Equipment may contain defects, material deficiencies, cracks, breaks, corrosion and other defects. It may be the outcome of the FFS procedure:
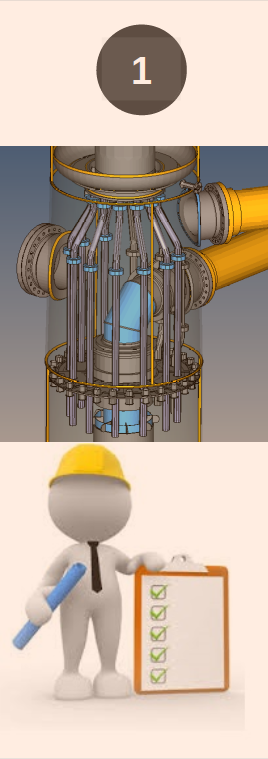
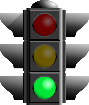
Operation can continue
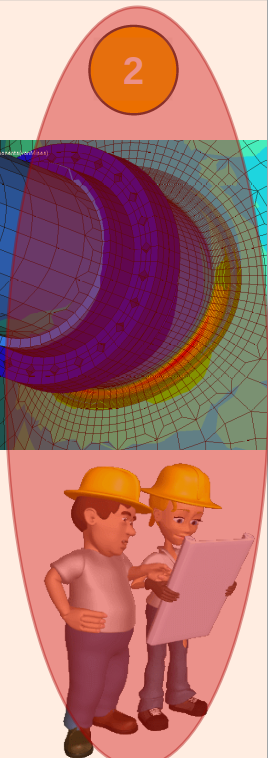
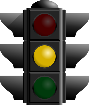
Remaining lifetime computation
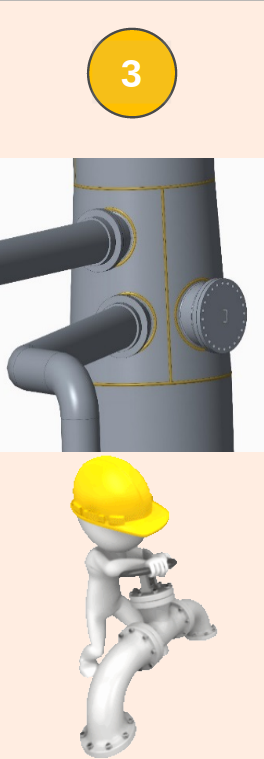
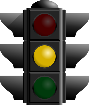
Modification of operating parameters
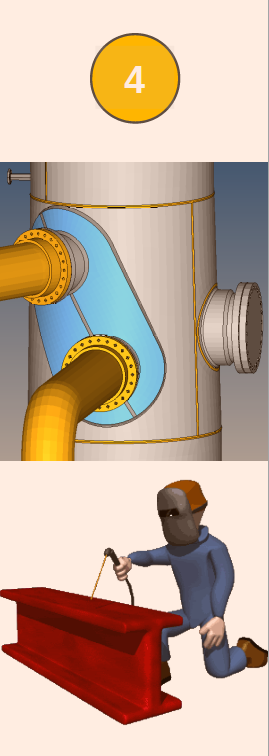
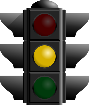
It can be operated after repair
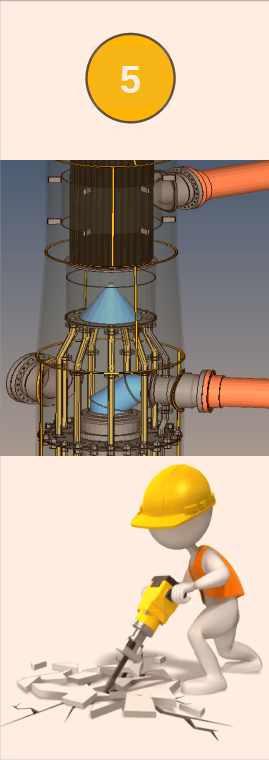
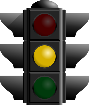
Conversion of equipment
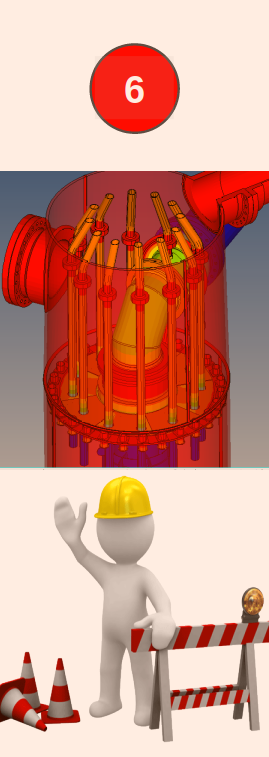
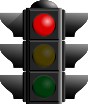
Equipment shut down
3 basic conditions of lifetime test procedures:
1. Stress Analysis: in order to be able to perform any kind of remaining life calculation, the exact stress distribution of the equipment must be determined (analytical, numerical methods). Independent or coupled differential equations of mechanics can only be solved with an approximate numerical method (finite element method) on complex geometries. The first step in any finite element strength analysis is the construction of an accurate 3D computer model (CAD) :
- elasticity theory
- heat conduction
- flow theory
2. Material Properties: It is essential to know the material characteristics of the equipment to be tested as defined in the standard, or in the absence of this, the properties determined by the measurement prescribed in the standard - shown at different environmental, temperature and load levels :
- the need for data from literature and material databases
- individual measurements (in case of base- and butt weld seams creep, tensile, fatigue tests, etc.)
- Mechanical properties (Rm ; Rp0,1 ; E ; Rm|T|t ; Rp0,1|T|t ; ET ; Sa ; T ; tr(T,s) ; …)
- material characteristics, permissible stress (s-e|T ; fnc ; ; ; … )
- safety factors, factors, parameters (SFc ,WSF, WSRF, FSRF, …)
- other physical and thermal technical characteristics required for analyses
2. Standard application: during the examinations, it is necessary to follow the governing standard of the field in question every time. In the absence of this, in the case of a given company, the so-called "house standards" are guidelines::
- MSZ, STN
- EN
- ASME
- BS
- API
- etc.
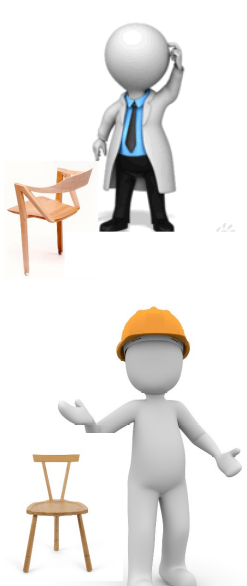