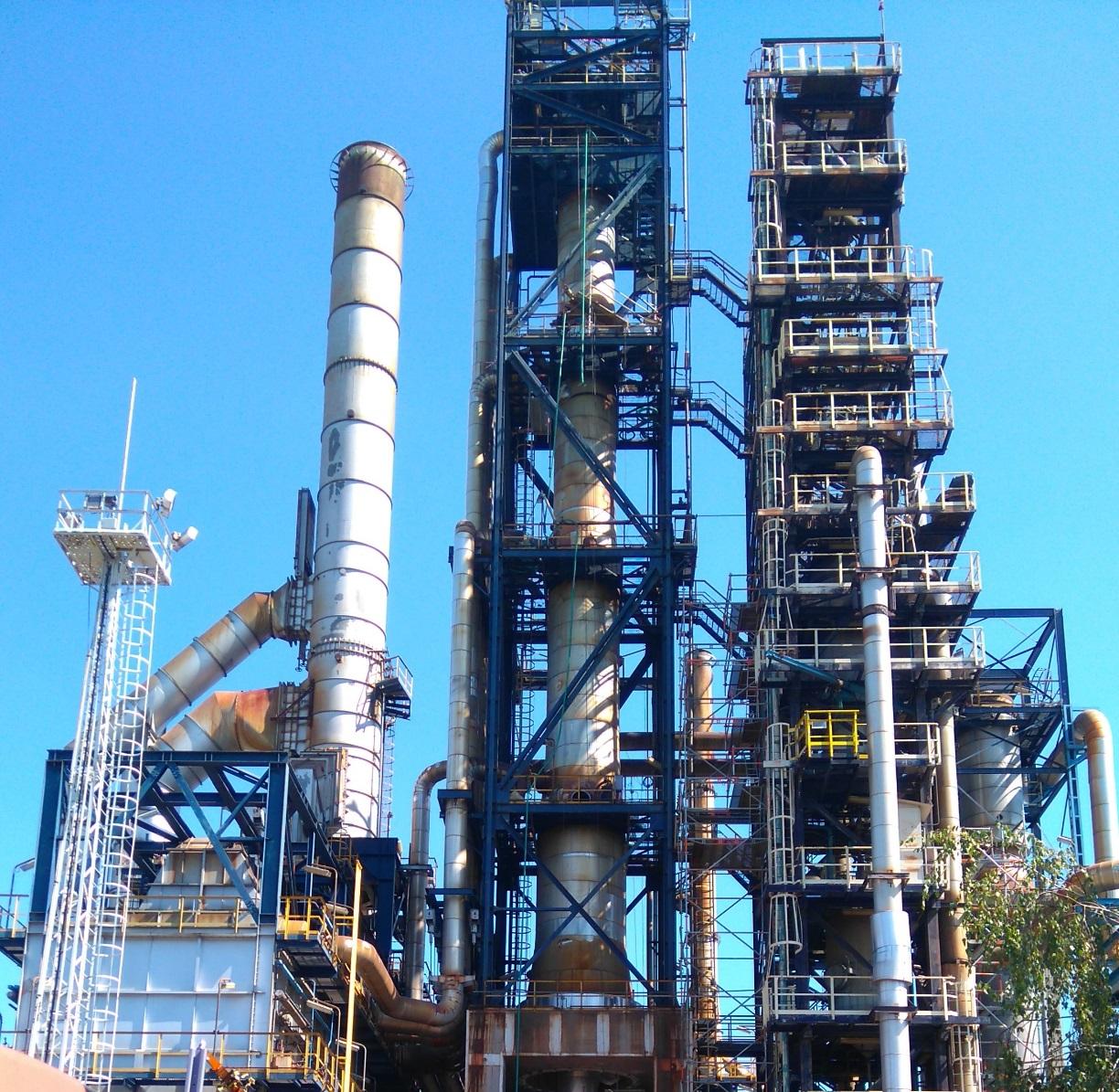
During the FFS procedure, it may become necessary to involve several engineering disciplines, on the basis of which important test and calculation data will be available. These areas of expertise may include the following:
- Stress Analysis: the exact stress distribution of the equipment must be determined in order to perform any kind of remaining life calculation (analytical, numerical methods).
- Material Engineering : it is crucial to know the properties of each type of material at different environmental, temperature and stress levels.
- Nondestructive Examination (NDE) : individual material continuity defects must be identified according to their location and size before they cause failure. The choice of the most suitable inspection procedure depends on many factors, starting from the type of defect to their location and the accessibility of the current area.
