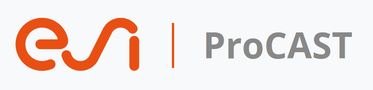
Solution to foundry problems
With our casting solutions you can Get it Right the fi rst time and enhance your productivity & profi tabilityESI’s Casting Simulation Suite, ESI ProCAST , provides a complete set of solutions for the foundry industry. An advanced tool which is the result of more than 25 years of collaboration with major industrial partners and academic institutions across the world, ESI ProCAST offers an extensive suite of modules and foundry tools to meet today’s challenging industrial requirements. Based on the powerful Finite Element Technology, ESI ProCAST enables predictive evaluations of the entire casting process, including filling and solidification defects, mechanical properties and complex part distortion. It enables rapid visualization of effects of design changes and provides a basis for correct decisionmaking, from the earliest stages of the manufacturing process.
ESI ProCAST enables the modeling of all casting processes for all castable alloys, and also addresses other foundry relevant manufacturing process like core blowing & heat treatment.
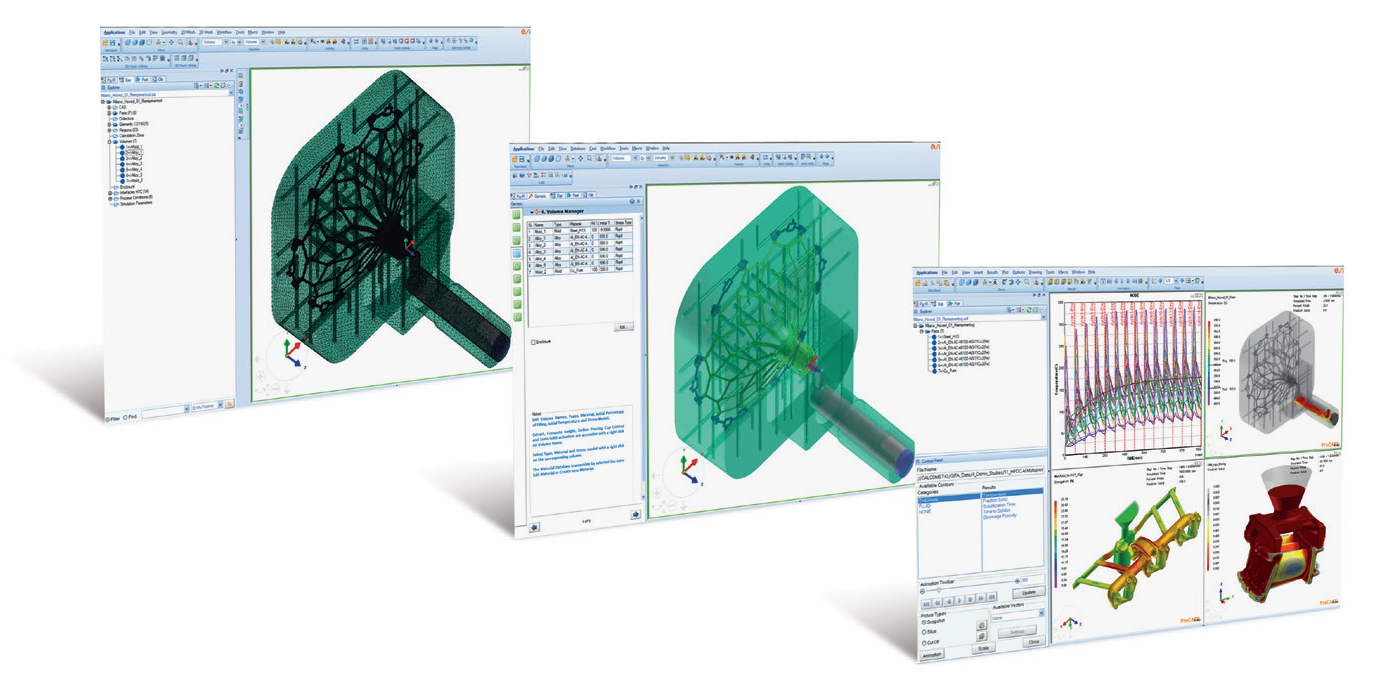
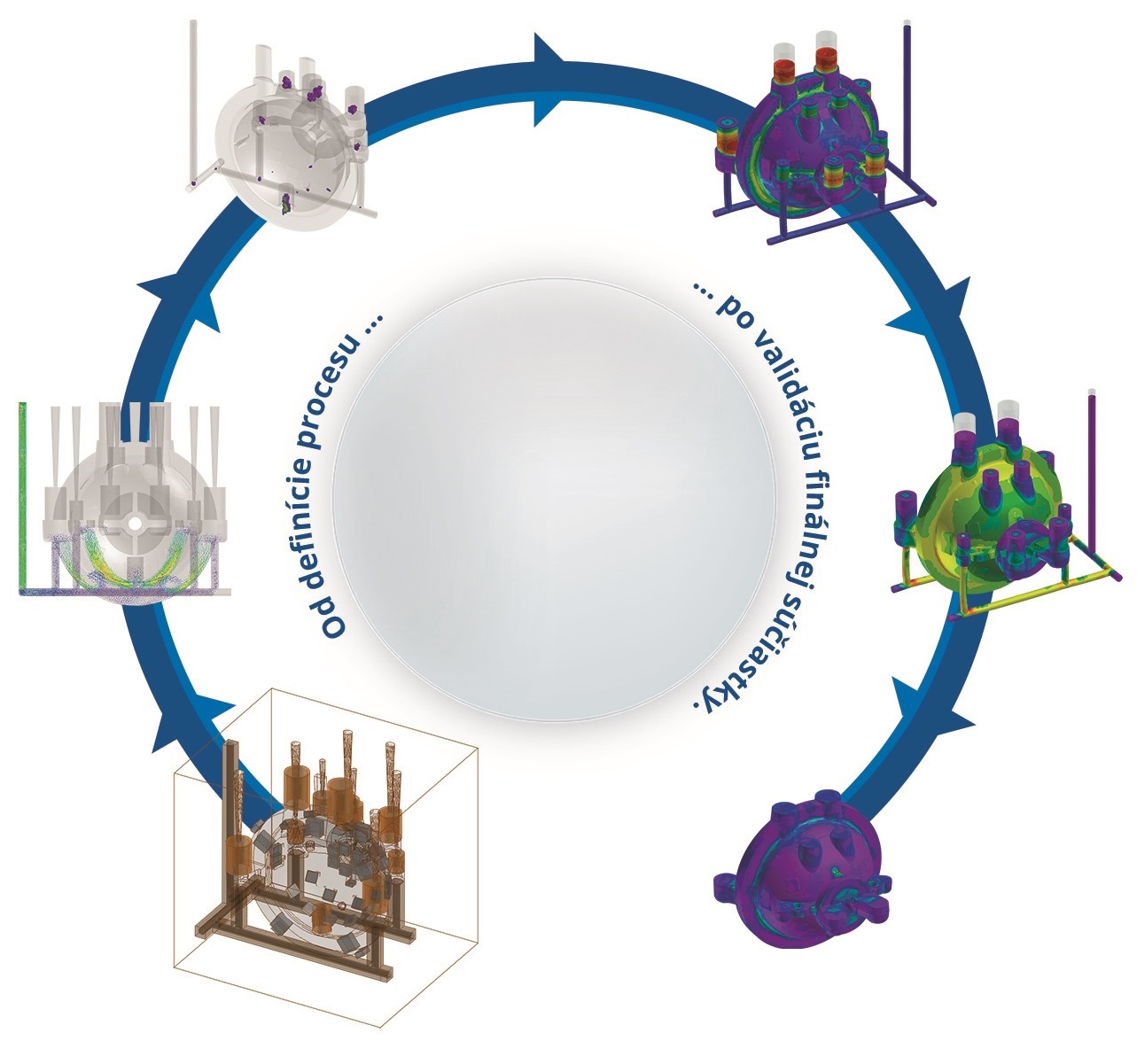
Visual-Environment: A Streamlined and Productive Interface
ESI’s Casting Simulation Suite , ProCAST, is fully integrated with ESI’s open collaborative engineering environment, Visual-Environment, allowing for interoperability and chaining between casting software and other simulation disciplines. Within Visual-Environment you can find Visual-Mesh, Visual-CAST, Visual-Viewer and Visual-Process.
A Visual-Mesh comes with a CAD reader and specific tools to facilitate the link between CAD environment and meshing operations.