- Corrosion : knowledge and understanding of the mechanism of environmental degradation leading to failures is a prerequisite for FFS. Furthermore, knowledge of corrosion processes is extremely useful in ordering appropriate remediation steps.
- Plant Operations : continuous contact with operating specialists is essential and necessary in order to understand and evaluate the operating parameters of the given equipment. Information such as operating temperature and pressure, operating environment and shutdown/run-up cycles are essential inputs to a successful FFS.
- Fracture Mechanics : this engineering science is used to analyze micro- and macro-discontinuities in the material.
- Probability & Statistics: the statistical analysis of the data collected during operation is an extremely important part of both the FFS process and the possible future risk analysis.
There are many advantages to using the FFS procedure:
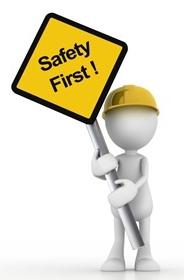
Safety : despite the fact that risk is an inseparable part of the oil industry and the industry dealing with the processing of high-pressure liquids and gases, SAFETY should be an important goal for every ethically thinking company. The FFS minimizes the risk level, it can be used to decide whether or not the continued operation of a long-standing equipment that may have degraded during operation is safe or not.
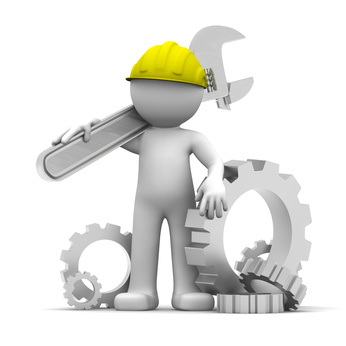
Economic benefit : in addition to the obvious increase in the safety level, the use of FFS also has a fundamental economic advantage. The planned FFS during operation reduces the probability of unannounced, unplanned shutdowns due to equipment failure, thus preventing costly and unplanned component and equipment replacement. If a malfunction (material discontinuity, crack, etc.) is discovered during normal operation, FFS can be used to decide whether or not the equipment can be operated safely until the next scheduled shutdown.
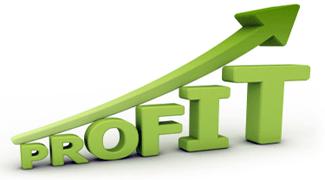
Improved Yield : it is less visible, but another significant advantage of using FFS can be the increase in the company's income. If the lifetime of a piece of equipment can be accurately determined with the help of FFS, the technology can continue operating between downtimes much more boldly and thus more efficiently. Even if replacement of certain components becomes necessary more often, the more efficient utilization level of the entire equipment itself results in higher output, thereby generating higher revenue and profit for the company.
The API/ASME FFS standard procedure defines 3 evaluation levels:
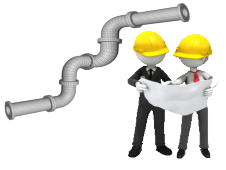
Level 1 : this is the simplest, so-called basic evaluation procedure, which can be performed by an experienced inspector or plant engineer.
- simple manual calculations can also be performed during the process
- necessarily the most conservative valuation level (sometimes Level 2, 3 suits, but Level 1 not)
- In some cases Level 1 not allowed (e.g. seismic load, wind load, etc)
- In case of Level 1 the procedures prescribed in the FFS must be followed exactly, there is no room for independent or individual interpretation.
- necessarily the most conservative valuation level (sometimes Level 2, 3 suits, but Level 1 not)
- In some cases Level 1 not allowed (e.g. seismic load, wind load, etc)
- In case of Level 1 the procedures prescribed in the FFS must be followed exactly, there is no room for independent or individual interpretation.
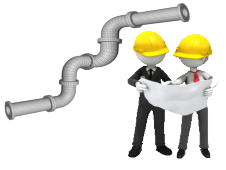
Level 2 : is more complex assessment procedure than Level 1, which can be carried out by an engineer trained in FFS. Most Level 2 calculations are done on predefined worksheets.