A Visual-CAST provides foundry tailored wizards and data checks which guide users to set-up their casting process. An extensive material database is available with standard and commonly used alloys, dies, chills, sand molds & cores, ceramics, filters, insulation & exothermic sleeves. In addition, it also features a unique thermodynamic material database calculator which allows the user to directly enter the chemical composition of the alloy and automatically predict temperaturedependent properties required to accurately simulate the casting process.
A Visual-Viewer is a complete, productive and innovative postprocessing environment for foundry applications with a state-of-theart plotting and animation control solution. It enables you to boost the productivity of your foundry engineers by performing automated tasks and generating customized reports within a multi page/window environment.
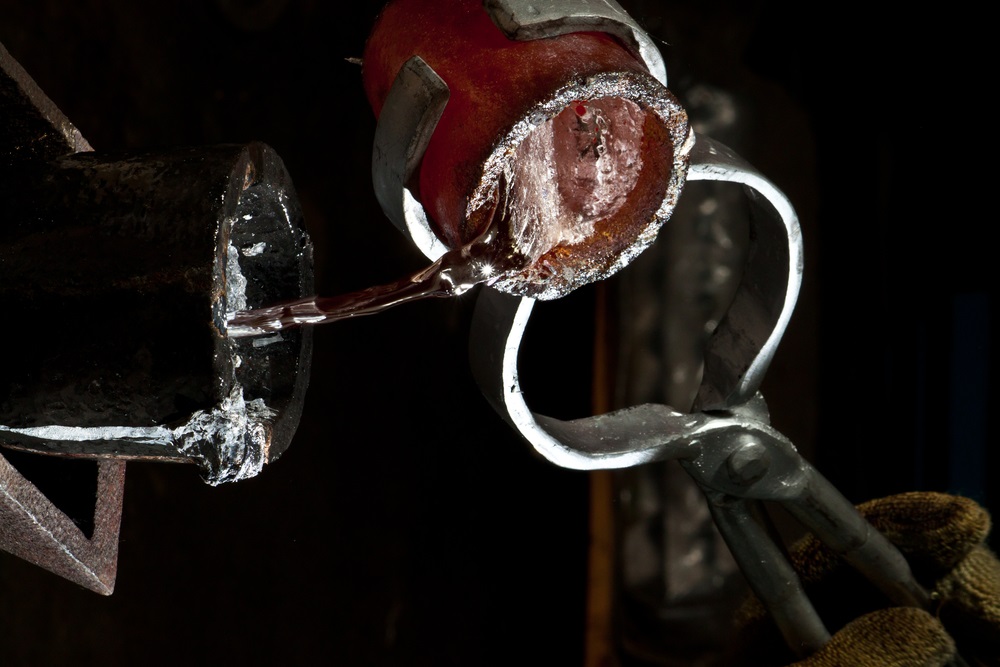
Originally created in 1985 by foundry professionals from Aluminum Pechiney, ESI’s QuikCAST is today fully integrated into ESI’s ProCAST and available in the Visual-Environment. ESI’s QuikCAST meets industrial needs delivering rapid and realistic predictions, allowing foundrymen the ability to simulate the entire casting process from fi lling to solidifi cation, including defects prediction.
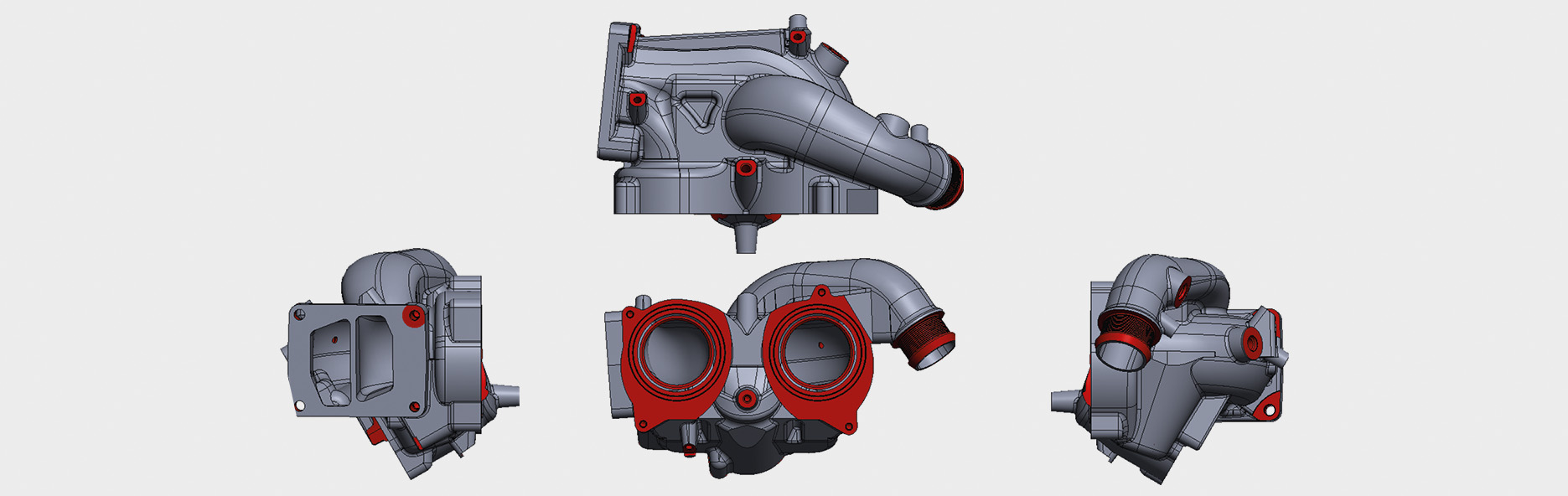
A ProCAST Szoftvercsomag felépítése
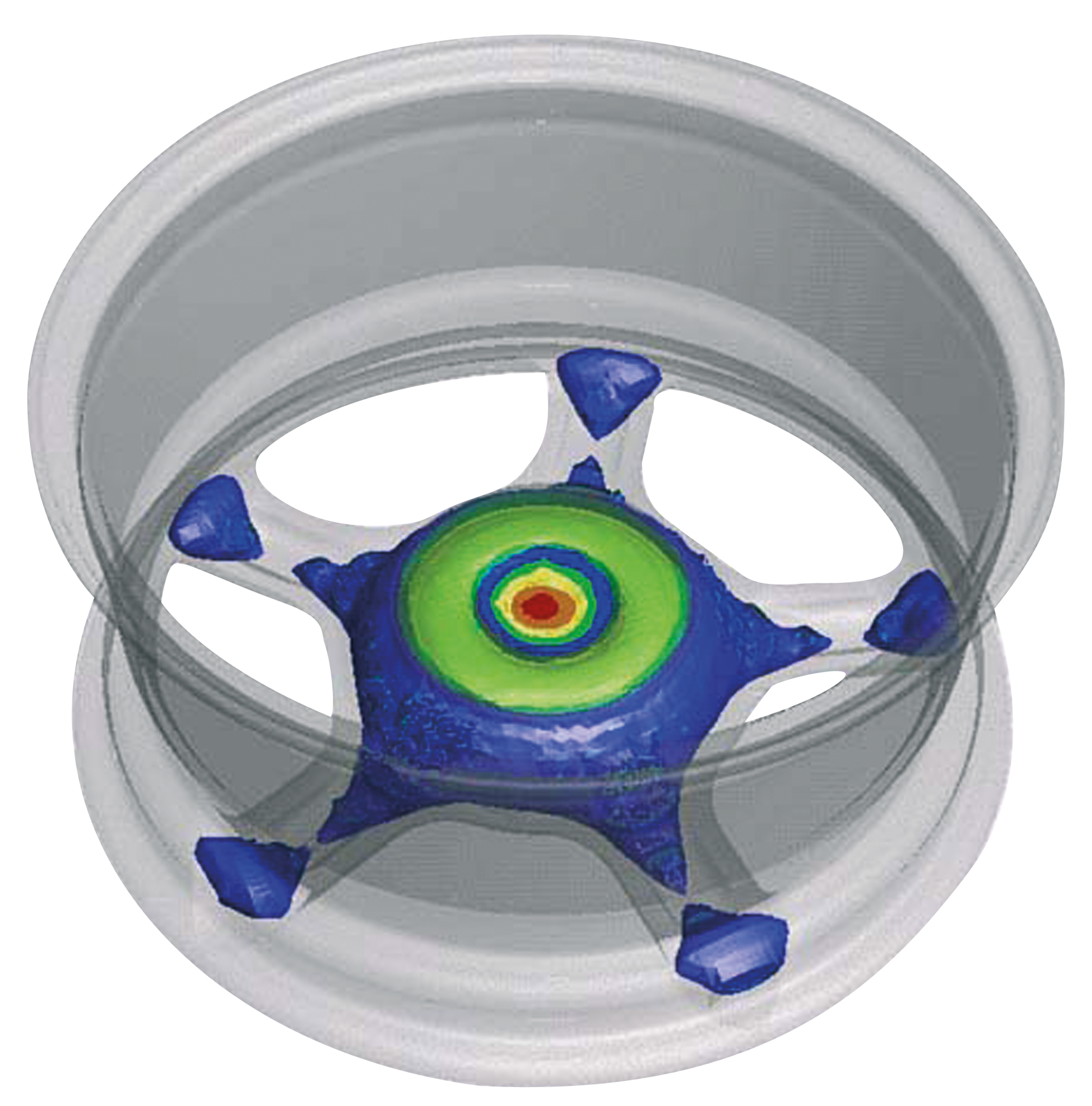
Base Package
Specific Process
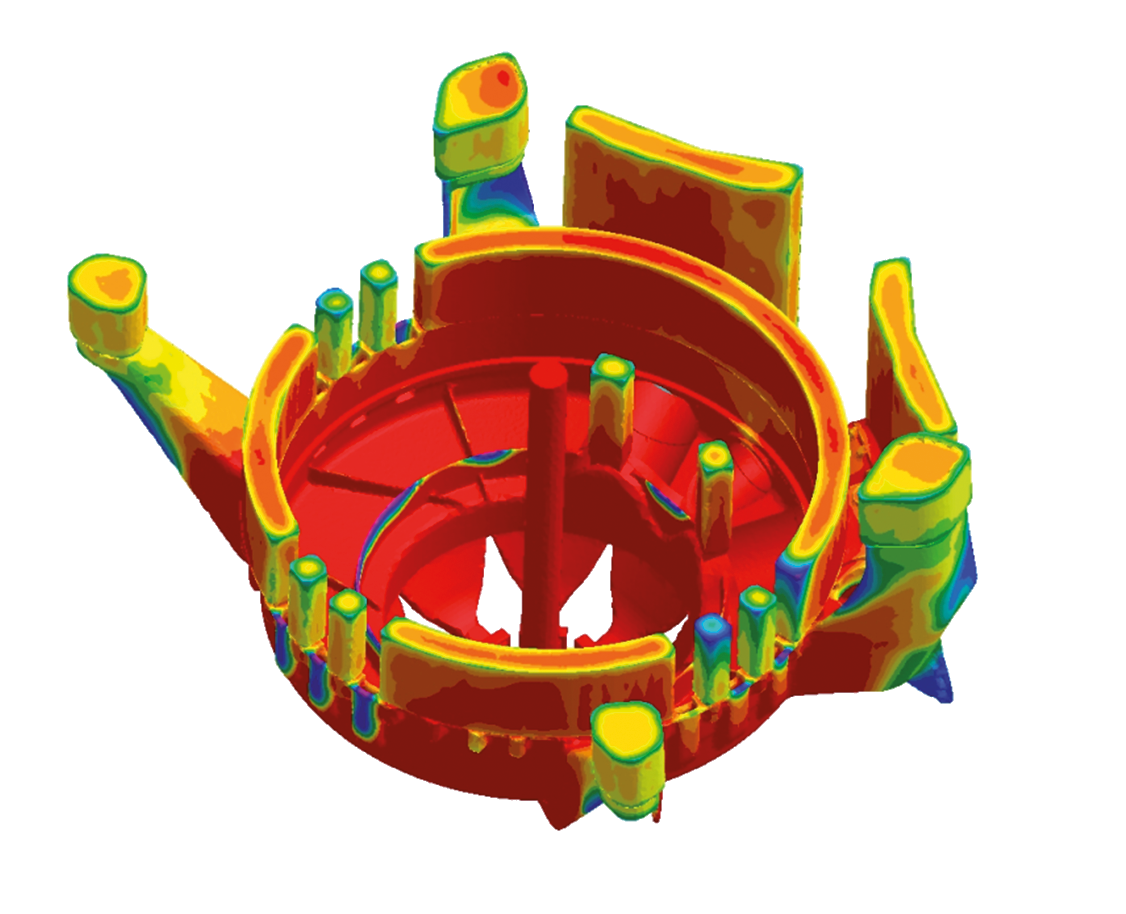