- the course and form of the calculations performed during the process are predefined according to FFS
- During the application of Level 2, greater engineering leeway is allowed in terms of technical decisions
- the engineer performing the evaluation must be familiar with FFS procedures
- During the application of Level 2, greater engineering leeway is allowed in terms of technical decisions
- the engineer performing the evaluation must be familiar with FFS procedures
Equipment may contain defects, material deficiencies, cracks, breaks, corrosion and other defects. It may be the outcome of the FFS procedure:
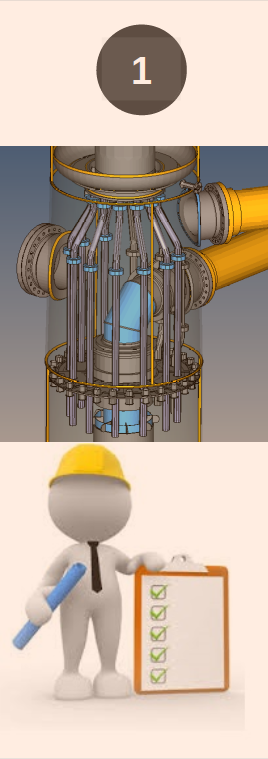
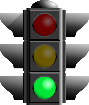
Operation can
continue
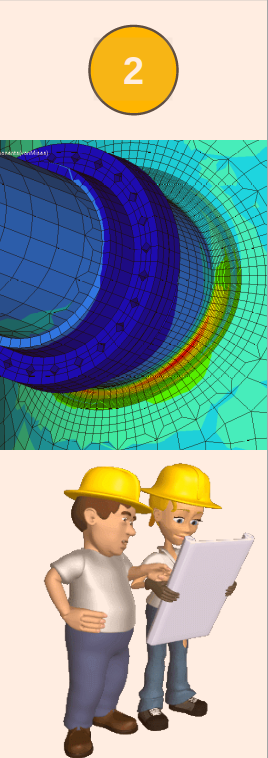
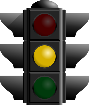
Remaining lifetime computation
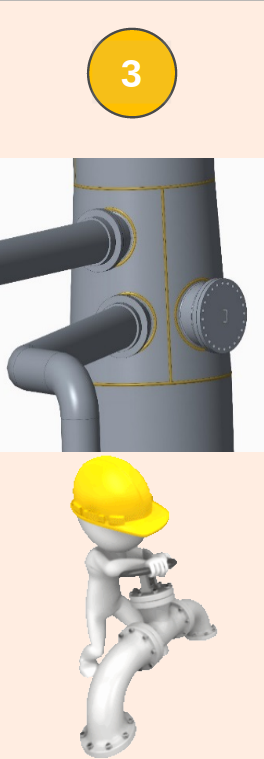
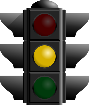
Modification of operating parameters
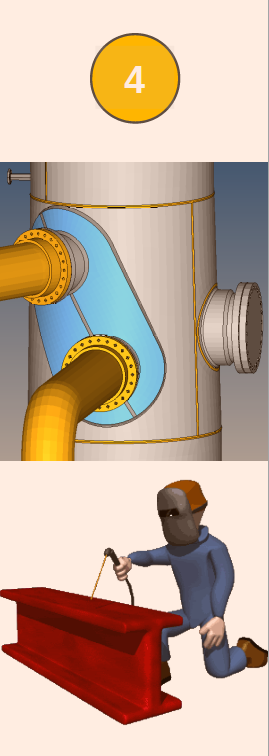
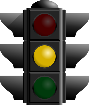
It can be operated after repair
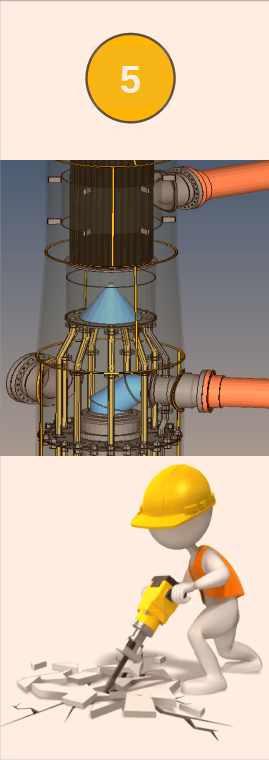
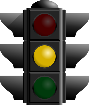
Conversion of equipment
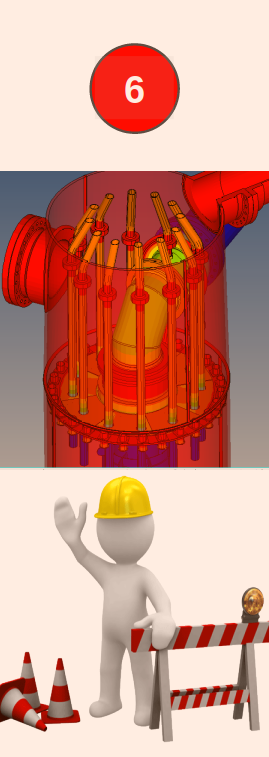
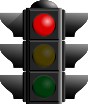
Equipment shut down