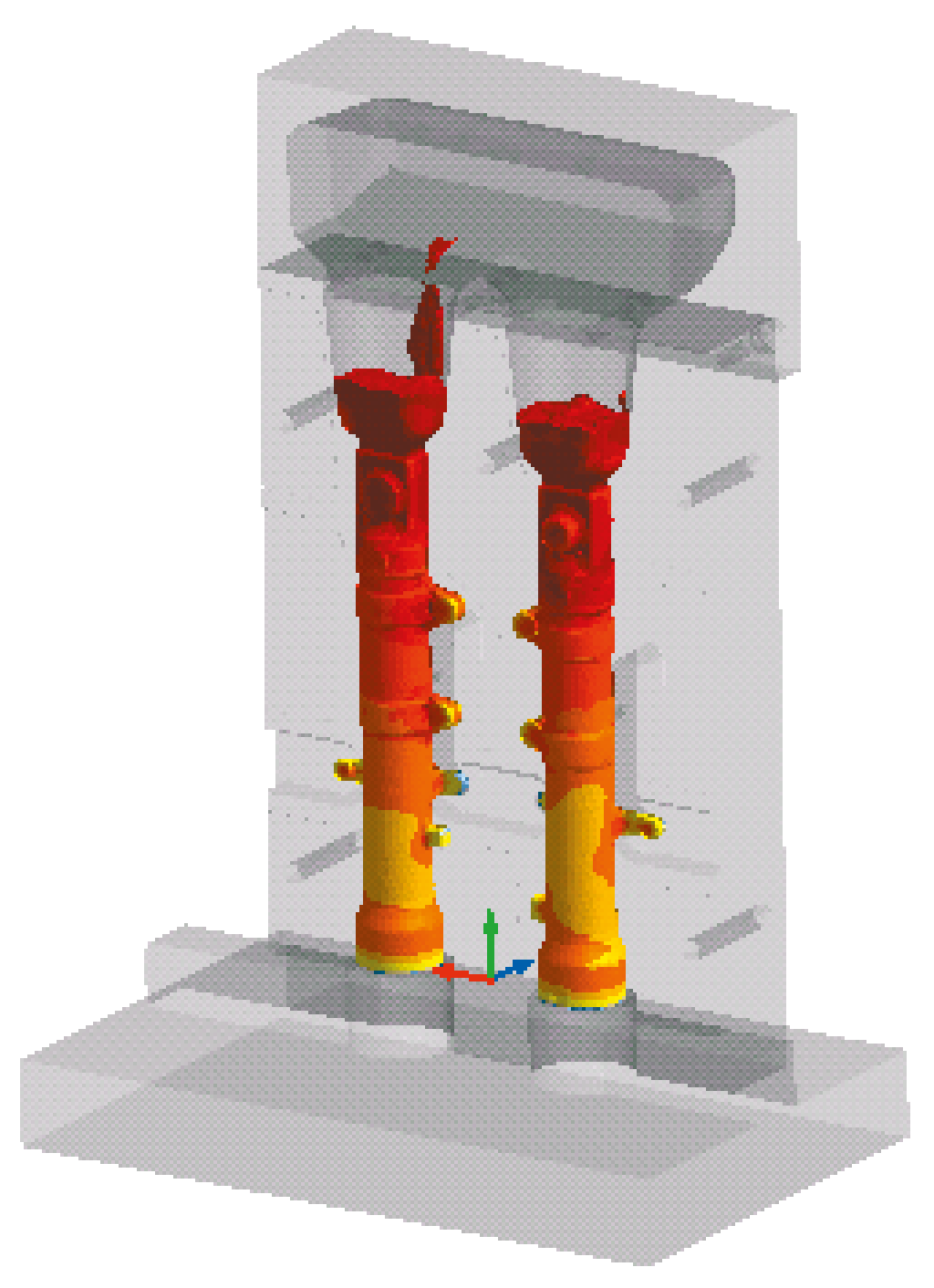
Decision-Making
Physics - Advanced Analysis
Microstructure formation is an important phenomenon affecting the end properties of an ‘as cast’ component. ProCAST allows for the calculation of the types of phases present - the volume fraction of the phases, the grain size, and grain shape - which all determine the mechanical properties.
The solid state phase transformation and the resulting mechanical properties during heat treatment can also be simulated with ProCAST using models based on Time- Temperature-Transformation (TTT) or Continuous Cooling- Transformation (CCT) diagrams.
The microstructure solver also calculates the macro-segregation based upon the composition of the alloy.
Originally developed by Rio Tinto Alcan, a heat treatment advisor calculates the mechanical properties (YTS, UTS, E% and HB) throughout the entire range - from T4 through T6 and T7 - based on Mg variation and aging parameters for the most commonly poured aluminum A356/357.
Grain structure of ‘as cast’ components are important for controlling casting conditions and optimizing component performance. ProCAST computes grain structure, including columnar to equiaxed transitions, for any dendritic alloy. It allows controlled solidification conditions to generate single crystal or directionally solidified grain structure. ProCAST couples a Cellular Automaton (CA) model with the Finite Element (FE) heat flow computations. For this reason, the grain structure module of ProCAST is often referred to as the CAFE module by industry experts.
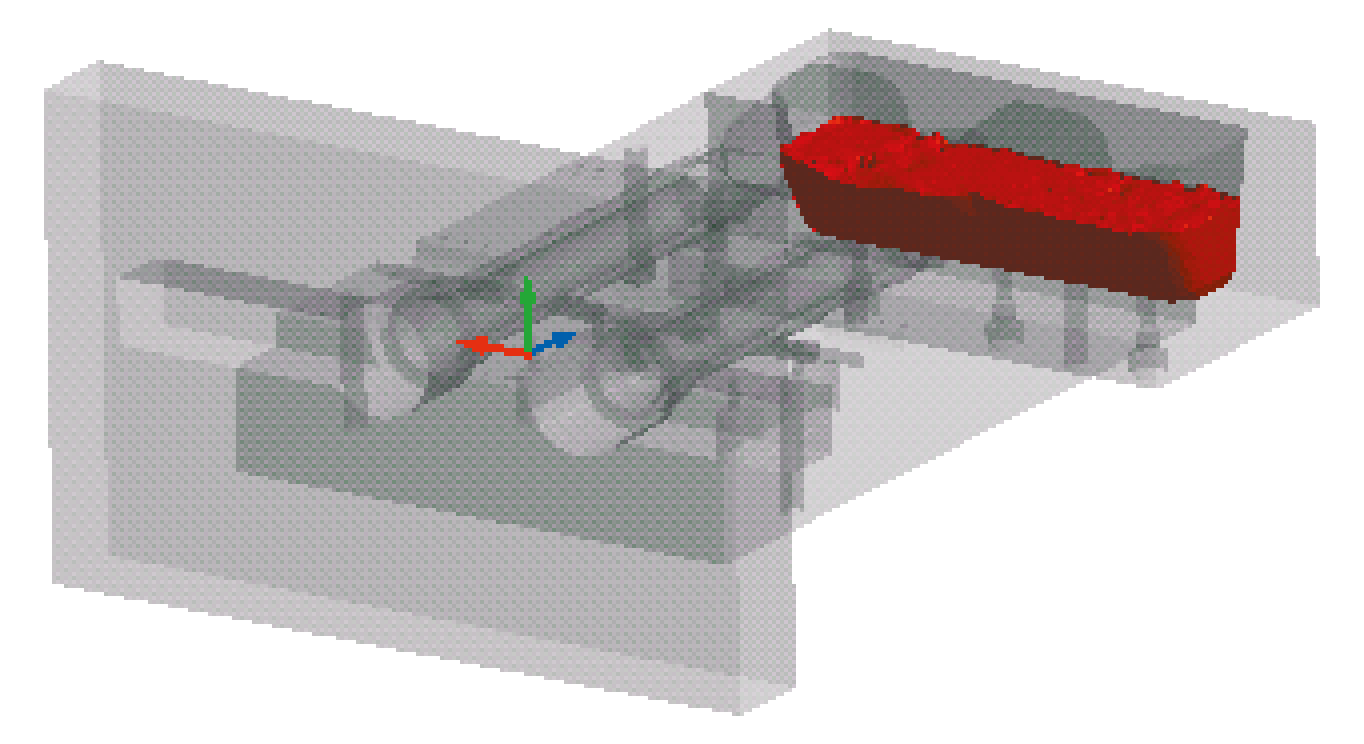
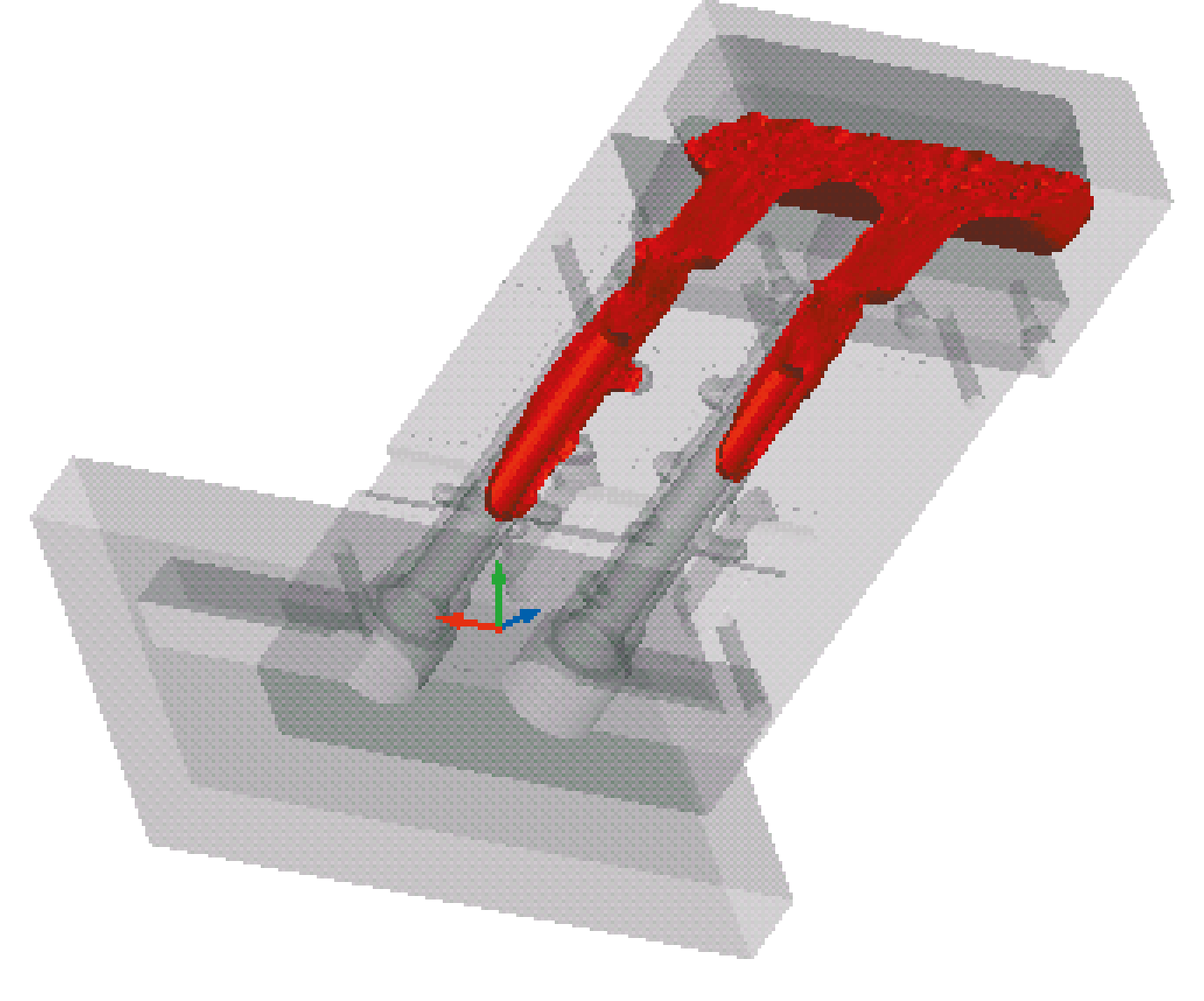
Ready for a license?
Looking for more information?